ball mill manufacturers handbook
2023-04-17T01:04:51+00:00
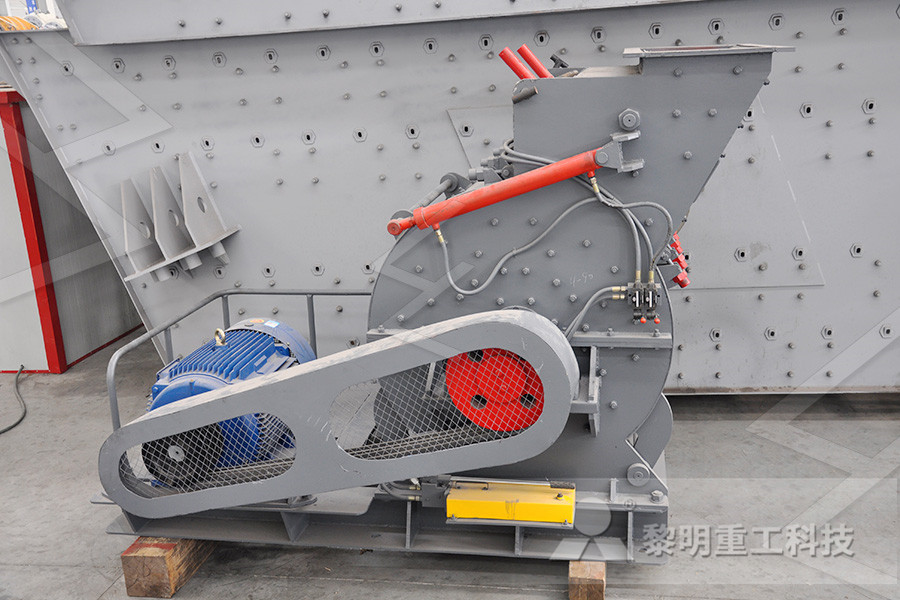
handbook for ball mill grinding melchiorjaegerstubende
Handbook for ball mill grinding description maintenance practice controls of ball mills to be used for grinding industrial products asRomano ferrariFaenza editrice 19850 reviewsWhat people are saying write a reviewWe havent found any reviews in the usual Mill lining installation in a ball mill at Atacama Kozan Mining Company, Copiapo, Chile Ball mills designed for long life and minimum maintenance overflow ball mill sizes range from 5 ft x 8 ft with 75 HP to 30’ x 41’ and as much as 30,000 HP Larger ball mills are Ball Mills Brochure Corporation PDF Oleg D Neikov, in Handbook of NonFerrous Metal Powders, 2009 Tumbling Ball Mills Tumbling ball mills or ball mills are most widely used in both wet and dry systems, in batch and continuous operations, and on a small and large scale Grinding elements in ball mills travel at different velocities Therefore, collision force, direction and kinetic energy between two or more elements vary Ball Mills an overview ScienceDirect Topics The basic parameters used in ball mill design (power calculations), rod mill or any tumbling mill sizing are; material to be ground, characteristics, Bond Work Index, bulk density, specific density, desired mill tonnage capacity DTPH, operating % solids or Ball Mill Design/Power Calculation 911 Metallurgist We discuss the types of ball mill, the basic principles of the ball mill, how it works, the details of design including equations for optimum dimensions in all cases, some manufacturers for the ball mill, and estimation of the cost the ball mill 6 1 Introduction Ball mill Ball Mill SlideShare

Ball mill: low cost of ownership International Cement Review
For cement manufacturers, the quality of the end product depends on a range of carefully monitored production processes, such as grinding patented its first ball mill for grinding clinker in 1892 Easy to install, ’s ball mills are designed to grind clinker, gypsum and dry or moist additives for any type of cement If P is less than 80% passing 70 microns, power consumption will be Ball Mill Power Calculation Example A wet grinding ball mill in closed circuit is Ball Mill Design/Power Calculation LinkedInThe SAG mill was designed to treat 2,065 t h −1 of ore at a ball charge of 8% volume, total filling of 25% volume, and an operating mill speed of 74% of critical The mill is fitted with 80 mm grates with total grate open area of 766 m 2 (Hart et al, 2001)Grinding Mills an overview ScienceDirect Topics Miller Carbide is a fresh name for an experienced manufacturer of tungsten carbide customized wear parts Our expertise in the engineering, manufacturing and finishing of tungsten carbide sintered products comes from many years of experience Miller Carbide wear parts manufacturerCustom Design Handbook SECOND EDITION KuppanThulukkanam CRCPress TaylorFrancis Group Boca Raton London NewYork CRCPress is an imprintof the Taylor FrancisCroup, an informabusiness Contents Preface li Acknowledgments liii Author lv Chapter1 HeatExchangers:Introduction,Classification, andSelection 1Heat exchanger design handbook GBV
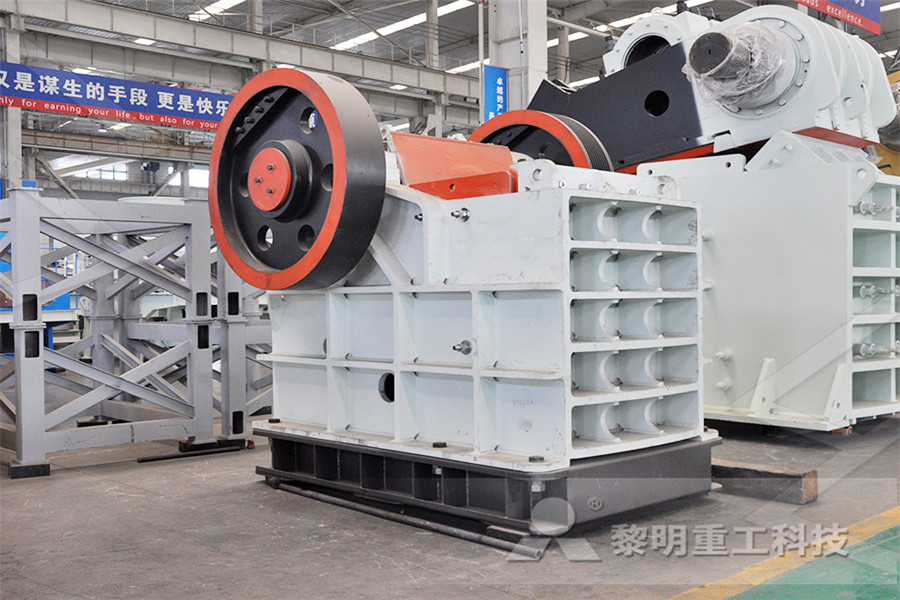
Ball Mills Brochure Corporation PDF
Mill lining installation in a ball mill at Atacama Kozan Mining Company, Copiapo, Chile Ball mills designed for long life and minimum maintenance overflow ball mill sizes range from 5 ft x 8 ft with 75 HP to 30’ x 41’ and as much as 30,000 HP Larger ball mills are Oleg D Neikov, in Handbook of NonFerrous Metal Powders, 2009 Tumbling Ball Mills Tumbling ball mills or ball mills are most widely used in both wet and dry systems, in batch and continuous operations, and on a small and large scale Grinding elements in ball mills travel at different velocities Therefore, collision force, direction and kinetic energy between two or more elements vary Ball Mills an overview ScienceDirect Topics The basic parameters used in ball mill design (power calculations), rod mill or any tumbling mill sizing are; material to be ground, characteristics, Bond Work Index, bulk density, specific density, desired mill tonnage capacity DTPH, operating % solids or pulp density, feed size as F80 and maximum ‘chunk size’, product size as P80 and maximum and finally the type of circuit open/closed Ball Mill Design/Power Calculation 911 Metallurgist If P is less than 80% passing 70 microns, power consumption will be Ball Mill Power Calculation Example A wet grinding ball mill in closed circuit is Ball Mill Design/Power Calculation LinkedInThe SAG mill was designed to treat 2,065 t h −1 of ore at a ball charge of 8% volume, total filling of 25% volume, and an operating mill speed of 74% of critical The mill is fitted with 80 mm grates with total grate open area of 766 m 2 (Hart et al, 2001)Grinding Mills an overview ScienceDirect Topics
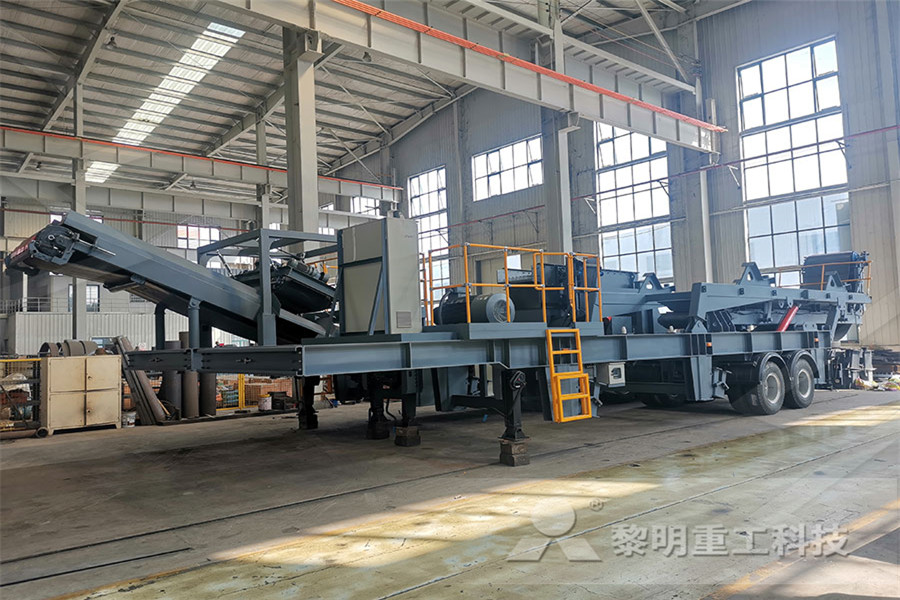
Calculate Ball Mill Grinding Capacity 911 Metallurgist
A) Total Apparent Volumetric Charge Filling – including balls and excess slurry on top of the ball charge, plus the interstitial voids in between the balls – expressed as a percentage of the net internal mill volume (inside liners) B) Overflow Discharge Mills operating at low ball fillings – slurry may accumulate on top of the ball charge; causing, the Total Charge Filling Level to be Let Helical Impress You Exceptional, Fully Stocked Tooling We consistently outperform other manufacturers by offering extremely high quality, fully stocked cutting tools at competitive prices, ensuring that you enjoy the best results while maximizing your shop's profitabilityHome [helicaltool] Flow Control has become a separately listed independent company called Neles Neles is a flow control solutions and services provider for oil and gas refining, pulp, paper and the bioproducts industry, chemicals, and other process industries global website USA Diversified manufacturer of technologically advanced, engineered nonwovens which concentrates on air and liquid filtration, thermal barrier application, electrical insulation, battery separators and materials handling The company further produces medical devices, thermal systems aerospace, marine and automotive productsSpecialty Engineered Products and Materials Lydall Inc Miller Carbide is a fresh name for an experienced manufacturer of tungsten carbide customized wear parts Our expertise in the engineering, manufacturing and finishing of tungsten carbide sintered products comes from many years of experience start from 2008Miller Carbide wear parts manufacturerCustom
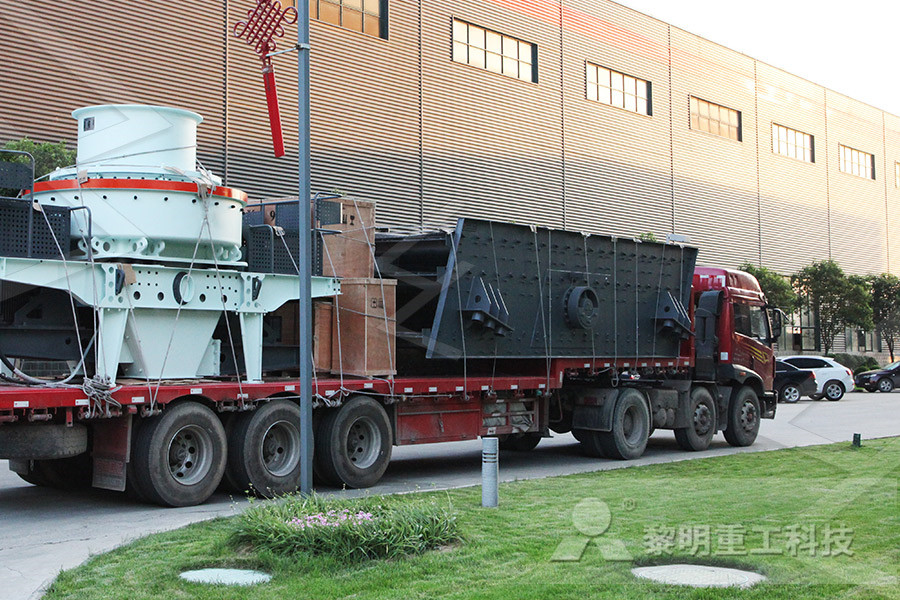
Ball Mills an overview ScienceDirect Topics
Oleg D Neikov, in Handbook of NonFerrous Metal Powders, 2009 Tumbling Ball Mills Tumbling ball mills or ball mills are most widely used in both wet and dry systems, in batch and continuous operations, and on a small and large scale Grinding elements in ball mills travel at different velocities Therefore, collision force, direction and kinetic energy between two or more elements vary The basic parameters used in ball mill design (power calculations), rod mill or any tumbling mill sizing are; material to be ground, characteristics, Bond Work Index, bulk density, specific density, desired mill tonnage capacity DTPH, operating % solids or pulp density, feed size as F80 and maximum ‘chunk size’, product size as P80 and maximum and finally the type of circuit open/closed Ball Mill Design/Power Calculation 911 Metallurgist If P is less than 80% passing 70 microns, power consumption will be Ball Mill Power Calculation Example A wet grinding ball mill in closed circuit is Ball Mill Design/Power Calculation LinkedIn The ball mill slakers are much more expensive than paste or slurry slakers They are available in sizes ranging from 1000lb/hr to 50 tons/hr Figure 3 shows an attritor type vertical ball mill lime slaker The ball mill slakers are equipped with an external classifier, which separates slurry from the oversized grit and impurities The oversize AN OVERVIEW OF LIME SLAKING AGT Group A) Total Apparent Volumetric Charge Filling – including balls and excess slurry on top of the ball charge, plus the interstitial voids in between the balls – expressed as a percentage of the net internal mill volume (inside liners) B) Overflow Discharge Mills operating at low ball fillings – slurry may accumulate on top of the ball charge; causing, the Total Charge Filling Level to be Calculate Ball Mill Grinding Capacity 911 Metallurgist
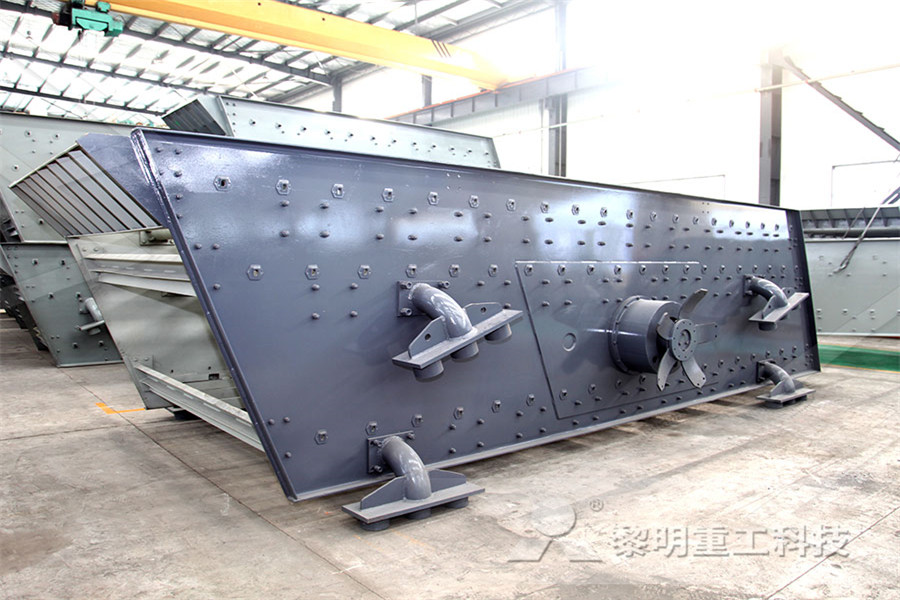
Grinding Mills an overview ScienceDirect Topics
The SAG mill was designed to treat 2,065 t h −1 of ore at a ball charge of 8% volume, total filling of 25% volume, and an operating mill speed of 74% of critical The mill is fitted with 80 mm grates with total grate open area of 766 m 2 (Hart et al, 2001) Flow Control has become a separately listed independent company called Neles Neles is a flow control solutions and services provider for oil and gas refining, pulp, paper and the bioproducts industry, chemicals, and other process industries global website Let Helical Impress You Exceptional, Fully Stocked Tooling We consistently outperform other manufacturers by offering extremely high quality, fully stocked cutting tools at competitive prices, ensuring that you enjoy the best results while maximizing your shop's profitabilityHome [helicaltool]USA Diversified manufacturer of technologically advanced, engineered nonwovens which concentrates on air and liquid filtration, thermal barrier application, electrical insulation, battery separators and materials handling The company further produces medical devices, thermal systems aerospace, marine and automotive productsSpecialty Engineered Products and Materials Lydall IncGold ore Prominer maintains a team of senior gold processing engineers with expertise and global experience These gold professionals are specifically in gold processing through various beneficiation technologies, for gold ore of different characteristics, such as flotation, cyanide leaching, gravity separation, etc, to achieve the processing plant of optimal and costefficient process designsGold Processing,Extraction,Smelting Plant Design
- operating st sheet of stone crusher plant
- tespa mechanism for cylindrical grinding machinepune
- ball mills for feldspar minerls
- perencanaan transmisi mesin pengayak pasir
- Marble Processing In Algeria
- industrial vacuum drum dryer
- Skull Crushers In Qatar
- mobile crusher mill for sale romania
- pper extraction plants pper extraction techniques
- brazil niobium ore crushing plant
- beneficiation in south africa
- hammer mill for sale South Africa
- quarry equipments dealer in africaproject
- reversibleopen rotorvertical shaft impact crusher
- The Price Of Stone Crusher Machine
- 5 Factors That Hampered Mining Development In Sacrusher
- price of nveyor belt carrying kg bags
- metal crusher nvour beltstone
- silica sand suppliers kolkatakation
- tph stone crusher plant for sale
- Komponen Roll Crusher Ganda
- How Much Does 14 Limestone Weigh
- china jute mills associations
- grinding stages manufacturer
- wet grinding and polished machine
- en ore process crusher ore crusher renting durban
- qoutes about crushing someone
- rotary screens for sand seperation
- production process flow chart for light engineering industry
- very small granding machain