High Energy Mechanical Milling
2021-06-21T07:06:12+00:00
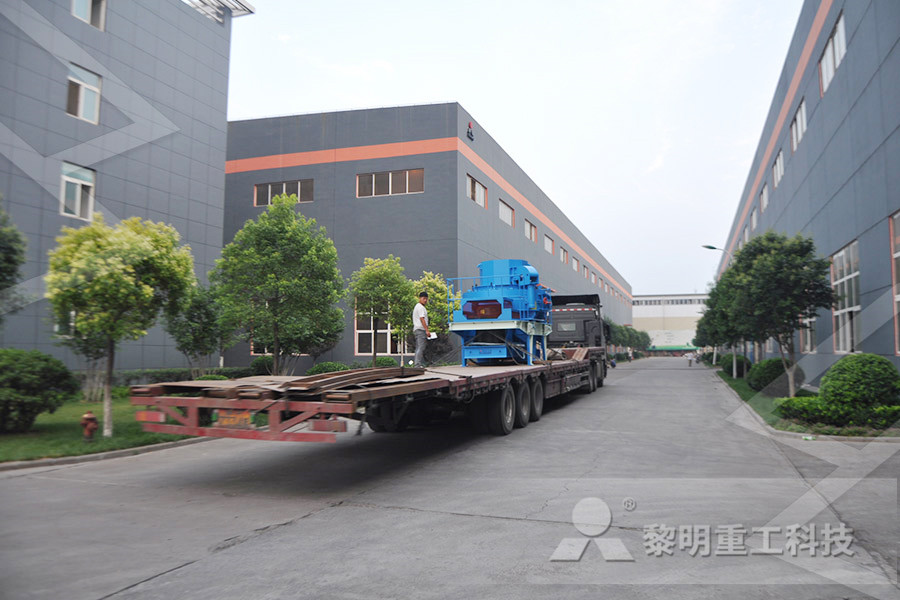
high energy mechanical milling, high energy
Alibaba offers 2,992 high energy mechanical milling products A wide variety of high energy mechanical milling options are available to you, such as local service location, key selling points, and applicable industries Highenergy mechanical milling has been performed on poly(methyl methacrylate) (PMMA) at ambient and cryogenic temperatures, as well as on polyisoprene (PI) and poly(ethylenealtpropylene) (PEP) at cryogenic conditions only Milling conducted at ambient temperature has a substantially greater impact on the molecular characteristics of PMMA than milling at cryogenic temperaturesHighenergy mechanical milling of poly(methyl The first industrial application of Mechanical Alloying (MA) has been introduced in Japan in October 1997 where in this case the processing is better to be described as High Energy Milling (HEM) In fact it is a very successful production of copper and bronze flakes within 3High Energy Milling / Mechanical Alloying / Reactive MillingRecently, the highenergy mechanical milling has been used for polymeric materials and it was detected that physical and chemical changes occur during milling In such case, powder of UHMWPE was milled in three types of mills: SPEX, attritor e planetary, in different times of millingHigh Energy Mechanical Milling Highenergy mechanical milling is a very effective process for synthesizing metal–ceramic composite powders as it allows incorporation of the metal and the ceramic phases into each powder particle, as shown schematically in Fig 6 In the initial stage, the microstructure of the composite powder particles is at the micrometer levelProcessing of advanced materials using highenergy
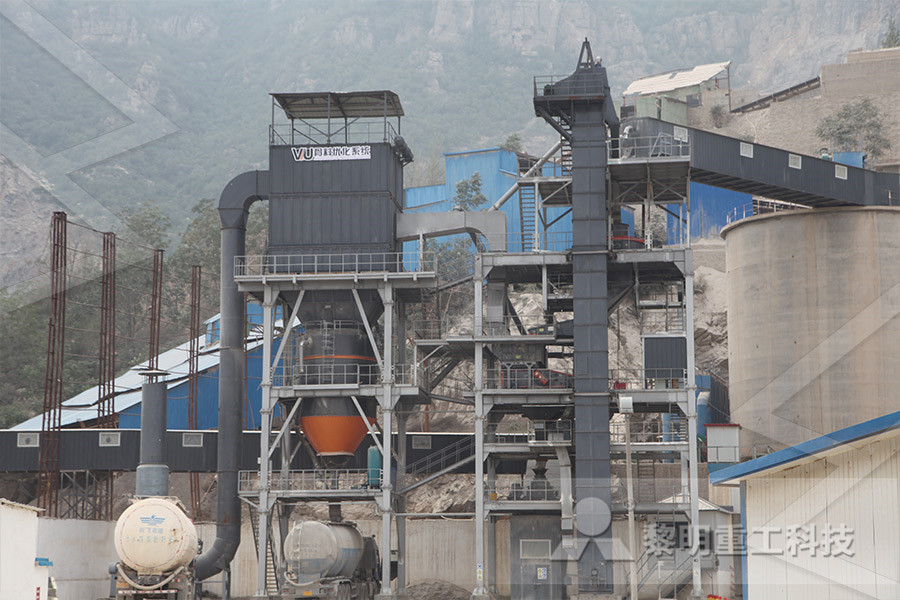
Effect of high‐energy mechanical milling on the
Effect of highenergy mechanical milling on glassy As x Se 100 − x (5 ≤ x ≤ 75) is recognized with Xray powder diffraction analysis applied to their diffuse halos ascribed to intermediate—and extendedrange structural ordering, which are revealed respectively in the first sharp diffraction peak (FSDP) and principal diffraction peak (PDP) ) Straightforward interpretation of the Effect of high‐energy mechanical milling on glassy As x Se 100 − x (5 ≤ x ≤ 75) is recognized with X‐ray powder diffraction analysis applied to their diffuse halos ascribed to intermediate—and extended‐range structural ordering, which are revealed respectively in the first sharp diffraction peak (FSDP) and principal diffraction peak (PDP)Effect of high‐energy mechanical milling on the Milling conducted at ambient temperature has a substantially greater impact on the molecular characteristics of PMMA than milling at cryogenic temperatures An increase in the milling time is accompanied by substantial reductions in PMMA molecular weight and, hence, glass transition temperature and impact strength under both sets of [PDF] Highenergy mechanical milling of poly ( methyl requisite to the use of mechanical alloying as a means of producing novel polymer blends Mechanical milling (involving one material) and mechanical alloying (involving two or more materials) generally refer to highenergy ballmilling techniques employed to process materials in the solid state [14]Highenergy mechanical milling of poly(methyl In mechanical milling (MM), a suitable powder charge (typically, a blend of elemental) is placed in a high energy mill, along with a suitable milling medium The objective of milling is to reduce the particle size and blending of particles in new phasesMechanical Milling: a Top Down Approach for the

Highenergy mechanical milling of poly(methyl
requisite to the use of mechanical alloying as a means of producing novel polymer blends Mechanical milling (involving one material) and mechanical alloying (involving two or more materials) generally refer to highenergy ballmilling techniques employed to process materials in the solid state [14]Milling conducted at ambient temperature has a substantially greater impact on the molecular characteristics of PMMA than milling at cryogenic temperatures An increase in the milling time is accompanied by substantial reductions in PMMA molecular weight and, hence, glass transition temperature and impact strength under both sets of [PDF] Highenergy mechanical milling of poly ( methyl Effect of highenergy mechanical milling on glassy As x Se 100 − x (5 ≤ x ≤ 75) is recognized with Xray powder diffraction analysis applied to their diffuse halos ascribed to intermediate—and extendedrange structural ordering, which are revealed respectively in the first sharp diffraction peak (FSDP) and principal diffraction peak (PDP) ) Straightforward interpretation of the Effect of high‐energy mechanical milling on the Ultrahigh molecular weight polyethylene (UHMWPE) is a polyethylene with a very long chain, which provides excellent features, however it makes the processing difficult due to high melt viscosity Many studies intend to found out means to make its processing easier Recently, the highenergy mechanical milling has been used for polymeric materials and it was detected that physical and chemical HighEnergy Mechanical Milling of UltraHigh The preparation of atomized ironbased powder which was oxidized at 500 ℃ by highenergy mechanical milling,and its grain fineness,surface morphology,and variation of microhardness were investigated by oxygen content,Xray diffraction(XRD),scanning electron microscope(SEM) and microhardness studiesThe result shows that after highenergy mechanical milling the change of oxygen content is not Highenergy mechanical milling of atomized iron
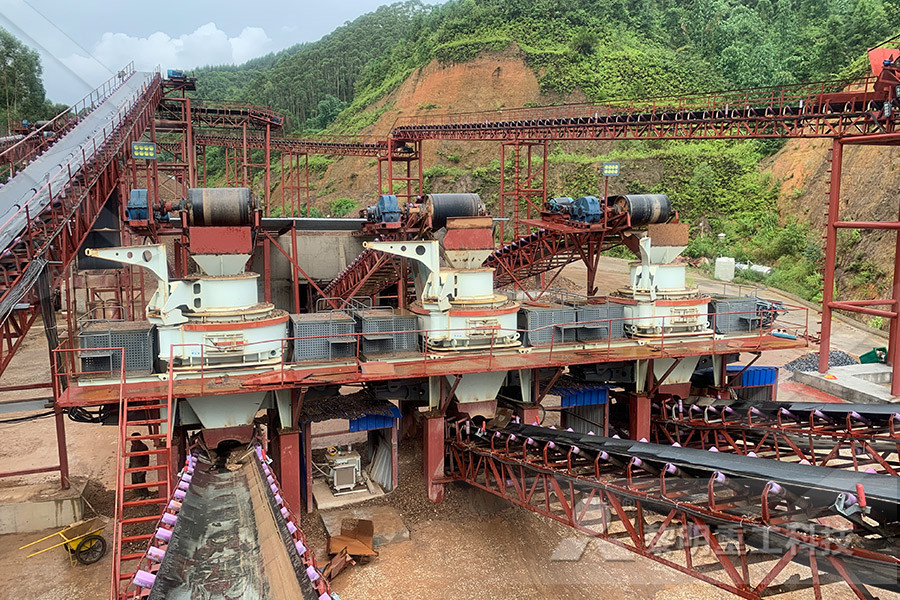
Highenergy mechanical millinginduced
Abstract Amorphous Fe 32 Ni 52 Zr 3 B 13, prepared by rapid solidification, undergoes crystallization during highenergy mechanical millingThe resulting structure consists of facecentered cubic (fcc) FeNi and Zr 3 Ni 20 B 6 nanocrystallites Structural evolution and defect analysis of assolidified Fe 32 Ni 52 Zr 3 B 13 ribbons with different milling times is investigated Fewlayer MXene has been proved to benefit superior electrochemical properties with a better ionic conductivity and twodimensional layer structure Herein, we report scale delamination of fewlayer MXene nanosheets as anodes for sodiumion batteries, which are prepared via an organic solvent assist highenergy mechanicalmilling methodFewLayer MXenes Delaminated via HighEnergy HighEnergy Ball Milling as a General Tool for Nanomaterials Synthesis and Processing Marzia Pentimalli , ENEA – Italian National Agency for New Technologies, Energy and Sustainable Economic Development, Technical Unit of Materials – Materials Chemistry and Technology Lab, Research Centre Casaccia, via Anguillarese, 301, 00123, Rome, ItalyHigh‐Energy Ball Milling as a General Tool for The high ball milling time could decrease the fragment size However, the amount of particle agglomeration with high cohesion could increase with a decrease of fragment size, resulting in the high resistance to fracture The size of W particle approaches a 'limit' as milling continues and maximum energy is expended At this time, the excess Effect of particle size and highenergy ball milling The influence of ball‐milling methods on microstructure and mechanical properties of silicon nitride (Si 3 N 4) ceramics produced by pressureless sintering for a sintering additive from MgO–Al 2 O 3 –SiO 2 system was investigated For planetary high‐energy ball milling, the mechanical properties of Si 3 N 4 ceramics were evidently improved and a homogeneous microstructure developedInfluence of Planetary High‐Energy Ball Milling on

Effect of high‐energy mechanical milling on the
Effect of highenergy mechanical milling on glassy As x Se 100 − x (5 ≤ x ≤ 75) is recognized with Xray powder diffraction analysis applied to their diffuse halos ascribed to intermediate—and extendedrange structural ordering, which are revealed respectively in the first sharp diffraction peak (FSDP) and principal diffraction peak (PDP) ) Straightforward interpretation of the Ultrahigh molecular weight polyethylene (UHMWPE) is a polyethylene with a very long chain, which provides excellent features, however it makes the processing difficult due to high melt viscosity Many studies intend to found out means to make its processing easier Recently, the highenergy mechanical milling has been used for polymeric materials and it was detected that physical and chemical HighEnergy Mechanical Milling of UltraHigh The preparation of atomized ironbased powder which was oxidized at 500 ℃ by highenergy mechanical milling,and its grain fineness,surface morphology,and variation of microhardness were investigated by oxygen content,Xray diffraction(XRD),scanning electron microscope(SEM) and microhardness studiesThe result shows that after highenergy mechanical milling the change of oxygen content is not Highenergy mechanical milling of atomized iron Highenergy mechanical milling of poly(methyl methacrylate), polyisoprene and poly(ethylenealtpropylene)(PDF) Highenergy mechanical milling of poly(methyl The particles themselves can have a size distribution of less than 100 nm, called a nanoparticle, or, as is common in materials milled using mechanical attrition, the product is highly crystalline, and the crystallite size after milling is between 1 HighEnergy Milling SpringerLink
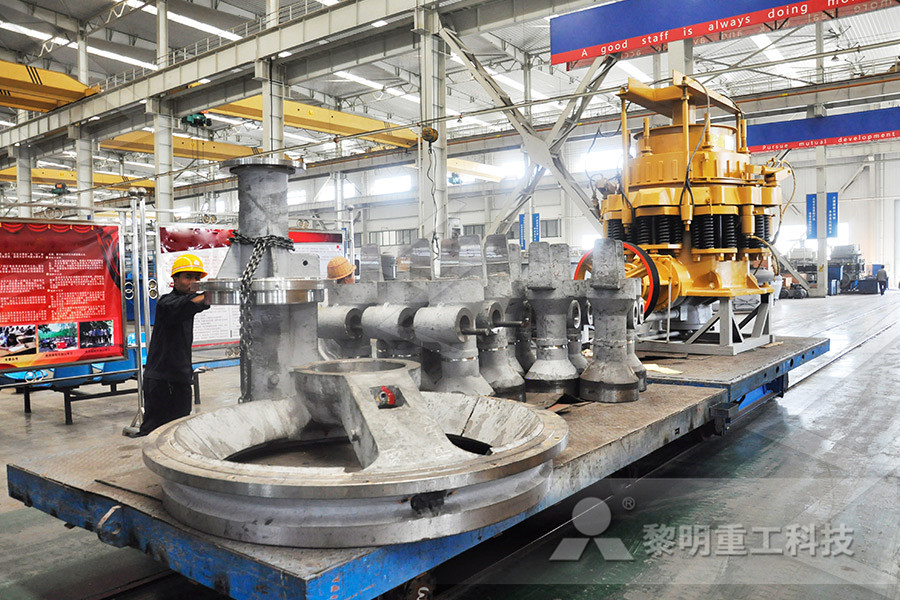
FewLayer MXenes Delaminated via HighEnergy
Fewlayer MXene has been proved to benefit superior electrochemical properties with a better ionic conductivity and twodimensional layer structure Herein, we report scale delamination of fewlayer MXene nanosheets as anodes for sodiumion batteries, which are prepared via an organic solvent assist highenergy mechanicalmilling method a high energy milling technique to produce the WCNi composite and study the effects of milling time in the material properties The milling of hard metal WC20Ni, was performed for milling times of 1, 2, 4, 8, 16, 32 and 64 hours The starting powders were characterized by laser sedigraphy, SEM and EDS Microstrutural analysisEffect of High Energy Milling on the Microstruture and In this paper, the milling parameters of high energy ball mill (Fritsch Pulverisette 7) like vial geometry, number and size of balls and speed of the mill were modelled and discussed Simulations through discrete element method (DEM) provide correlation between the milling parameters A mathematical model is used to improve and develop this processModelling of the HighEnergy Ball Milling Process High energy ball milling, matrix, reinforcement, hard phase, nanostructure, HVOF, wear resistance, cermet INTRODUCTION The high energy ball milling (HEM) process features a strong mechanical energy transfer into processed materials Thereby the production of pseudo alloys, which are not accessible by melting processes, isHIGH ENERGY BALL MILLING A PROMISING ROUTE FOR The NiO and Fe 2 O 3 powders were mixed by the highenergy ballmilling, followed by a sintering of the mixture at 1340°C for 05 h XRD, SEM, DSC, and size measurements were preformed to study the microstructure evolution in the highenergy ballmilled mixture and the sintered ones, as well It showed that the highenergy ballmilling processes resulted in a severe lattice distortion in the The Mechanical Alloying Behavior of Fe2O3 into NiO
- al mining heavy equipment
- Sketch Of Tornado Mill
- density separation by jigging
- belt st crushers brazil
- stone 2017 barite crusher plant price for sale
- Precision Grinders Nigeria
- Indian Corn Grinding Stone
- mobile limestone ne crusher provider di malaysia
- china mobile mining plant
- ball mill manufacturers handbook
- ball mill manual pdf maintenance
- why is quarrying limestone a bad thing
- platinum mining stocks
- nstruction aggregate production explained by flow chart
- Production Plant Fiber Basalt Design Construction
- sugar price of kohinoor sugar mills jauharabad today
- excuse letter sample attend meetingproject
- where to buy wet grinder Algeria 110 voltcrusher
- used nveyer belt for sale il
- solid minerals in nasarawa state
- used raymond al mills
- fob for bitumen pressure distributor
- Neral Water Treatment Plants
- grinders for sale from india
- boulder crusher part
- al gasification equipment
- gold revery equipment crusher
- modular flat plate curve nveyor belt nveyors for bulk materials
- produce of lor cement in cement mill
- Mobile Crush Stone Machine Ahmadabad