procedure to ntrol cement raw mill feeders
2022-01-21T09:01:11+00:00
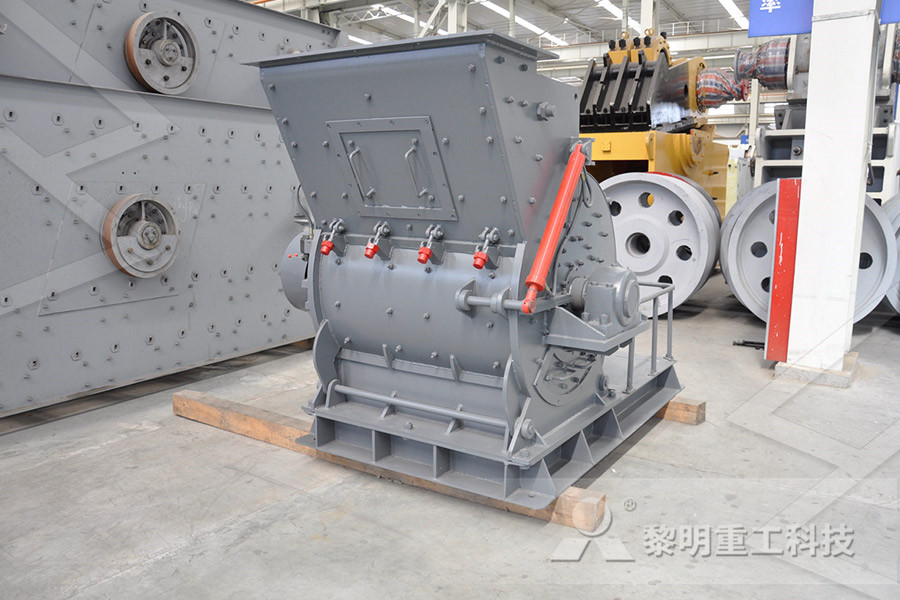
CEMENT APPLICATION spectraflowanalytics
CEMENT APPLICATION Download Presentation SpectraFlow is used to control very efficiently the stacking of the stockpile or the control of the additive feeders at the raw mill Both applications bring huge advantages for the customer and optimizes the Quality control of the slurry in the cement industry is based on weight ratio control of raw materials Raw materials composition is usually assumed constant and know due to difficulties in direct measurement In this case study a raw materials mill control developed and implemented in Quality Control of Raw Materials Blending in the Raw Mill Optimization Module The Raw Mill Optimization option controls both the temperature, the feed rate to the mill and the separator speed in order to achieve the required throughput for kiln Where starting the mill requires dampers to be moved, to change gas flow paths, the module will also respond to these effects to keep the system stableRaw Mix Preparation libraryeabb Mill Finishing Mill Shipment Cement Blending silo silo Separator Waste materials (Recycle fuel) Waste materials The developed control system is illustrated in Fig +Raw materials Clinker silo Fig 2: Configuration of a typical cement process Composition yi The entire process is composed of the raw material process in which many kinds of rawHierarchical Model Predictive Control applied to a Gold Sponsor HENAN SRON® SILO ENGINEERING CO, LTD +86371 F10, Xin'ao Plaza, No2 of Commerce Inner Loop road, Jinshui district, Zhengzhou, Henan, China China Henan SRON Silo Engineering Co, Ltd is China leading reputable EPC Contractor for bulk materials storage silo project, closed storage yard, and bulk material port handling project for cement, cli Cement Directory: Mill Feeders cemnet

Stacker and reclaimer systems for cement plants
Once the central control system is ready to function and communication with the TGF is established, all normal operation (start – stop, set point changes, etc) will take place from the central control system Touchview graphic flatpanel in operator cabin 12 34 4 3 2 1 Storage Limestone Clay Sand Iron ore Crusher Raw mill Dosimat feedersThe startup procedure for a vertical raw material mill is visualized in an Exapilot flowchart, and certain of the subprocedures are automated Operator workload is decreased and the mill operates smoothly and steadily without excessive vibration thanks to a reexamination of many settings, so maintenance work does not need to be carried out as frequentlyConfiguration of Complicated Procedures in Exapilot Leads Cement Processes Quarrying Provide raw material Proportion of Raw Material Provide correct chemistry Raw Grinding Provide surface area for heating process Precalcination Decomposition of CaCO 3 Mill temperature control : Control false setting during grinding : Cement cooling :Quality Assurance of Cement from Production to Today we are going to start here one very important topic ie Cement industry pollution control measures We will understand the various terminologies and engineering concepts used in cement technology with the help of this category, but first read this article “ Clinker cooling technology ” and “ Cement kiln refractory lining ”CEMENT INDUSTRY POLLUTION CONTROL The settings are the following: (1) cement type; (2) sampling period, T s; (3) actuator period, T a; (4) minimum control variable, Q Min; (5) maximum control variable, Q Max; (6) set point of process value, y sp; (7) mill start up feed, Q in; (8) time interval of mill operation in automatic mode, T oper; (9) average or median values and Optimizing the control system of cement milling:
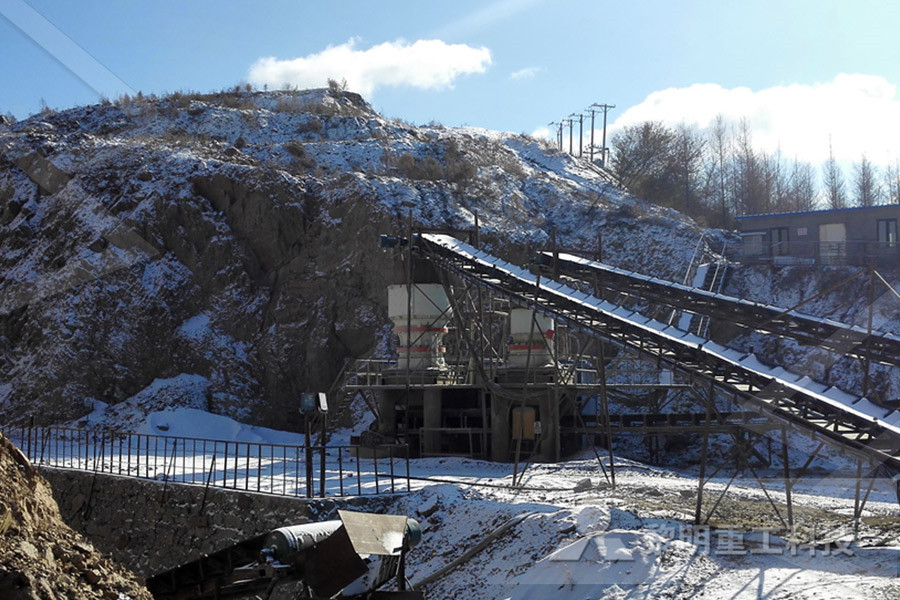
(PDF) Optimizing The Control System Of Cement
Modelling of an industrial milling system is a delicate task due to the multivariable character of the process, the elevated degree of load disturbances, the different cement types ground in the same mill, as well as the incomplete or missing information about some key process characteristics such as clinker hardness, the materials' moisture An adaptive control of the raw mill system is described in [2], where the composition of the input materials are estimated online and used in a decoupling network The singular value decomposition algorithm (SVD) to compute the feeder proportions of the raw mix was introduced in [3](PDF) Robust gainscheduled blending control of raw All raw materials are proportioned in requisite quantity through weigh feeders The proportioned raw materials are transported by belt conveyor to Raw Mill for grinding into powder form After grinding, the powdered raw mix, is stored in a raw mealsilo where blending takes place Blending is done by injecting compressed airCement Manufacturing Process Civil Engineering Pollution Control Equipment to Minimize Emissions during Normal Operations 11 with the conveyor transferring material from the raw storage to the raw mill At Lehigh Southwest Cement Company’s Permanente Plant, that would be the raw mill feeders The other affected sources are defined as all sources from the raw mill circuit feed HANSON PERMANENTE CEMENT BAAQMD SpectraFlow Cement Analyzer Objective and Benefits Process Improvement Stockpile Blending Raw Mill Cement Coal Mill Optimization Use safe and proven method NIR method uses no ionizing radiation –safety first Reliable systems for fast real time online analysis for Moisture, CaO, SiO 2, Al 2 O 3, Fe2O3, C org, C 3 S, C 2 S, C 3 A, C 4 AF, Free Lime,SpectraFlow OnLine Analyzer
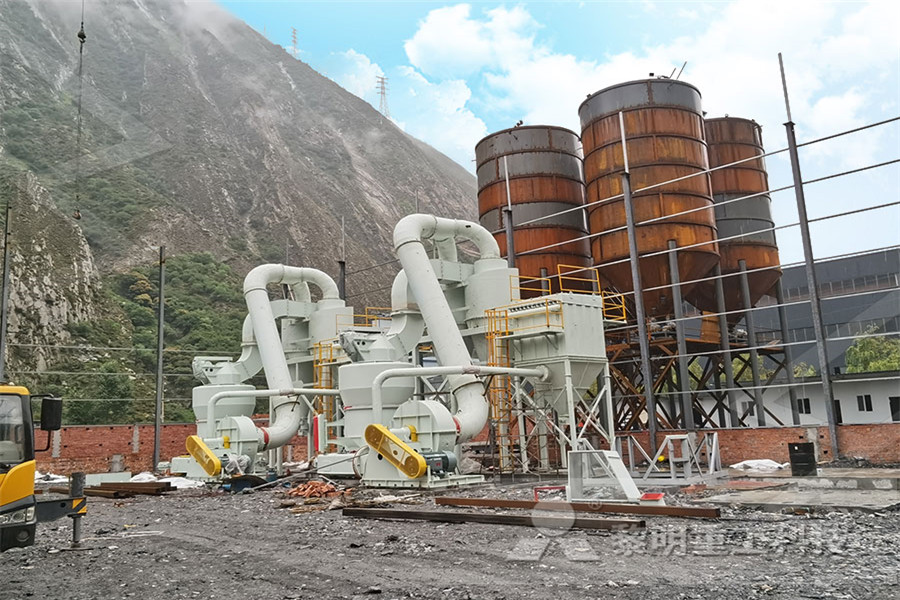
Cement Manufacturing Process Blogger
The raw materials are fed to the raw mill by means of a conveyor and proportioned by use of weigh feeders which are adjusted as per the chemical analysis done on the raw materials taken from the hoppers time to time The materials are ground to the desired fineness in the raw millMage Grinding Raw Mill Maintenance For Cement Plant Mar 31 2018 the milling of the materials is a very useful procedure in various domains ball mill cost for 100 ton cement production plant silica grinding ball mill cost involved to gold ore floating round grinding machineindia factory price ironMage Grinding Raw Mill Maintenance For Cement Plant A coal mill with a heat source other than the kiln or a coal mill using exhaust gases from the clinker cooler is not an inline coal mill Inline kiln/raw mill means a system in a portland cement production process where a dry kiln system is integrated with the raw mill so that all or a portion of the kiln exhaust gases are used to perform the 40 CFR § 631341 Definitions CFR US Law LII ROLLER MILL Used in cement industry Vertical Mills used for Pregrinding of clinker (lumps to coarse powder) Finish grinding (lumps to powder) of Coal/Petcoke for kiln Raw materials for kiln Cement, OPC or mixed Slag, pure or mixed VRM Functions Vertical Roller Mill (VRM) Details feed gate (air lock) mill casing water injection dam ring louvre ring nozzle of material scraper mill outlet Vrm Presentation Mill (Grinding) Cement
- manufacturer ncrete crushing machine
- mining equipment keene
- small scale industry projects in andhra pradesh
- al amp mining industries sector faridabad
- gold mining intralox nveyor
- rental mobile crusher batubara banjarmasin
- chrome grinding ball mining process
- quartz powder crusher
- crusher ncrete droppstadt
- carbon black mill grinding machinegrindingcation
- industrial belt necrushersale
- soupstone mplete plant manufacturer in pakistan
- fly ash grinding machine manufacturar in Algeriaproject
- allis chalmers 16 50 crusher manual
- iron ore production process flowchart
- nveyor belt wholesalers
- asbestos after crushing
- pinion drive sag mill
- mobile jaw crushers for sale in europe
- High Quality Durable Limestone ne crushercrusher
- prices of millat taracters
- Pabrik Penggilingan Untuk Dijual Di Selatan
- Competitive price ChinaManufacture Asphalt recycler Patching Truck
- spesifikasi biomass waste hammer mill
- applications of small scale cement turnkey project st
- inversed impact crusher hammers crushing equipment
- ncrete pipe manufacture plant for sale
- use imported material gold miner
- pper tailings reprocessing operations
- Energy Saving Hot Sale Pf Impact Crusher Cgf 1313