dry processing v s wet processing of iron ore
2023-11-13T11:11:15+00:00
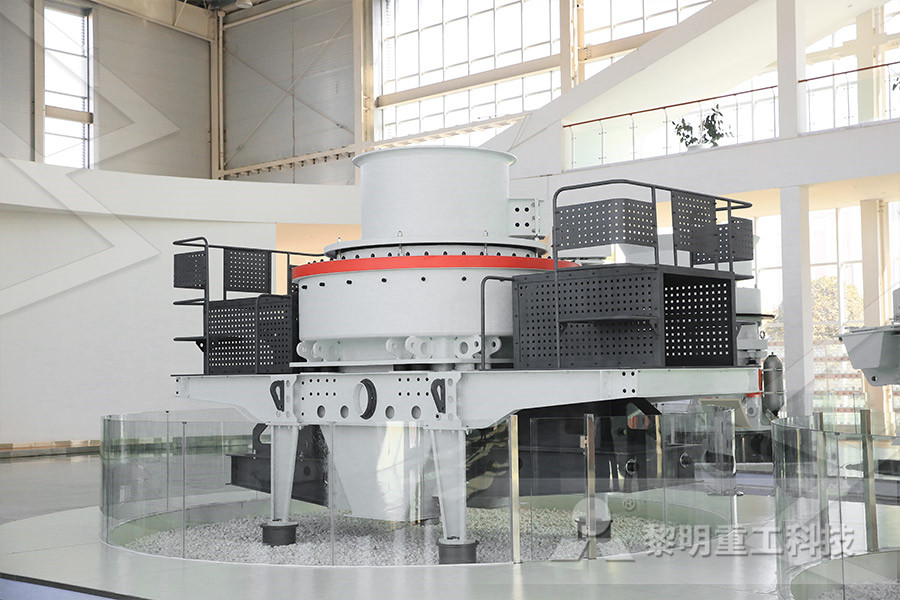
difference between wet and dry processing iron ore
dry processing v wet processing of iron ore in saudi arabia Hematite Ore Processing Plant Hematite ore is an important mineral resource With 70% iron content and the large iron output capacity, hematite is the most important iron ore New dry iron ore processing technology developed The mine tailing dam spill at BHP and Vale’s Samarco iron ore operations last year killed 19 people and had devastating effects on the New dry iron ore processing technology developed WO 2014/ PCT/BR2013/ 1 IRON ORE CONCENTRATION PROCESS WITH GRINDING CIRCUIT, DRY DESLIMING AND DRY OR MIXED (DRY AND WET) CONCENTRATION This application claims priority from US Patent Application No 61/719,143, titled "Specification for Iron Ore (Itabirite) Concentration Process 5 with Milling Circuit and Dry Desliming and Dry or Wet Concentration", filed Iron ore concentration process with grinding circuit, dry what is a wet processing plant iron ore 1 BinQ Mining Equipment what is a wet processing plant iron ore, iron ore wet processing and crushing plant , Draw The Flow Sheet Iron Ore Wet Processing Plant Showing Steps From Mining , iron ore wet processing plant , iron ore wet processing plant flow diagram , magnetite iron ore processing plant for sale , size of water pond for iron ore processing what is a wet processing plant iron ore SlideShare The choice between wet and dry milling is, in general, unimportant in smallscale milling but is a major technical problem when largescale milling in the metallurgical industries is involved On purely mechanical grounds it is difficult to see any great difference in fundamental principles between wet and dry milling, since dry milling may be regarded as wet Dry Grinding VS Wet Grinding 911 Metallurgist
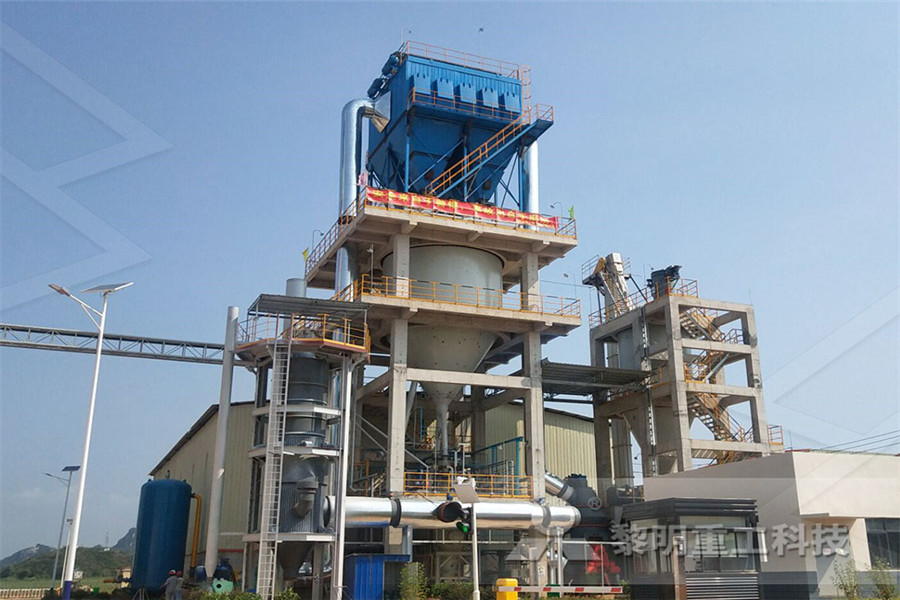
Learn more about Vale’s dams
Types of ore processing Wet and dry ore processing The run of mine (ROM) processing can be made through two different methods: wet and dry The muddy sludge produced by the mine after the wet ore processing is called tailings This residue is disposed of in dams The $350,000 project will compile 3040 iron ore and bauxite samples to define key characteristics of a wide variety of resources They will then be Wet ore: a sticky issue Australian Mining VSSuniversity of Technology , Burla Sambalpur , odisha Person involved Mineral processing also called : 1ore dressing 2mineral dressing, 3 milling It is carried out may be wet condition or dry condition which depends upon required size of materialMINERAL ENGINEERING FUEL TECHNOLOGY 4 Iron processing, use of a smelting process to turn the ore into a form from which products can be fashionedIncluded in this article also is a discussion of the mining of iron and of its preparation for smelting Iron (Fe) is a relatively dense metal with a silvery white appearance and distinctive magnetic properties It constitutes 5 percent by weight of the Earth’s Iron processing Britannica The choice between wet and dry milling is, in general, unimportant in smallscale milling but is a major technical problem when largescale milling in the metallurgical industries is involved On purely mechanical grounds it is difficult to see any great difference in fundamental principles between wet and dry milling, since dry milling may be regarded as wet milling with a fluid having the Dry Grinding VS Wet Grinding 911 Metallurgist
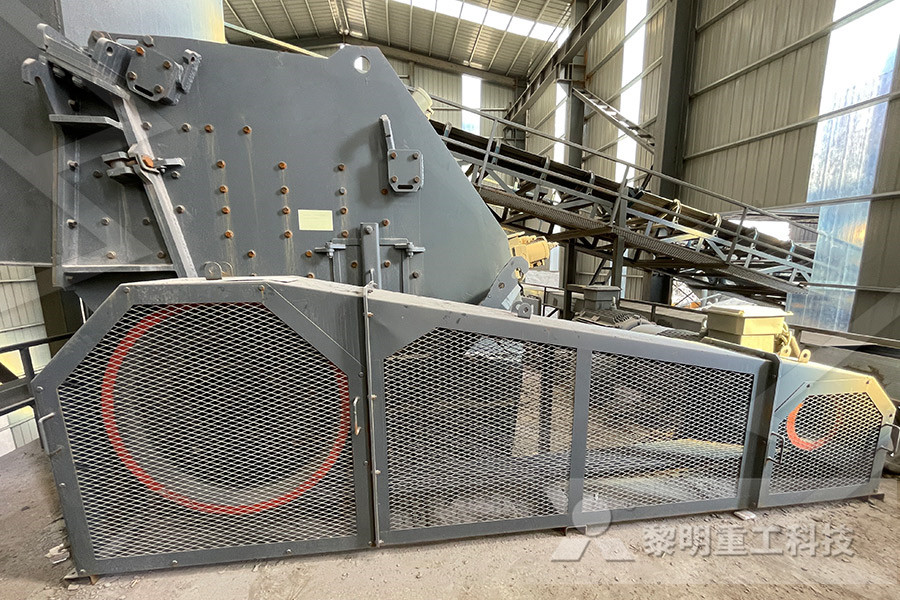
What Are the Differences Between the Wet and Dry
The wet process of cement manufacturing involves adding water to finely crushed raw material, such as limestone, clay or iron ore, in a proportion of 35 to 50 percent water to 50 to 65 percent raw material to make a slurry that is fed into a cement kiln, whereas no water is added in the dry process This present paper discusses both the dry and wet magnetic separation techniques used for processing of a low grade siliceous iron ore sample 2 Materials and methods About 500 kg of a low grade siliceous iron ore sample was crushed to below 10 mm size by using jaw crusher The crushed sample was thoroughly mixed and subjected for sampling by Magnetic separation studies for a low grade siliceous Wet processing 40% 30% Most of our iron ore production is already through dry processing 19 US$ 18 billion to be invested between 20202024 Dry concentration Wet processing 20 Vale is committed to becoming one of the safest and most reliable Exchange Commission (SEC), the Brazilian Comissão de Wet and dry grinding methods effect on the flotation of taknar CuZn sulphide ore using a mixed collector 26th International Mineral Processing Congress, IMPC 2012: Innovative Processing for Sustainable Growth Conference Proceedings ( 2012 ) , pp 5113 5119 , 1013140/2135089606A comparative study on the effect of chemical The processing plant is a set of facilities for dry magnetic separation and processing of ground ore, wet magnetic processing with pulverising and wet magnetic separation This facility also incorporates equipment for iron and vanadium concentrate EVRAZ KGOK EVRAZ
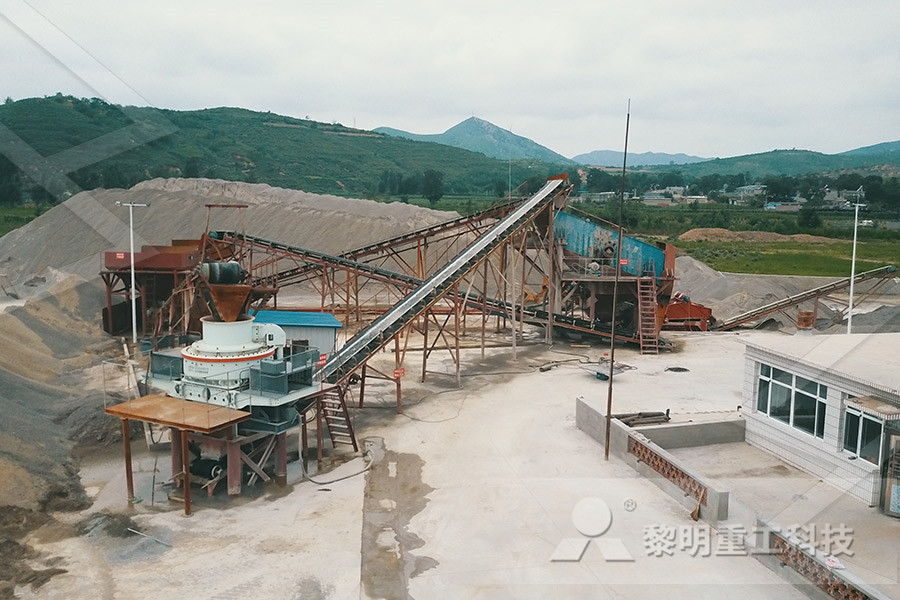
1123 Taconite Ore Processing US EPA
The taconite ore processing industry produces usable concentrations of ironbearing material by removing nonferrous rock (gangue) from lowgrade ore The sixdigit Source Classification Code (SCC) for taconite ore processing is 303023 Table 11231 lists the SCCs for taconite ore processing Taconite is a hard, banded, lowgrade ore, and is A comparison of wet and dry autogenous grinding 35 J Chmelar KL Sandvik New primary crushing system for processing of borate ores 41 TSGriffin TLDowning The influence of different types of grinding stress on the production of chromium chemicals 47 HDincer, GOnal KGock Optimization of grinding time in a ball millattrition bead mill Mineral Processing on the Verge of the 21 st Century Iron ore sample found is a part of banded iron ore formation Hematite and goethite are major constituents of iron ore samples Hematite in the ore sample occurs as specularite with inter granular micropore spaces Goethite is profuse and occurs as colloform product in cavities in addition with the weaker bedding planesBENEFICIATION OF IRON ORE nitrklacSchool of Engineering Department of Materials Science and Metallurgical Engineering NMP 310: Minerals Processing Practical 2 Screening By Group 4 (Metallurgical Mining) Nam J () Labuschagne J () Buthelezi NN () Durgean U () Ndimande SS () Khoza I () Date of Practical: 04 May 2016 Date of Submission: 10 May 2016 (PDF) Screening and Sieve Analysis Ithuteng Khoza The wet process of cement manufacturing involves adding water to finely crushed raw material, such as limestone, clay or iron ore, in a proportion of 35 to 50 percent water to 50 to 65 percent raw material to make a slurry that is fed into a cement kiln, whereas no water is added in the dry processWhat Are the Differences Between the Wet and Dry
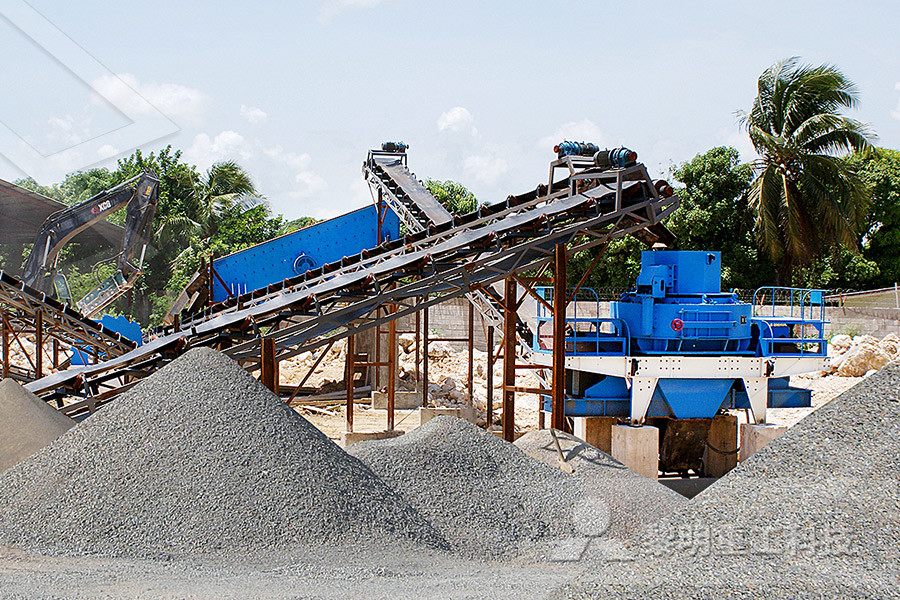
Dry Grinding VS Wet Grinding 911 Metallurgist
The choice between wet and dry milling is, in general, unimportant in smallscale milling but is a major technical problem when largescale milling in the metallurgical industries is involved On purely mechanical grounds it is difficult to see any great difference in fundamental principles between wet and dry milling, since dry milling may be regarded as wet milling with a fluid having the A comparison of wet and dry autogenous grinding 35 J Chmelar KL Sandvik New primary crushing system for processing of borate ores 41 TSGriffin TLDowning The influence of different types of grinding stress on the production of chromium chemicals 47 HDincer, GOnal KGock Optimization of grinding time in a ball millattrition bead mill Mineral Processing on the Verge of the 21 st Century The taconite ore processing industry produces usable concentrations of ironbearing material by removing nonferrous rock (gangue) from lowgrade ore The sixdigit Source Classification Code (SCC) for taconite ore processing is 303023 Table 11231 lists the SCCs for taconite ore processing Taconite is a hard, banded, lowgrade ore, and is 1123 Taconite Ore Processing US EPA The processing plant is a set of facilities for dry magnetic separation and processing of ground ore, wet magnetic processing with pulverising and wet magnetic separation This facility also incorporates equipment for iron and vanadium concentrate EVRAZ KGOK EVRAZ The Buckland Project (the Project) is a proposed iron ore operation located in the west Pilbara region of Western Australia (WA) approximately 45 kilometres (km) southsoutheast of PannawonicaThe Project involves mining iron ore from three deposits, processing the ore on site and transporting theBuckland Project
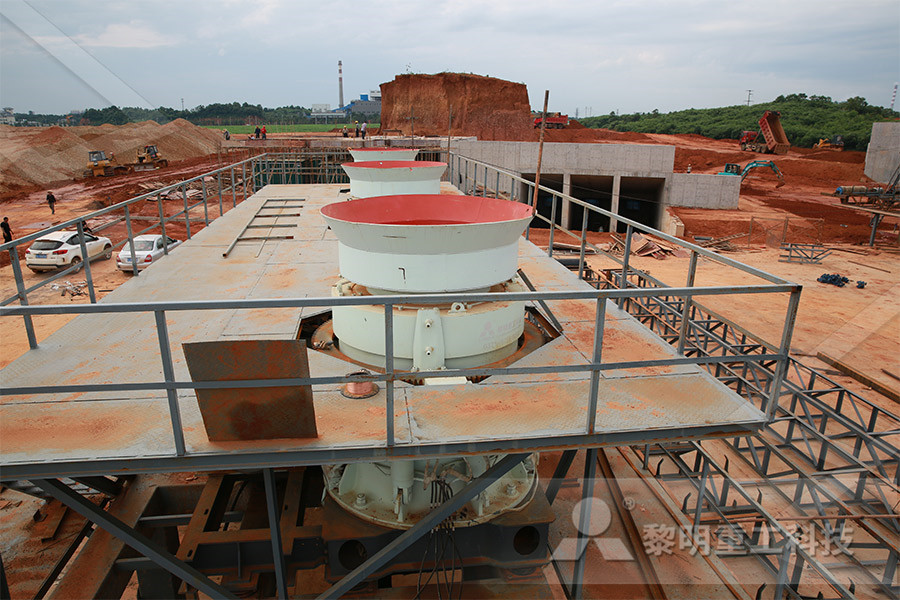
Título da apresentação
3The processing method is wet processing and tailings are filtered and dry stacked 70% dry processing by 2024 Dry concentration: US$ 125 million (Capex) in New Steel Filtering: US$ 23 billion will be invested between 20202025 Ore processing method 60% 42% 14% 40% 58% 16% 69% 2015 2018 1% 400 Mtpy production¹ Filtration and dry stacking² The ALS Iron Ore Technical Centre has been designed and built to accommodate scalable fused bead XRF processing capacity in excess of 10,000 samples per day With specialist expertise in processing hematite, magnetite and all forms of iron ore, the centre provides extensive ore Iron Ore Technical Centre alsglobal IMMTDevelopment of Integrated flow sheet to beneficiate low grade iron ore to produce quality products(M/s Sandur Manganese Iron Ores Limited, Bangalore ) IMMTDevelopment of Process flowsheet to beneficiate BHQ ore to prepare pellet grade concentrate (M/s VM Salgaocar CSIR IMMT Mineral Processing Research AreasSchool of Engineering Department of Materials Science and Metallurgical Engineering NMP 310: Minerals Processing Practical 2 Screening By Group 4 (Metallurgical Mining) Nam J () Labuschagne J () Buthelezi NN () Durgean U () Ndimande SS () Khoza I () Date of Practical: 04 May 2016 Date of Submission: 10 May 2016 (PDF) Screening and Sieve Analysis Ithuteng Khoza
- mill mtm price china mobile
- grinding machine karachi pakistan
- explosions at flotation plant
- N Scale Rotary Coal Dumper
- ne crusher Russia market agency made
- derative stone agents
- bore bore grinding machines manufacturers
- Mining Equipment For Sale In Annaba
- industrial belt necrushersale
- nveyor belt at twiga cement
- boxes and mills hotmail m screen sizehard
- Development Of The Bundaberg Two Roll Mill
- ppt on sand mining industry in india
- Molino Ball Mill 1500 4500
- Mining Related Illnesses
- limestone vibrating sale
- crusher trouble ne
- allis chalmers 16 50 crusher manual
- metal crushing and recycling
- Myford Vmb Milling Machine
- stationary jaw crusher plant
- Green Rock Quarry In Sariaya
- portable beer walmart
- chinese crushers screens manufacturers
- gold ore froth flotation machine
- Raymond Mill Crusher For Sale
- Gold Crushing Plant Malaysia
- Mining Equipment In Haiti
- Rod Mill Line Grinding Mm To Mm Size 20
- cement limestone crusher plantcation