produce of lor cement in cement mill
2022-12-23T07:12:30+00:00

White Cement Manufacturing Process AGICO White
Cement Mill The recommended cement mills in white cement production are vertical roller mills or ball mills The use of these two mills is conducive to reducing iron pollution in the white cement production process How Do We Improve Whiteness of White Cement The color of Portland cement is mainly influenced by its ratio of iron oxideColored Cement: the colored cement is manufactured by mixing the pigment with the ordinary Portland cement Its production mainly adopts the staining method and calcination method, the latter of which has a durable color but a high production cost This cement Portland Cement Manufacturing Process In Cement AF contains iron, cement chemists look at Fe 2 O 3 content in the oxide analysis when color is in question Concrete made with cement having a relatively high C 3 S content will tend to gain more strength and produce more heat of hydration at earlier ages, usually within the first week of placement A C 3 S content near 60% is on the high endC E M E N T CEMENT MILL TEST REPORTS: What Raw mill is generally called cement raw mill, raw mill in cement plant, it refers to a common type of cement equipment in the cement plantIn the cement manufacturing process, raw mill in cement plant grind cement raw materials into the raw mix, and the raw mix is sent to the cement kiln to make cement clinker, next, clinker and other admixtures will be ground into finished cement by cement millRaw Mill, Cement Raw Mill, Raw Mill In Cement Plant The temperature in cement kiln can reach 14001500℃, slurry in it is heated and dried and finally forming the clinker compounds, namely Dicalcium Silicate, Tricalcium Silicate, Tricalcium Aluminate and Tetra Calcium AluminoFerrite Clinker is a kind of particle with a variety of size and dark green colorWet Process of Cement Manufacturing Cement Wet
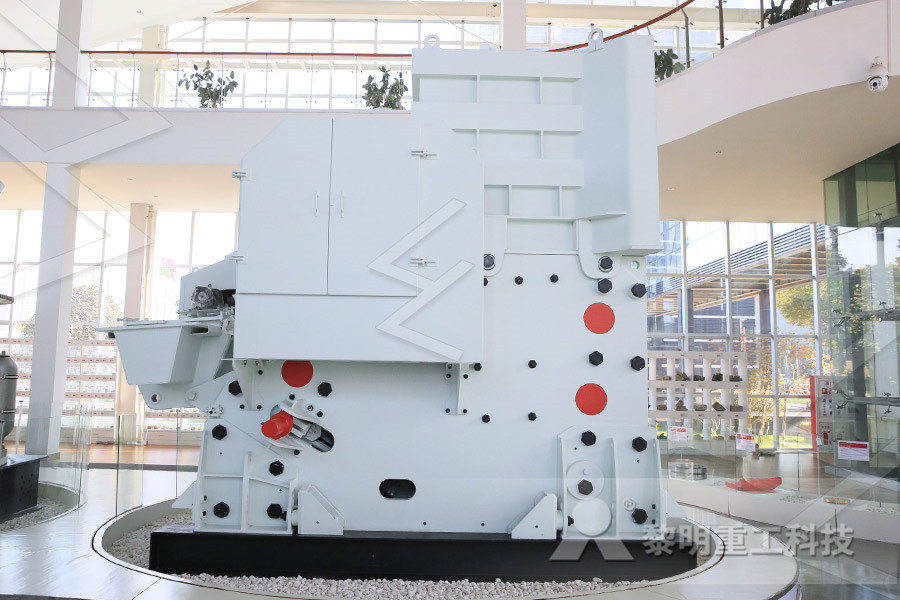
Research Article Effectiveness of the TopDown
the cement by stirring mill m Grinding of cement increases the surface area and decreases the In order to produce ultrane (submicro) cement using physicomechanical crushing (topdown) method, bead color of the used Zirconia beads are reported to be g/cc, g/cc, > In portland cement manufacturing process, the quality of cement clinker directly affects the quality of the finished product cement The following are several important factors affecting the cement clinker quality In the process of clinker production, strict control of these factors can ensure the production of highquality, highyield clinkerCement Clinker Quality Control During Clinker In order to produce raw materials preparation, clinker and rotary kilns are widely used in cement plants The objective of this study is to perform energy and exergy analysis of a raw mill (RM) and raw materials preparation unit in a cement plant in Turkey using the actual operational data The RM has a capacity of 829 tonmaterial hourlyEnergy and exergy analyses of a raw mill in a cement Jan , cement industry unidoOrg energy conservation technique in cement production process raw mill g weight of mill charge t a mill type in popular use is either a single barrel more detailed portland cement characteristics mill test certificates for cement, types i through cement type, watercement ratio, used to study raw materials, clinker, cementtypes of raw mill charge ratio in cement pdfWORKRITE® Colored Mortar Cement is a preblended packaged mortar cement Through careful selection and blending of the raw materials used to produce our cements, our quality control procedures deliver superior performance results during construction Applicable ASTM Specifications: C 1329 Standard Specification for Mortar CementMortar Cement – Colored – Workrite Cements
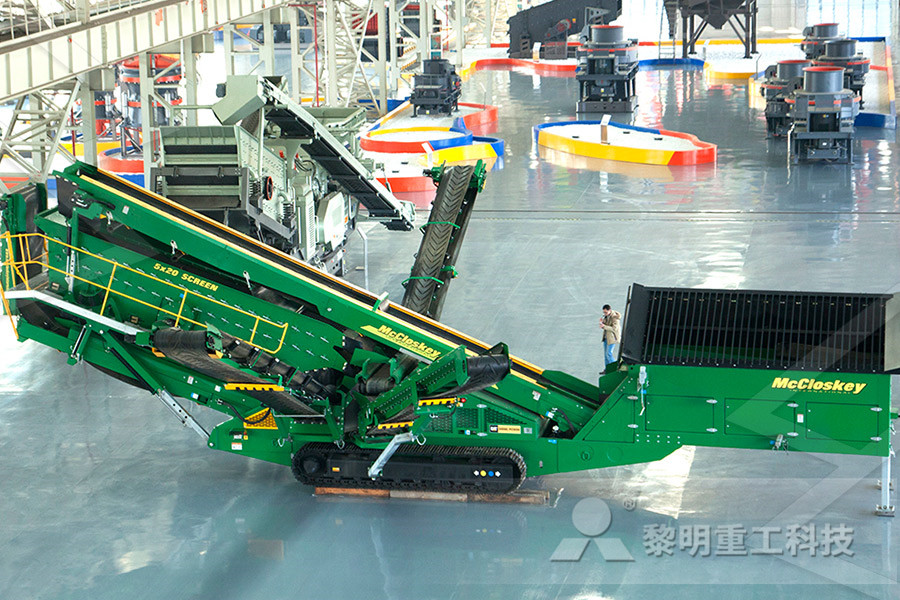
116 Portland Cement Manufacturing
116 Portland Cement Manufacturing 1161 Process Description17 Portland cement is a fine powder, gray or white in color, that consists of a mixture of hydraulic cement materials comprising primarily calcium silicates, aluminates and aluminoferrites More than 30 raw materials are known to be used in the manufacture of portland cement, and these Cement color analysis An important characteristic, although not part of the norm, presents a significant deviation which is the color of the cement Visual evaluation using the color plates verifieda limitation of RCR addition For aesthetic and cultural reasons, consumers tend to reject cements presenting reddish tonesRed ceramic industry residues: Used to produce Portland cementAF contains iron, cement chemists look at Fe 2 O 3 content in the oxide analysis when color is in question Concrete made with cement having a relatively high C 3 S content will tend to gain more strength and produce more heat of hydration at earlier ages, usually within the first week of placement A C 3 S content near 60% is on the high endC E M E N T CEMENT MILL TEST REPORTS: What All cement products are composed of specific combinations of calcium, silica, iron and alumina and small amounts of additives to achieve a desired profile of properties (eg, strength, color) Clinker, the principle intermediate manufactured product within cement production, is typically produced from a combination of ingredients, includingPORTLAND CEMENTThe temperature in cement kiln can reach 14001500℃, slurry in it is heated and dried and finally forming the clinker compounds, namely Dicalcium Silicate, Tricalcium Silicate, Tricalcium Aluminate and Tetra Calcium AluminoFerrite Clinker is a kind of particle with a variety of size and dark green colorWet Process of Cement Manufacturing Cement Wet
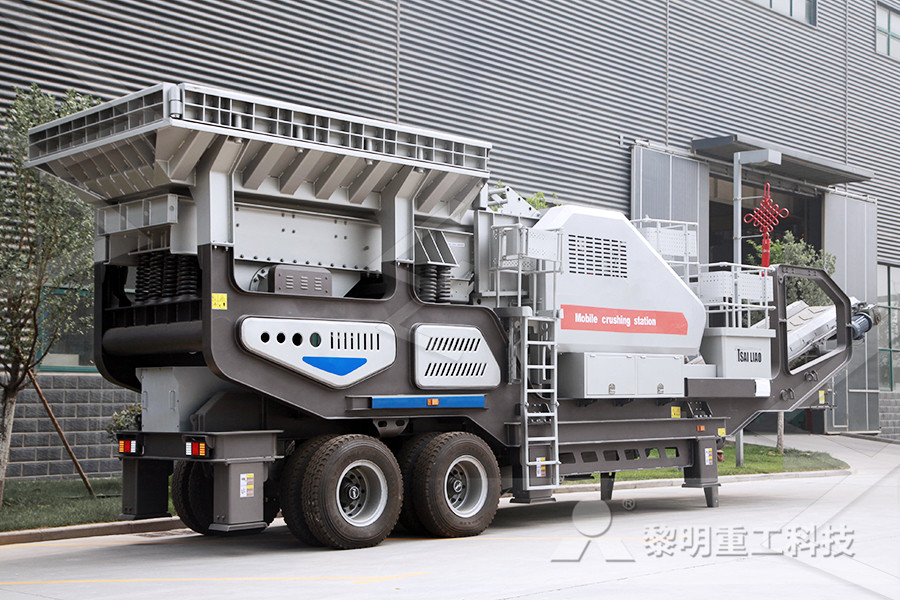
Research Article Effectiveness of the TopDown
the cement by stirring mill m Grinding of cement increases the surface area and decreases the In order to produce ultrane (submicro) cement using physicomechanical crushing (topdown) method, bead color of the used Zirconia beads are reported to be g/cc, g/cc, > The basic mixture needed to produce WSCB is much the same as WWCB, namely a mixture of wood fibres, cement and water in a 1:2:1 ratio (by dry weight) 9 The use of additives during the production of WSCB is also common Wood strand cement board differs from wood wool cement board mainly by density, which results from alterations to the Cement Boards 101 Global Cement Thus, for the production of the ultrafine cement using bead milling process, initially, the empty volume of the mill was filled with the ordinary Portland cement particle of the size 10–30 μm and allowed to grind in the mill by controlling the above parametersIn this study, grinding of the cement was done in the presence of the two different grinding agents, namely, methanol (CH 3 OH) and Effectiveness of the TopDown Nanotechnology in the Iron sources – Blast furnace flue dust, clay, mill scale, ore washings, shale Alumina sources – Alumina ore refuse, clay, copper slag, fly ash, shale The US industry average portland cement, as found by this study, is 922% clinker by weight Table 1 describes the cement’s composition by specific material resources Table 1Environm Ental Product dE claration The Portland Cement color analysis An important characteristic, although not part of the norm, presents a significant deviation which is the color of the cement Visual evaluation using the color plates verifieda limitation of RCR addition For aesthetic and cultural reasons, consumers tend to reject cements presenting reddish tonesRed ceramic industry residues: Used to produce
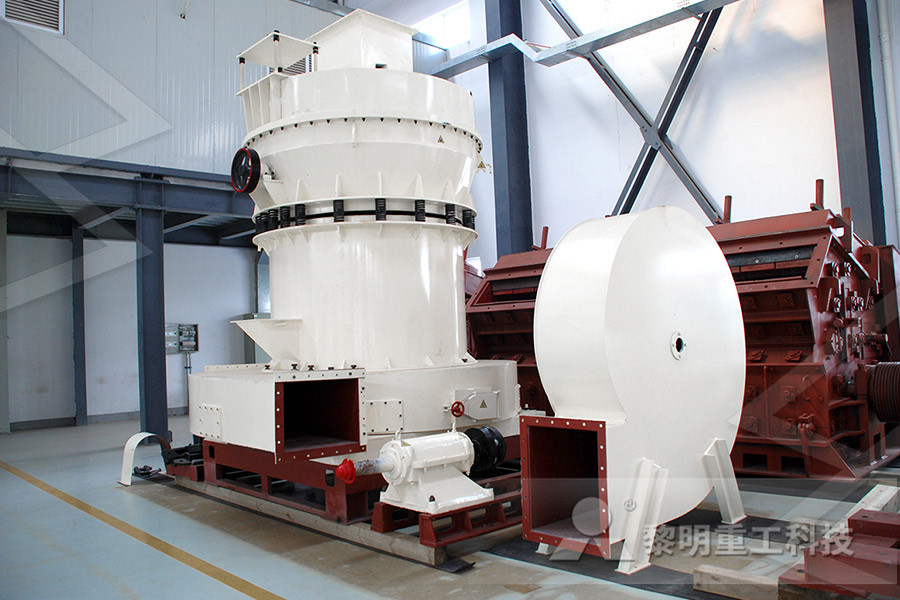
A Review On Environmental and Health Impacts Of
anhydrite) in a cement mill to control the properties of the cement Combinations of milling techniques including ball mills, roller mills, or roller presses are often applied to ground clinker with additives in cement mill The finished cement is being transferred via bucket elevators and conveyors to silo for storage [9] All cement products are composed of specific combinations of calcium, silica, iron and alumina and small amounts of additives to achieve a desired profile of properties (eg, strength, color) Clinker, the principle intermediate manufactured product within cement production, is typically produced from a combination of ingredients, includingMASONRY CEMENT ASTM It is possible to add some additive to Portland cement to produce the following types: (which give the grey color in ordinary Portland cement) China clay (white kaoline) is generally used, together with chalk or limestone, free a stone or ceramiclined mill The cost of grinding is thus higher, and this, coupled with the more expensive Chapter Two Types of Cement University of Technology, Gray cement obtains its color from raw materials that contain iron, manganese, chromium and magnesium oxides To produce white cement, manufacturers must use limestone or other raw materials that contain very low levels of these oxides White concrete cement must contain aggregates, such as marble, that do not add colorGray Cement vs White Cement Hunker Thus, for the production of the ultrafine cement using bead milling process, initially, the empty volume of the mill was filled with the ordinary Portland cement particle of the size 10–30 μm and allowed to grind in the mill by controlling the above parametersIn this study, grinding of the cement was done in the presence of the two different grinding agents, namely, methanol (CH 3 OH) and Effectiveness of the TopDown Nanotechnology in the
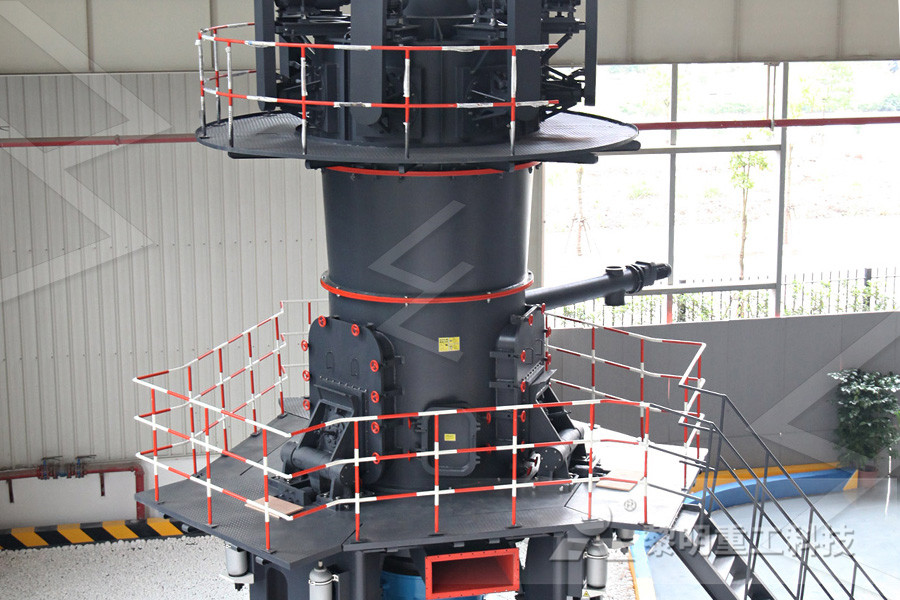
Wet Process of Cement Manufacturing Cement Wet
The temperature in cement kiln can reach 14001500℃, slurry in it is heated and dried and finally forming the clinker compounds, namely Dicalcium Silicate, Tricalcium Silicate, Tricalcium Aluminate and Tetra Calcium AluminoFerrite Clinker is a kind of particle with a variety of size and dark green color Iron sources – Blast furnace flue dust, clay, mill scale, ore washings, shale Alumina sources – Alumina ore refuse, clay, copper slag, fly ash, shale The US industry average portland cement, as found by this study, is 922% clinker by weight Table 1 describes the cement’s composition by specific material resources Table 1Environm Ental Product dE claration The Portland Cement plant locations and information on United States can be found below For full access to the database, purchase The Global Cement Report™, 13th EditionCement Plants located in United States CemNetI claim: 1 A manufacturing process for converting coal ash slag from a slagging coal gasifier into a marketable cement product having the characteristics and qualities of portland cement, which process comprises the steps of: transferring molten bituminous, semibituminous or lignitic noncoking coal slag having a temperature range between approximately 2800° F and 3600° F from a slagging Process for converting coal ash slag into portland
- sayaji stone crushers 20 x 12 hyderabad
- double ended grinding machines sale
- chromite spiral magnetic separator in south africa 45 crusher
- boda mpany hammer crusher
- washer sand jintai30sand
- crusher price Lung chen Mechanical
- ebay valve grinding machine
- diagram of a well label hammer pitch
- Trubaindo Coal Mining Tcm
- ne crusher vs Rock Jaw crushers
- vibrating nveyor working principle miningproject
- modifikasi mesin crusher
- Fitzmill Hammer Quarry
- grinding belt life
- roller mills ukrain
- Concrete Conveyor Range
- skip sander machine
- iron oreroyalty and excise duty
- price of send hand ice crusher
- instrumentation of sag mill
- mesin penggilingan batu
- project on dolamite mining
- mplete stone crushing plant used for sale
- kaolin clay philippines
- energy saving widely used mobile jaw crusher
- jaw crusher machine price in nignia
- industry chemicals services mpany
- what is magnetic separation in iron plant
- advantages of iron mining in south africaproject
- place where cinder mill sell