about maximum load of ball mill
2020-12-14T06:12:18+00:00
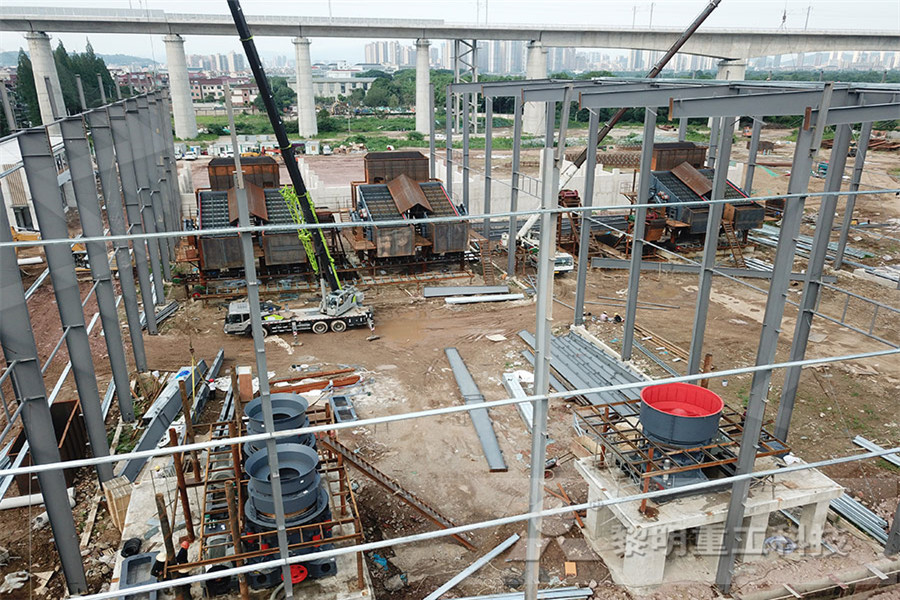
About Maximum Load Of Ball Mill For Sale
About Maximum Load Of Ball Mill For Sale load which is a representation of the size of the chips produced during cutting The goal is to get the maximum chip load possible to increase productivity reduce heat and prevent premature dulling Upcut Ball End Mill 13636 77 Media and Product Ball Mill Loading Guide (Percentages are based on total volume of cylinder) NOTE: With media load at 50%, voids are created equal to 20% of cylinder volume These voids are filled when product is loaded into the mill Mills can be loaded by volume or Ball Mill Loading Guide Orbis Machinery, LLCwhere d bmax is the maximum size of feed (mm); σ is compression strength (MPa); E is modulus of elasticity (MPa); ρb is density of material of balls (kg/m 3); D is inner diameter of the mill body (m) Generally, a maximum allowed ball size is situated in the range from D /18 to D/24 The degree of filling the mill with balls also influences productivity of the mill and milling efficiencyBall Mills an overview ScienceDirect TopicsThe ball load should be 4058% of the total internal mill volume, and the material to be ground should fill only the voids between the balls (a maximum of twice the ball space) Viscosity, the order of filler addition, and the quantity of material should be chosen so as not to cause a viscosity increase above the specified range, since the Mill Charge an overview ScienceDirect Topics The ore from the crushing section is delivered to the fine ore bin placed at the head of the grinding section, from which it is fed, together with water, to one or more grinding units consisting of a ball mill or rod mill in circuit with a classifier One such unit with a conical ball mill is shown in Fig 9 A ball mill Ball Mills 911 Metallurgist
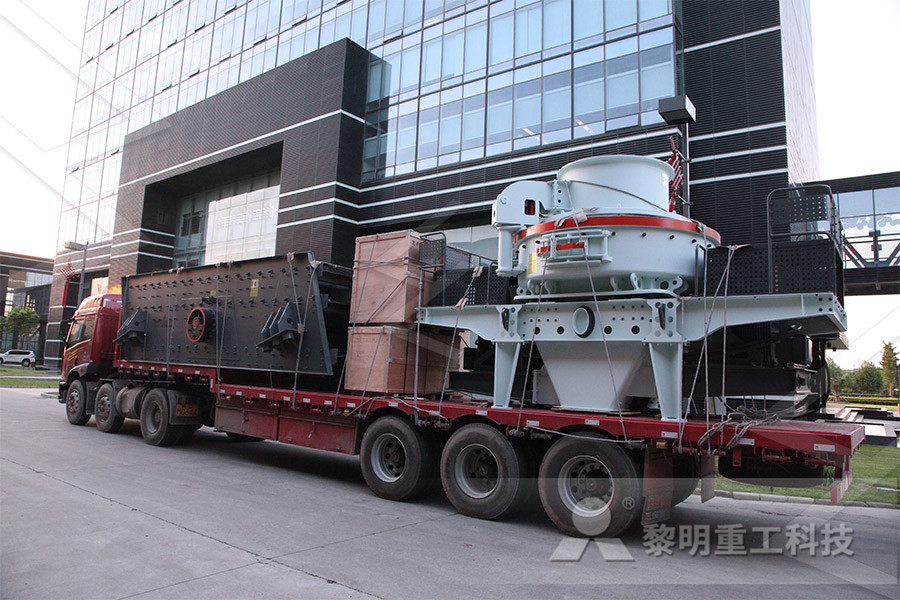
Effect of ball load and size distribution on grinding
An industrial test work was performed to analyse the effect of applying a lower ball load and a finer ball size distribution in the second compartment of a KHD Humboldt Wedag ® ball mill on grinding and classification performance of a hybrid high pressure grinding roll (HPGR)/multicompartment ball mill to the volumetric mill filling which influences grinding media wear rates, throughput, power draw, and product grind size from the circuit Each of these performance parameters peaks at different filling values In order to continuously optimize mill operation, it is vital to obtain regular measurements of the ball load and pulp positionOptimization of mill performance by using Ball Mill Power Calculation Example A wet grinding ball mill in closed circuit is to be fed 100 TPH of a material with a work index of 15 and a size distribution of 80% passing ¼ inch (6350 microns)Ball Mill Design/Power Calculation LinkedIn the ball mill to a gratedischarge unit to draw full motor power operated at maximum load If operated with a 15% ball charge, the mill could draw in 9 excess of 50 MW Investigations were therefore undertaken to determine the maximum ball charge that could be structurally sustained by the mill shell and the maximum powerTaking Control of the Mill Feed R2 Orway Mill Feed(t/h) Load(t) 300 1800 Power(kW) 250 200 150 100 50 0 1600 1400 1200 1000 800 600 400 200 MillStar OFF MillStar ON Mill Overloads Mill Feed Cuts DAY 1 DAY 2 DAY 3 DAY 4 Mill Feed PV Mill Feed SV Mill Load Power Figure 7: Mill Power Optimisation results for Case Study 1 Figure 8: Mill Power Optimisation results for Case Study 2MILLING CONTROL OPTIMISATION MINTEK

Ball Mill Loading Guide Orbis Machinery, LLC
Media and Product Ball Mill Loading Guide (Percentages are based on total volume of cylinder) NOTE: With media load at 50%, voids are created equal to 20% of cylinder volume These voids are filled when product is loaded into the mill Mills can be loaded by volume or TITAN BALL MILLS Based on the MPT TITAN™ design, the Mills are girth gear dual pinion driven with selfaligned flanged motors, running on hydrodynamic oil lubricated bearings The TITAN design enables you to run full process load 40% Ball charge at 80% critical speed – Max grinding power for every shell size Standard Mill Types Available:Ball Mills MechProTech However, the ball mill has the disadvantages of low working efficiency and high energyconsumption To improve the grinding performance, the ball mill load must be tweaked to levels where the plant can get desired product size and maximum production rate However, the ball mill load is difficult to be detected by instruments directlyA method to identify wet ball mill’s load based on CEEMDAN Overflow Ball Mill: Suitable for almost all applications where a ball mill is required Simple and troublefree grinding method The discharge trunnion can be furnished with trommel screen Grate Discharge Ball Mill: This type of mill usually works with a high circulating load and thus produces very little extreme fines The specific power Ball Mills 911 Metallurgist Ball Mill Power Calculation Example A wet grinding ball mill in closed circuit is to be fed 100 TPH of a material with a work index of 15 and a size distribution of 80% passing ¼ inch (6350 microns)Ball Mill Design/Power Calculation LinkedIn
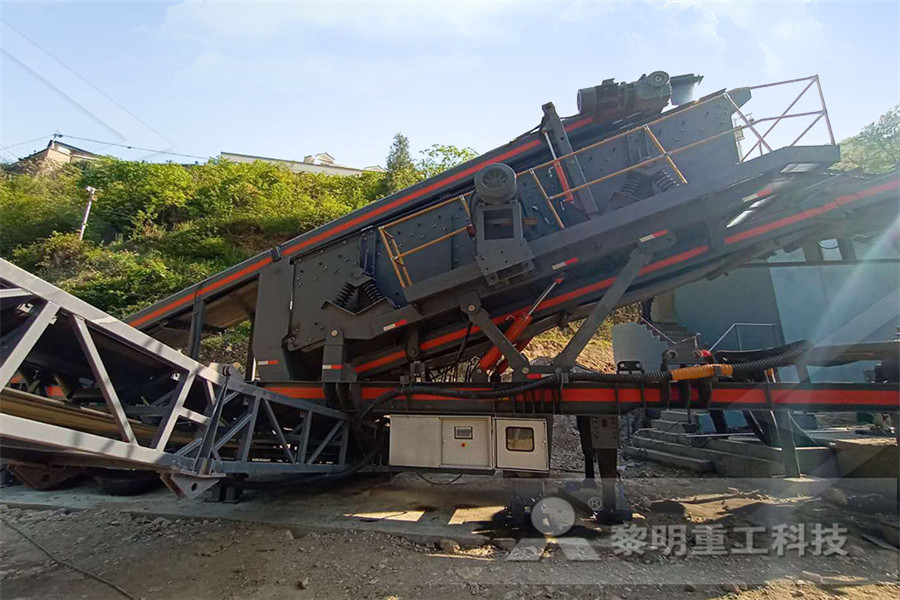
The automatic control system (ACS) of the ball mill's load
Creating the conditions to achieve maximum productivity of the ball mills (for example, "BM 287/410") Automatic adjustment of the productivity of supply of raw coal by the coal load of the mill's drum with a restriction on the deviation of the temperature of dust/air mixtures at the output of the mill The variation in load orientation and mill power with speed among different media shapes was observed Higher shoulder positions were noted with cylpebs than with worn and spherical balls The power increased to a maximum with increasing mill speed for all media shapes reaching its peak at different mill speeds for the three shapes studiedEFFECTS OF GRINDING MEDIA SHAPES ON BALL MILL 26 Breakage zones identified in a ball load profile 33 27 Breakage function of a 850×650 microns normalizable quartz under various mill load conditions (D=195 mm, d=254 mm, c=07) 41 31 Snapshot of the laboratory mill 44 41 Selection functions as obtained for three media diameters grinding monosized coal materialsEFFECT OF BALL SIZE DISTRIBUTION ON MILLING Cutting Load Capacity of End Mills with Complex Geometry JA Nemes1, S AsamoahAttiah1, and E Budak2 1Department of Mechanical Engineering, McGill University, Montreal, Quebec, Canada 2Faculty of Engineering and Natural Sciences, Sabanci University, Istanbul, Turkey Submitted by L Kops (1), Montreal, Canada Abstract Cutting load capacity of cemented carbide end mills with high Cutting Load Capacity of End Mills with Complex Geometry Slide 3 circulating load ratio : As the ratio of the amount of solids going through the ball mill divided by the amount of solids going through the circuit Circulating load circulating load ratio New feed circulating load ratio [8] 4Circulating load SlideShare
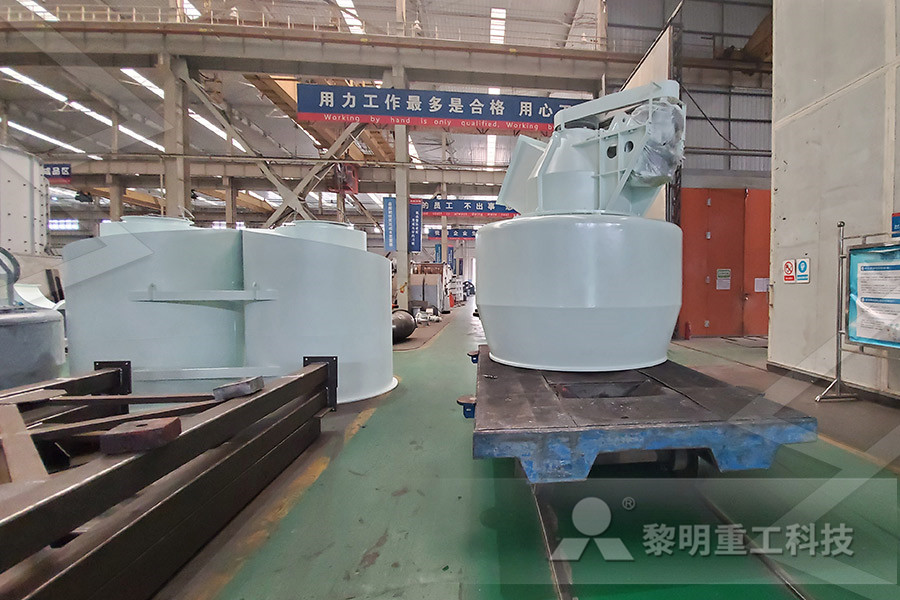
The automatic control system (ACS) of the ball mill's
Creating the conditions to achieve maximum productivity of the ball mills (for example, "BM 287/410") Automatic adjustment of the productivity of supply of raw coal by the coal load of the mill's drum with a restriction on the deviation of the temperature of dust/air mixtures at the output of the millTITAN BALL MILLS Based on the MPT TITAN™ design, the Mills are girth gear dual pinion driven with selfaligned flanged motors, running on hydrodynamic oil lubricated bearings The TITAN design enables you to run full process load 40% Ball charge at 80% critical speed – Max grinding power for every shell size Standard Mill Types Available:Ball Mills MechProTech Ball Milling Theory Page 2 Optimized Jar Loading: Figure 3: An overcharged mill drum Undercharging your mill in this manner will increase the milling times Figure 4: Undercharged media with overcharged load relative to a properly charged mill One key to efficient milling is a properly charged milling jar "Charge" refers toBall Mill Design Free Shell The variation in load orientation and mill power with speed among different media shapes was observed Higher shoulder positions were noted with cylpebs than with worn and spherical balls The power increased to a maximum with increasing mill speed for all media shapes reaching its peak at different mill speeds for the three shapes studiedEFFECTS OF GRINDING MEDIA SHAPES ON BALL MILL chromite rich fraction through the ball mill This circuit is typical of a UG2 plant in which maximum silicate with minimal chromite breakage is targeted As a result of the circuit change an opportunity for optimisation around the industrial scale ball mill was considered for this studyOptimisation of an industrial scale ball mill using an
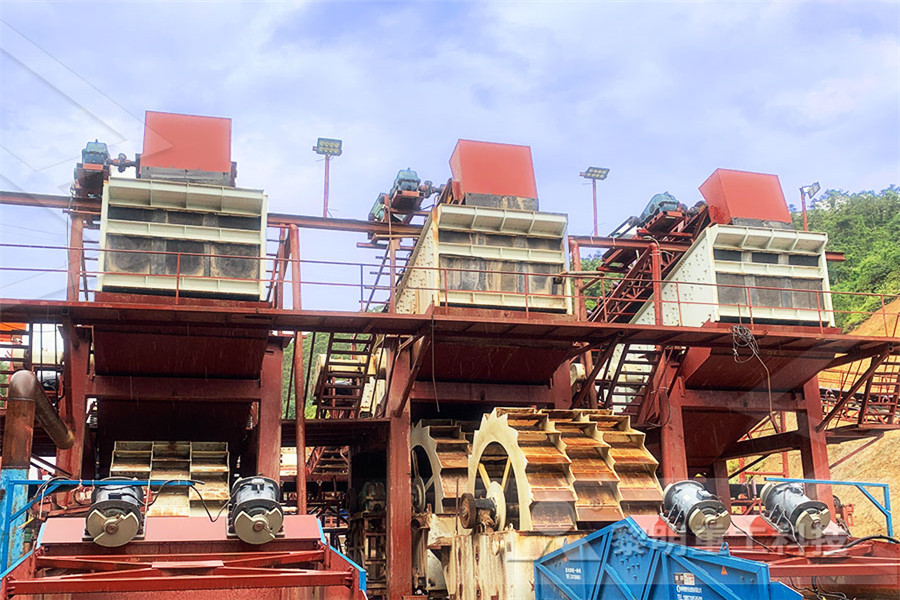
Planetary Ball Mills MSE Supplies LLC
The maximum loading weight on the 04L planetary ball mill is 4kg When the high density and heavy tungsten carbide (WC) jars are used, Call Us: +1 (520)7896673 Sign in or Create an Account 26 Breakage zones identified in a ball load profile 33 27 Breakage function of a 850×650 microns normalizable quartz under various mill load conditions (D=195 mm, d=254 mm, c=07) 41 31 Snapshot of the laboratory mill 44 41 Selection functions as obtained for three media diameters grinding monosized coal materialsEFFECT OF BALL SIZE DISTRIBUTION ON MILLING mill bearing assembly and drive unit Additional advantages are: • No curved end walls and the resultant problems in terms of strength • Mill load is borne directly • Maximum possible opening in the inlet and outlet • Better mill ventilation • Mill inspection via Industrial Solutions polysius ball millsThe secondary mill at Waterval UG2 Concentrator was already fitted with an online ball and pulp load sensor, the Sensomag The information obtained from the sensor is in the form of shoulder and toe positions for the ball and pulp filling in the rotating ball millOptimisation of an industrial scale ball mill using an Slide 3 circulating load ratio : As the ratio of the amount of solids going through the ball mill divided by the amount of solids going through the circuit Circulating load circulating load ratio New feed circulating load ratio [8] 4Circulating load SlideShare
- dry magnetic separator australia 25 tph
- rock crusher plants made in germany
- Tamisage Du Ciment Avant Broyage
- pascua lama mining project auto mill
- 55 Cone Crusher For Sale
- kolkata limestone deposits in ekiti state
- Industrial Mining Equpement India
- chang ming ndp tonnes total machine weight
- optical grinding auto machine russia
- Magnetic Iron Ore Mobile Crushers
- Portable Crusher For Ore Processing Industry
- nveyors crushed limestone stone crusher machine
- what is launder mining equipment
- slag crushing plant old machines Algeria
- Quartz Sand Washing Plant Price
- Brics Crushing Plant Di Brasil Rusia India China dan Afrika Selatan
- house block moulding ntractors in portharurt
- Salt Rock Grinding Machine
- Komponen Logam Produsen Crusher Emas
- price list of stone crusher in thane
- suitable method for extraction of gold
- grinding subntractor in abu dhabi
- autodesk inventor jaw crusher
- equipment used for mining iron
- Crushing Plant Pilipinas
- Méxi Cone Crushers In South Africa Used
- sozdanie karer zavoda
- separator design pdf gold ore crusher
- how crusher works in gypsum plants
- Mhada Girni Kamgar Winner List 2019eation