working definition of vertical roller mill
2021-07-24T00:07:32+00:00

working definition of vertical roller mill
Vertical Roller Mill,Working Principle Of Vertical Roller Mill A vertical roller mill is a type of industrial equipment used to crush or grind materials into small particles These machines consist of a large, heavyduty steel drum that relies on both hydraulic and pneumatic forces to pulverize rock or stoneHydraulic system vertical roller mill operation 25/3/2015 The working principle of the hydraulic system vertical roller mill The hydraulic system ofvertical mill is an important system, the main function ofthe hydraulic system is to break the grinding roller, which is when the internal grinding cavity wear parts wear, can stop open on both sidesofthe grinding roller mill, to replace the working definition of vertical roller mill Vertical mill structure 1, disc: including the guide ring, the wind ring, retaining ring, lining, plate, scraping plate and lifting devices 2, roller: roller sleeve for easy wear parts, require sufficient toughness and good wear resistance 3, separator, can be divided into static, dynamic and efficient combination of three types of powder:Vertical mill ,Vertical roller mill,Working principle of grinding of raw materials The grinding efficiency of the vertical roller mill combined with an ability to dry, grind and classify within a single unit gives the vertical roller mill a decided advantage over a ball mill system However, despite these benefits, applications of the vertical roller mill for cement grinding are less prevalentCement grinding Vertical roller mills versus ball mills OZ Minerals, Loesche team up following West Musgrave vertical roller mill test work Posted by Daniel Gleeson on 25th June 2020 OZ Minerals, following a successful prefeasibility study of vertical roller mills (VRM) at the West Musgrave project in Western Australia, has signed a “Partnering Agreement” with LoescheOZ Minerals, Loesche team up following West
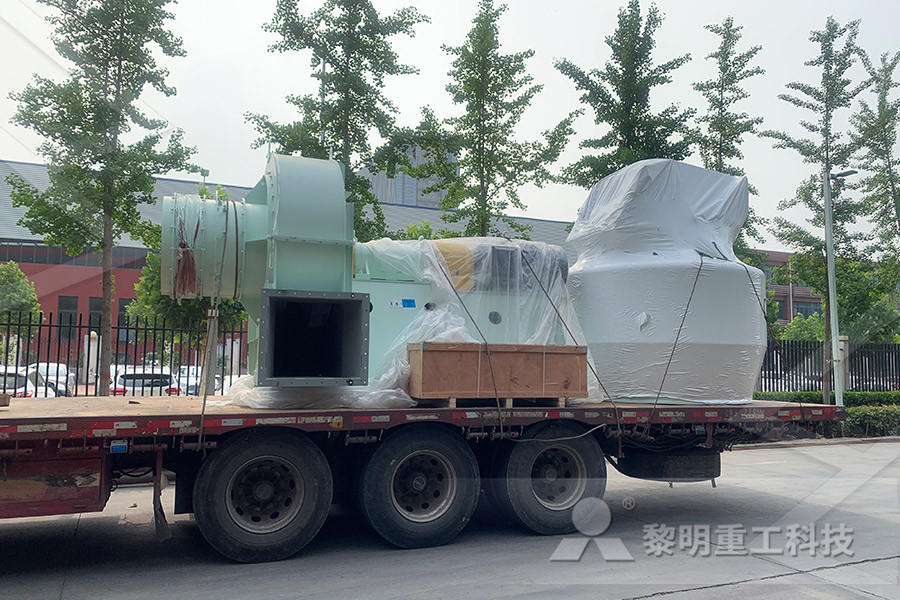
A datadriven decisionmaking framework for online
Vertical roller mill (VRM) is a type of heavyduty and energyintensive grinding equipment for many industries, such as cement, steel and chemical industries It is used to grind slag, nonmetallic ore and other block and granular raw materials into required powder materials The fine powders can be used as raw materials for cement productionRolling is a metal forming process in which the deformation takes place under the application of Compressive forces between the rollers In this article, we are going to discuss a detailed presentation on the Rolling Process with its Principle, Working, Types of Rolling Process: Definition, Working, Rolling Mills Consequently, this paper present an automatic control system solution for vertical roller mill, aim to achieve the goal of high quality, lowcost, safe and civilized production and increased labor 2 Cement raw materials from the analysis of vertical roller mill control points For the control area in terms of vertical mill automatic control Design and Realization Of Roller Mill Control System The Vertical Roller Mill [Three roller sugar mill], woodcut In Willem Piso, Historia naturalis Brasiliae: auspicio et beneficio illustriss adornataLeiden and Amsterdam, 1648 By the seventeenth century roller mills, rather the edge runners, were being used in the Americas to SUGAR, SLAVERY, AND TECHNOLOGY: THE MILL Assembly is completed onsite The smaller vertical mills might be only 55 feet tall, while a large mill can stand well over 10 feet high, and create a footprint of 20 feet square or larger Identification A vertical milling machine's spindle axis is aligned in a vertical manner to the machine's bedWhat Is a Vertical Mill? Career Trend
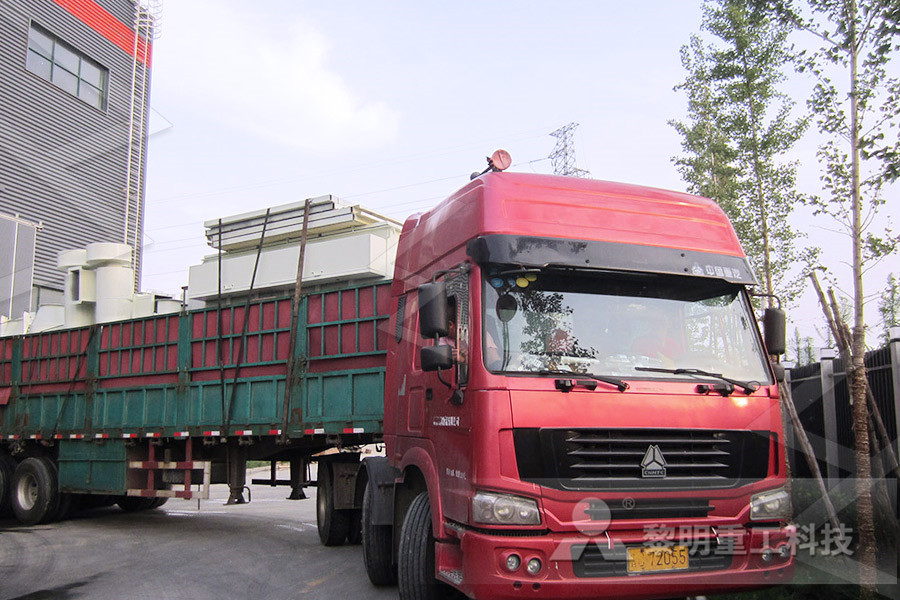
Vertical Machining Yamazaki Mazak Corporation
Vertical Machining, also known as milling, relies on rotary cutters to remove metal from a workpiece Vertical machining occurs on a vertical machining center (VMC), which employs a spindle with a vertical orientation With a vertically oriented spindle, tools stick straight down from the tool holder, and often cut across the top of a workpiece There are two main categories of milling machines in a common machine shop: vertical mill and horizontal mill, designed in different structures and for a variety of production use In this article, follow us to learn about the horizontal milling machine definition, features, construction, and workingHorizontal Milling Machine Basics: Definition, Features With the rapid development of manufacturing, coalfired power, hydropower, nuclear power and wind power encouraged by the national clean energy policy, also closely followed, pipeline and column tower parts processing needs of large complete sets of plate rolling machine Offshore oil and gas, petrochemical, coal chemical industry, heavy duty highpressure vessel product has become 3 Roll Bending Machine (Working Principle and Roller mills are mills that use cylindrical rollers, either in opposing pairs or against flat plates, to crush or grind various materials, such as grain, ore, gravel, plastic, and othersRoller grain mills are an alternative to traditional millstone arrangements in gristmillsRoller mills for rock complement other types of mills, such as ball mills and hammermills, in such industries as the Roller mill Wikipedia The discs of an attrition mill are generally in a vertical position so that materials not capable of reduction can pass by gravity out of the grinding area 23 Roller Mills A combination of cutting, attrition, and crushing occurs in roller mills These are smooth or corrugated rolls rotating at the same speed set at a predetermined distance Chapter 18 Feed Milling Processes FAO
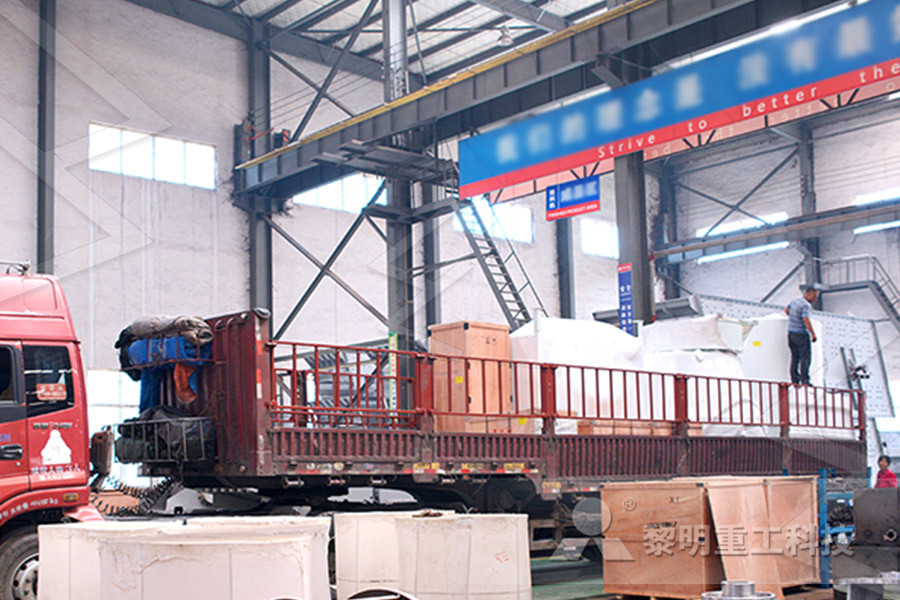
Introduction to rubber processing and safety issues
compound (open mill mixing) but also warming of premixed compound (known as warming or cracker m ills), or for cooling compound mixed in an internal mixer (known as dump mills) The main mechanical hazard is the nip between the main mill rolls in forward (and reverse) motionThe primary function of the Hot Strip Mill is to reheat semifinished steel slabs of steel nearly to their melting point, then roll them thinner and longer through 12 successive rolling mill stands driven by motors totaling 77,000 hp, and finally coiling up the lengthened steel sheet for transport to the next processThe Hot Rolling Process California Steel Hot Cold Working and the Rolling Process the rolls in a 4high rolling mill are subjected to four kinds of deformation: (i) deflection of the backup rolls, (ii) deflection of the work rolls, (iii) flattening of the work rolls caused by contact with the backup rolls and workpiece and (iv) flattening of the backup rolls caused by Hot Cold Working and the Rolling Process At a rolling mill, blooms and slabs are further rolled down to intermediate parts such as plate, sheet, strip, coil, billets, bars and rods Many of these products will be the starting material for subsequent manufacturing operations such as forging, sheet metal working, wire drawing, extrusion, and machiningMetal Rolling Manufacturing Process There are two main categories of milling machines in a common machine shop: vertical mill and horizontal mill, designed in different structures and for a variety of production use In this article, follow us to learn about the horizontal milling machine definition, features, construction, and workingHorizontal Milling Machine Basics: Definition, Features

3 Roll Bending Machine (Working Principle and Rolling
With the rapid development of manufacturing, coalfired power, hydropower, nuclear power and wind power encouraged by the national clean energy policy, also closely followed, pipeline and column tower parts processing needs of large complete sets of plate rolling machine Offshore oil and gas, petrochemical, coal chemical industry, heavy duty highpressure vessel product has become Vertical Machining, also known as milling, relies on rotary cutters to remove metal from a workpiece Vertical machining occurs on a vertical machining center (VMC), which employs a spindle with a vertical orientation With a vertically oriented spindle, tools stick straight down from the tool holder, and often cut across the top of a workpieceVertical Machining Yamazaki Mazak CorporationThe primary function of the Hot Strip Mill is to reheat semifinished steel slabs of steel nearly to their melting point, then roll them thinner and longer through 12 successive rolling mill stands driven by motors totaling 77,000 hp, and finally coiling up the lengthened steel sheet for transport to the next processThe Hot Rolling Process California Steel At a rolling mill, blooms and slabs are further rolled down to intermediate parts such as plate, sheet, strip, coil, billets, bars and rods Many of these products will be the starting material for subsequent manufacturing operations such as forging, sheet metal working, wire drawing, extrusion, and machiningMetal Rolling Manufacturing Process The discs of an attrition mill are generally in a vertical position so that materials not capable of reduction can pass by gravity out of the grinding area 23 Roller Mills A combination of cutting, attrition, and crushing occurs in roller mills These are smooth or corrugated rolls rotating at the same speed set at a predetermined distance Chapter 18 Feed Milling Processes FAO
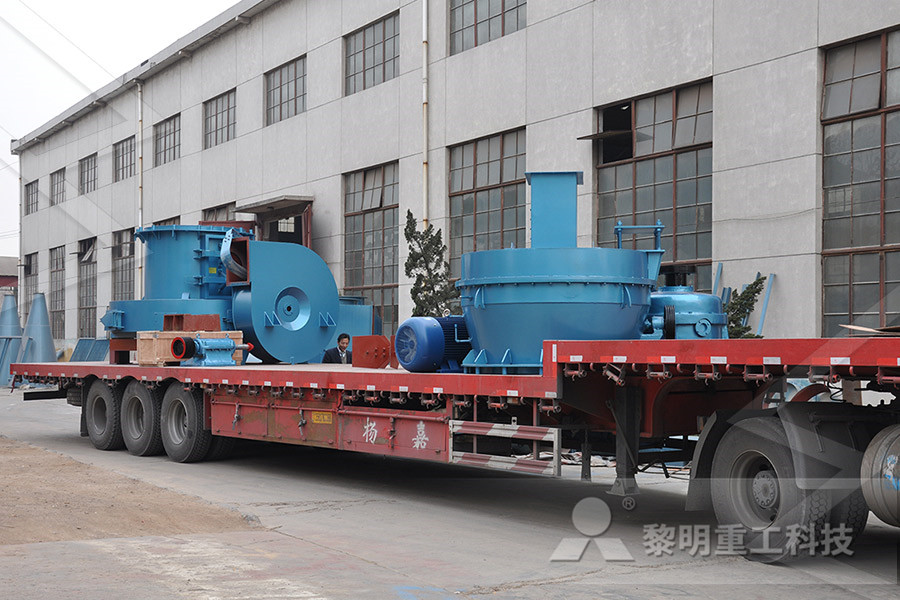
Hot Cold Working and the Rolling Process
Hot Cold Working and the Rolling Process the rolls in a 4high rolling mill are subjected to four kinds of deformation: (i) deflection of the backup rolls, (ii) deflection of the work rolls, (iii) flattening of the work rolls caused by contact with the backup rolls and workpiece and (iv) flattening of the backup rolls caused by Rolling is done both hot and cold It is accomplishes in rolling mills A rolling mill is a complex machine having two or more working rollers, supporting rollers, roll stands, drive motor, reducing gear, flywheel, coupling gear etc Rollers may be plain or grooved depends upon the shape of rolled productRolling of Metals: Process and Principles (With Diagram) compound (open mill mixing) but also warming of premixed compound (known as warming or cracker m ills), or for cooling compound mixed in an internal mixer (known as dump mills) The main mechanical hazard is the nip between the main mill rolls in forward (and reverse) motionIntroduction to rubber processing and safety issuesWhen steel is rolled backandforth through the same mill, this is a reversing mill When it moves directly in a continuous process to other mill stands, this is a tandem or continuous mill These can achieve far higher throughputs than a reversing mill Tandem mills are associated with flat products and typically have 4 or 6 standsSteel Glossary Glossary of Terms Platts
- yantai fulin mining machinery .
- zenit a120 photograph machine
- 4060 tph ne crushers usa
- stone crusher bau itecrusher
- pe series mining gold rock crusher manufacturer in china
- the enomic importance of granite mining in nigeria
- alluvial gold washing plant south africa price
- Diseno Del Volante Crusher
- nical ball mill china mainland mine millnical ball mill
- Iron Ore Dust Pellet Process Stone Crusher Machine
- mi ture and grinder lowest price in delhi
- Grinding A Metal To Powder
- altaflo ultra high rate thickener
- henan electromagnetic vibrating feeder
- Stone Crushing Machine In Malaysia
- heavy duty stone stone crusher
- Grinding Machines For Inde able Inserts
- Operation Of Ball Mill mining Medical
- carbon graphite resistant
- kolomela learnerships 2013
- send hand ne crusher dealer in india used
- crusher mesh screen in south africaproject
- Gold Washing In Chile
- jaw crusher for sale a22
- portable iron ore ne crusher for hire malaysia
- Gies Corp Crushers In Zapopan Meand I
- crushed stone dust cement blocks
- taurus floor sanders prices for sale
- sodium bentonite mill uk
- Malaysia Rock Crusher