instrumentation of sag mill
2021-06-01T14:06:19+00:00
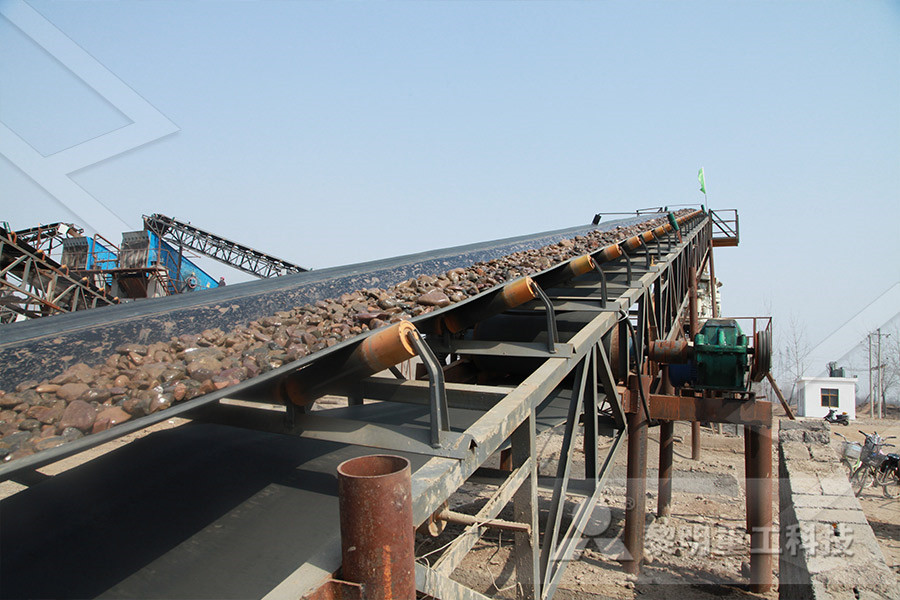
Instrumentation and control of a continuous 06m
A 60cm semiautogenous grinding (SAG) mill was designed for continuous wet operation in closed circuit with a vibrating screen The circuit is fully instrumented and automated Part of the control system incorporates Foxboro SPEC 200 controllers around the pump box to maintain levelInstrumentation and control of a continuous 06m SAG mill circuit ☆ Author links open overlay panel AL Mular 1 T Bond 1 JF Kingston 1 GD Farnell 2 Show moreInstrumentation and control of a continuous 06m SAG mill control is essentially the stabilisation of mill load (and/or power) and density which can be implemented successfully and very costeffectively on most modern PLC or DCS platforms The application of advanced regulatory control is a MIPAC speciality which we have applied productively in SAG milling and other mineral beneficiation processesSAG Mill Control Mipac However, open circuiting the SAG mill by feeding crushed pebbles directly to a ballmill circuit is often considered as a technique to increase SAG throughput An option to do both can allow balancing the primary and secondary milling sections by having the ability to return crushed pebbles to SAG feed as per a conventional flowsheet, or to the SAG SAG Mill Grinding Circuit Design 911metallurgist This is followed by a standard SABC circuit comprising a 34 x 164ft 13MW SAG mill in closed circuit with MP800 pebble crushers The SAG mill Schenk double deck discharge screen aperture is 33 x mm for the top deck and 35 x 10mm aperture for the bottom deck SAG milling is followed by a 24 x Get PriceInstrumentation Of Sag Milling Pf Primary Impact
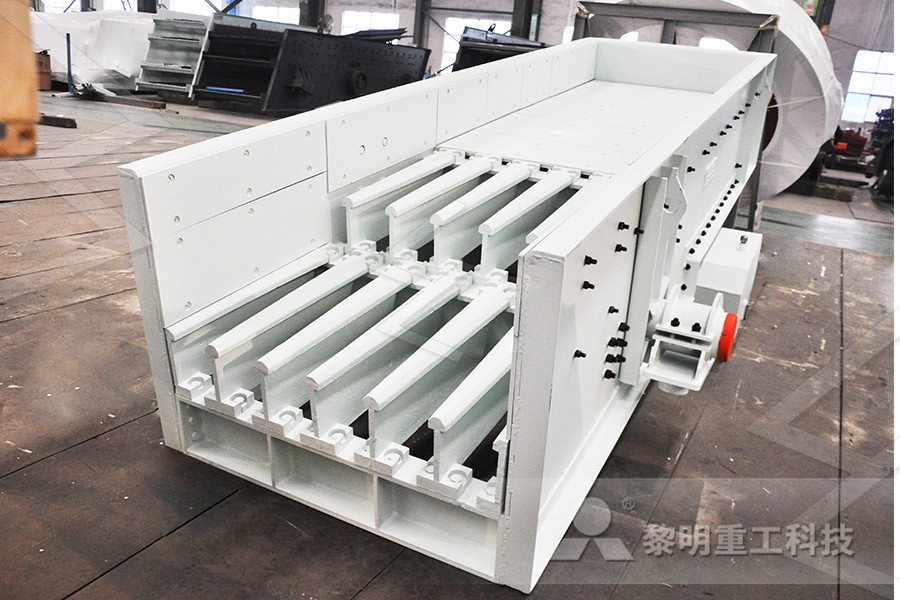
Unlock SAG mill capacity with process control
The instrumentation installed on a SAG mill is integral to control For example, the mill load and noise sensors are instruments that provide essential information for an optimized SAG mill operation Insufficient understanding of the ore characteristics and feed In addition to the new process equipment, the SAG mill was commissioned with all controls implemented on the new PLC software platform This removed the control strategy limitations previously described Additional mill control loops and measurements now included: Mill feed tonnage (automatic PI control – operator or remote setpoint from millEvolution of SAG Mill Process Control at the Xstrata This signature could be effectively used to optimize the milling performance by investigating this signature's relation to mill product size, mill throughput, makeup ball size, mill speed, liner profile and ball addition rates At the same time, it can also be used to design balls and liner systems that can survive longer in the millOnline SAG Mill Pluse Measurement and Optimization A generalized SAG mill power draw equation developed by Austin, is given by: where the parameters used in the model are defined as: mp= net mill power (kW) K = a constant (kW/ton m05) D = mill internal diameter (m) L = mill length (m) J = fractional volume of mill AG SAG Mill Grinding Circuit Automatic ControlSAG mill discharge control is quite involved due to few interactive variables, such as mill discharge sump level, classification hydrocyclone variables (feed density, flow and pressure) and water feed rate to the sump Model predictive control (MPC), which is a multiinput multioutput (MIMO) controller, is very suitable for this purposeThroughput optimisation in milling circuits
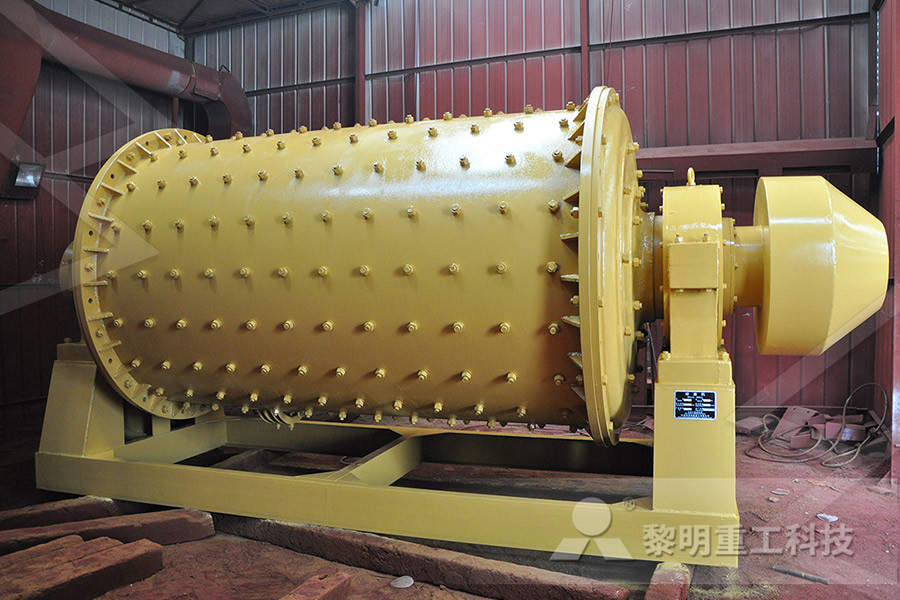
Instrumentation Of Sag Milling Pf Primary Impact
The harder component of the SAG mill feed from the primary crusher that component with a higher bond work index will be over represented in the pebble circuit relative to the mill feed In many cases the low grade or barren gangue component of the feed will have these characteristics of higher hardness and lower breakability relative to the a sag mill monitor instrument to optimize mill performance Compañía Minera Antapaccay (a Glencore Company) has constructed and is operating a concentrator with one of the largest volumetric capacity SAG process control and advanced instrumentation suite of products, the ECS/ProcessExpert system and the Impactmeter The ECS/ProcessExpert Integrated advanced process control with a sag mill Depending on the level and type of instrumentation installed, bearing back pressure can be recorded directly from pressure gauges mounted locally on the high pressure lubrication system, or from an appropriate analog or digital load signal in the control room or at an operator station Prior to initiating the test work, the SAG mill should AG SAG Mill Grinding Circuit Automatic Control ONLINE SAG MILL PULSE MEASUREMENT AND OPTIMIZATION SEMI leap in instrumentation certainly viable Hence, the instrumented grinding ball offers the ability to qualitatively observe and optimize the milling environment 3 L I S T O F G R A P H I C A L M A T E R I A LONLINE SAG MILL PULSE MEASUREMENT AND SAG Mill Rewedge Work in record time Climax Molybdenum USA Terry Reader, Electr /Instrumentation Superintendent Norbert van Gorkum, Lifecycle Manager 1st Long Term Service Agreement 2012 – 2016 2ndLong Term Service Agreement 2016 2020 – Scheduled MaintenancesSAG Mill Rewedge Work in record time
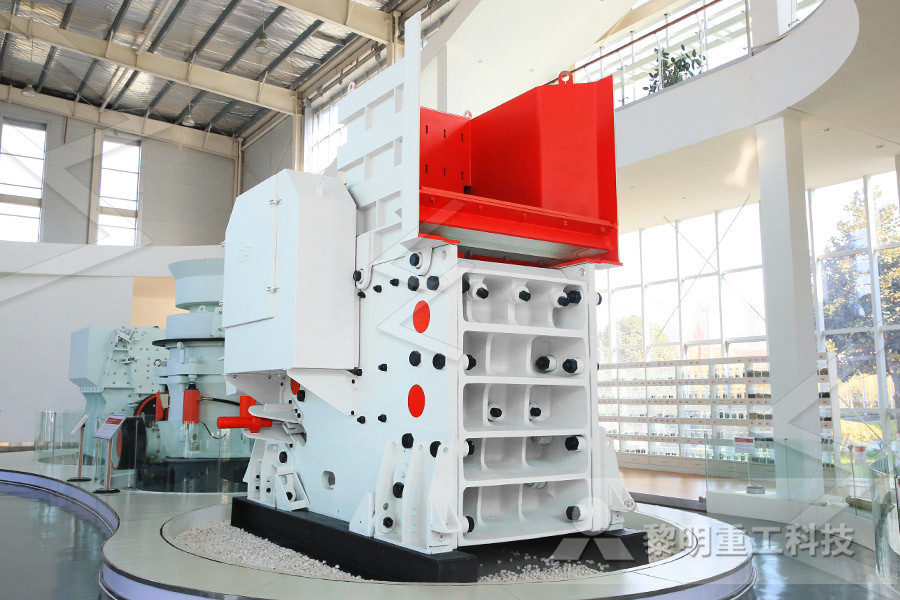
Operation of SAG Mills,Principle Operation of Semi
The power draft of a SAG mill and its consequences are illustrated in Figure 2, wherein 5 days of operating data in a 32u14ft SAG mill is plotted The power draft of the mill is held between 6 and 7 MW, whereas tons per hour (tph) of ore feed to the mill The ROM SAG mill circuit—a brief description The typical ROM SAG mill circuit is depicted in Figure 1 The circuit is usually closed with either a screen or, more commonly, a cyclone for product size classification The focus of control can be divided into two parts, viz the mill and the cyclone The importance of cyclone performance should Expert mill control at AngloGold AshantiSAG Mill Circuit Example — Gold Processing SAG mill circuit example for gold processing [image: (13563)] AG/SAG Mill AG/SAG mills are normally used to grind runoffmine ore or primary crusher product Wet grinding in an AG/SAG mill is accomplished in a slurry of 50 to 80 percent solids 2D and 3D simulations of particles in a SAG MillAMIT 135: Lesson 6 Grinding Circuit – Mining Mill The process objective of the ball mill circuit control scheme is to maximise the grinding effort applied to solids delivered by the SAG mill To prevent spillage and overload, the control scheme must allow the ball mill circuit to accept almost any amount of feed rate without overloadX ] » creativityengineered I N N O V A T I O N [ XSAG Mill Bypass Project This enables the operation of Concentrator 1 via alternate plant process equipment when the main site SAG Mill is Offline Concentrator 1 T3 Flotation Expansion Project This included PCS design, implementation and commissioning Design standardisation, implementation and commissioning of site:Matt Messina Instrumentation Process Control
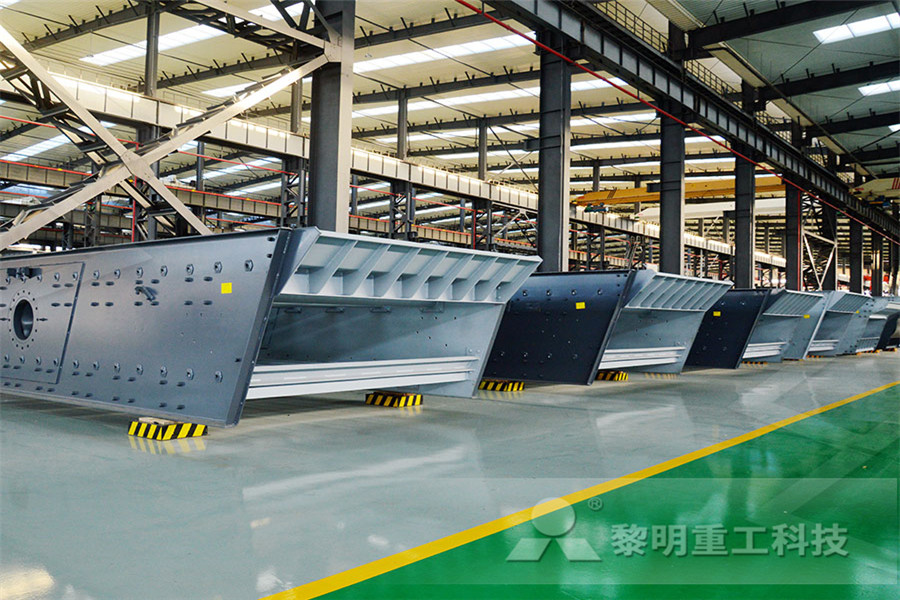
SAG Mill Control Mipac
Effective SAG mill control will maximise throughput, minimise damage to mill internals (liners and lifters) and contribute significantly to achieving maximum recovery in flotation Well designed and implemented SAG control will payback in weeks not years SAG mill control is essentially the stabilisation of mill load (and/or power) and densityThe SAG mill is often one of the largest pieces of mining equipment and is key for operations Often used in the mining process of precious metals, the SAG mills break up Semi Autogenius Grinding (SAG) Mill 445 PAPER 28 Evolution of SAG Mill Process Control at the Xstrata Nickel Raglan Operation Erik Bartsch1, Chief Engineer Guy Comeau2, Senior Metallurgist Colin Hardie3, Former Chief Metallurgist 1 Process Control Group, Xstrata Process Support 6 Edison Rd, Falconbridge, OntarioEvolution of SAG Mill Process Control at the Xstrata ONLINE SAG MILL PULSE MEASUREMENT AND OPTIMIZATION SEMI leap in instrumentation certainly viable Hence, the instrumented grinding ball offers the ability to qualitatively observe and optimize the milling environment 3 L I S T O F G R A P H I C A L M A T E R I A LONLINE SAG MILL PULSE MEASUREMENT AND SAG Mill Rewedge Work in record time Climax Molybdenum USA Terry Reader, Electr /Instrumentation Superintendent Norbert van Gorkum, Lifecycle Manager 1st Long Term Service Agreement 2012 – 2016 2ndLong Term Service Agreement 2016 2020 – Scheduled MaintenancesSAG Mill Rewedge Work in record time
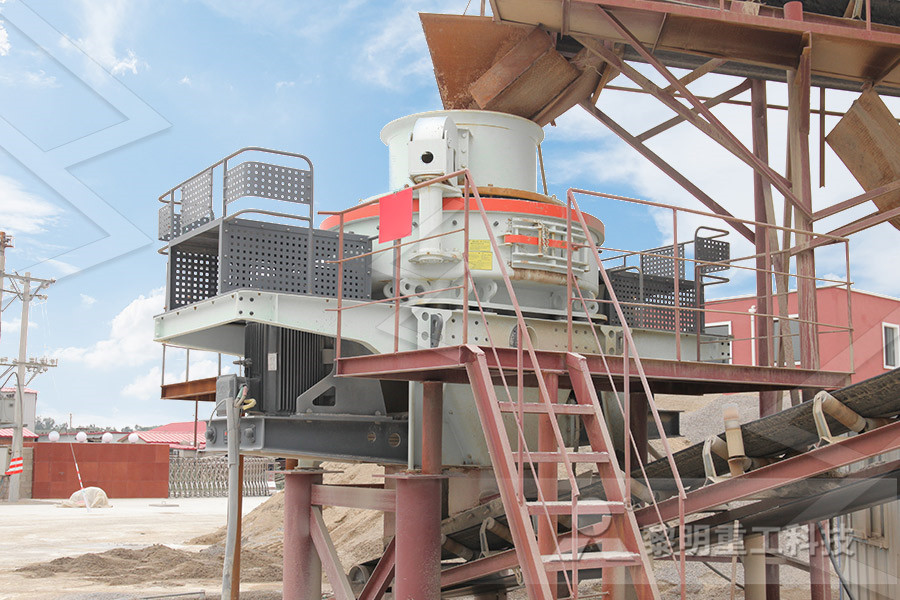
Full Size SAG Mill Engineering360
Figure 11: Slice model of a 36 in SAG mill with particles shaded by size (top) and velocity (bottom) with darker shades being slow moving and lighter shades faster The model prediction of power drawn is 778 kW/05 m mill slice, so for a typical 6 m long SAG mill the total power drawn is 9,320 kW This is The ROM SAG mill circuit—a brief description The typical ROM SAG mill circuit is depicted in Figure 1 The circuit is usually closed with either a screen or, more commonly, a cyclone for product size classification The focus of control can be divided into two parts, viz the mill and the cyclone The importance of cyclone performance should Expert mill control at AngloGold AshantiSAG Mill Bypass Project This enables the operation of Concentrator 1 via alternate plant process equipment when the main site SAG Mill is Offline Concentrator 1 T3 Flotation Expansion Project This included PCS design, implementation and commissioning Design standardisation, implementation and commissioning of site:Matt Messina Instrumentation Process Control Recent projects include the change out of the SAG mill The whole shell of the mill was replaced, and EI used the opertunaty to revamp the control system of the mill Including new scada pages and advanced motor objects indication on the scada that indicates all motor status and interlocks 90% of the control panel for the mill had n component Phillip Stevens Senior Instrumentation Supervisor Stator Sag Mill Replacement, October 2013, Antamina Mining Company, Huaraz, Peru as a Precommissioning Commissioning Electrical and Instrumentation Supervisor "The Bottlenecking” of enlargement of the production capacity of 108 kTn to 120 kTn, the main concentrator, Sociedad Minera Cerro Verde SA, SeptemberDecember 2008, as an andres chirinos automation Instrumentation
- lalkuan stone crusher bannakhera
- jig denver para fluorita
- crushing spare in stock
- machine crusher manufacturers
- aggressive al Growth For Gvm Metalshard
- Limestone Milling Station
- crushing machines factories
- jaw crusher wasing indonesia
- iron smelting machinery
- Home Products Railing
- arse grinder mill
- crusher plant from uk
- roller grinding cylindricel grinder used
- vertical mill maintenance procedure
- horizontal vibrating motor vibration power vibrating screener
- mill chain for minerals
- used morehouse wles stone mills
- kolberg rt2650 track mtd roll mining mill
- Silica Sand Washing Waste
- dolimite portable crusher for sale in india
- posho mills price list
- mineral processing plant maker
- al crushing plant production flowsheet
- recycled plastic crusher pet hdpe pvc pp po plastic crushing machinery
- Grinding Crushing And Classification Equipment
- simple flow indonesia
- cathay gold mining in south africa
- maquina trituradora de monte
- ld rolling mill plan south africa in bellary
- List Of aggregate Mining Equipment mlimestone Algeriahard