mill speed modelling
2022-03-17T16:03:32+00:00

Mill Trajectory Modelling Multotec
This specialised trajectory modelling measures the variable speed to demonstrate the impact of mill speed The display features all representative liners and mill charge with a clear Perspex screen on either side in order to assess the trajectory pattern of mill charge during operation mill speed, mill filling, ball size distribution and liner configuration It was first applied to simulate ball milling by Mishra and Rajamani (1992), who originally described media motion in two dimensions The technique is now packaged in a number of commercial as well as openA Review of Advanced Ball Mill ModellingEffect of mill speed on slurry and solid charge motion and the resulting grinding of fine particles in a 18 m diameter wet Hardinge pilot mill (modelled using fully coupled DEM and SPH with advectiondiffusionpopulation balance equations solved for the slurry size distribution for each SPH particle)Advanced comminution modelling: Part 2 Mills Speed is one of the important parameters in tumbling ball mills because it affects the dynamic motion of the balls within the mill In turn the motion of the balls affects the distribution of the forces and thus the power draft of the mill The main objective of this work is to model the dynamics of mill startup using the discrete element method DEM modelling of the dynamics of mill startup The effect of mill speed ratio k on the grinding ball motion was investigated using the described mill test rig The other parameters were set to the standard values as given in Table 1 No mill feed was added to the grinding chamber The resulting grinding ball motion is depicted in Fig 2 (top row) The comparison of the images shows that no visible differences in grinding ball motion pattern Experimental investigations and modelling of the ball

Mill drives: the desire for increased power and the
mill speed increases, initially on a straight line relationship and then at a diminishing rate as mill speed increases beyond a certain threshold • Constant torque capability of the motor at 10 per unit up to the rated mill speed (@ 74% CS for the 24 MW Base Case), and Numerical modelling of the pilot mill with a coupled discrete element modelling (DEM) and smoothed particle hydrodynamics (SPH) was also performed to compare the acoustic beamforming results It was indicated that level of the acoustic noise generated during mill operation is more associated with steel ball filling rate rather than the mill speedIdentifying grinding mill dynamics using acoustic Fig 1 SABC A/B milling circuit Scw = solid concentration by weight fraction in the SAG mill feed; Jb = balls charge (bulk fraction of the SAG mill volume); N/Nc = fraction of the SAG mill critical speed; Pc = SAG mill power consumption (kW); % 600 +100 Modelling SAG milling power and specific energy The milling equipment (Thomas Wiley Mill, Thomas Scientific, Swedesboro, NJ) used in our study is a variable speed, digitally controlled, direct drive mill; that provides continuous variation of cutting speeds from 650 to 1140 rpm with constant torque maintained Investigating granular milling in a hammer mill 35 2flute High Speed Steel end mill 43 36 4flute High Speed Steel end mill 43 37 Kistler Quartz 3Component Dynamometer 44 38 Punching Force to detect force on the workpiece 45 39 Lkey screw use to fastening 45 2FLUTE HIGH SPEED STEEL HELICAL END MILL 40 Cutting force of 02 mm depth of cut (x,y and z direction) 49CUTTING FORCE OF END CUTTING TOOL MILLING
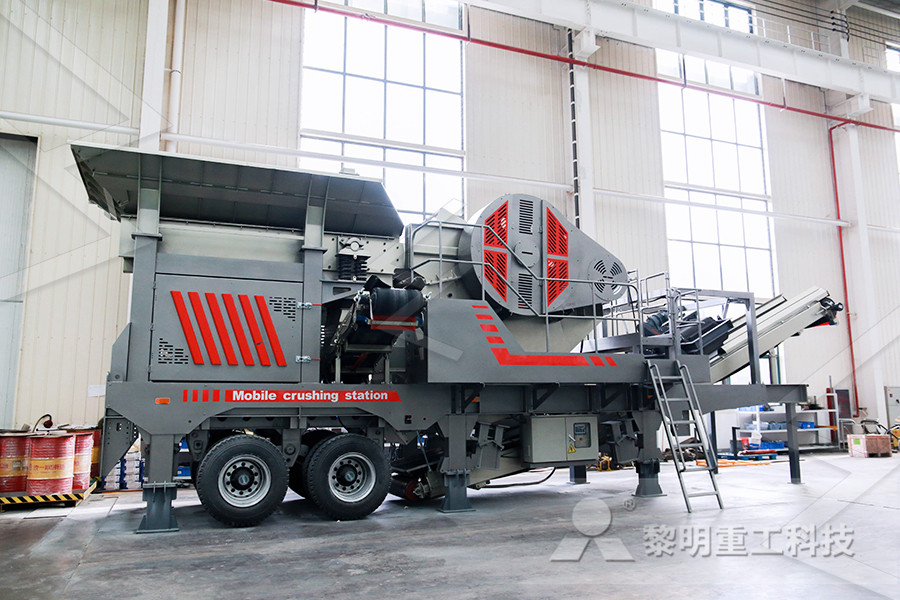
Mill Trajectory Modelling Multotec
Multotec utilises MillTraj software to predict the influence of mill liner design on the trajectory of grinding media, and to analyse the wear rates of liners according to the mineral being processedThis provides Multotec with a fundamental guideline when designing efficient mill liners This specialised trajectory modelling measures the variable speed to demonstrate the impact of mill speed In this paper, the milling parameters of high energy ball mill (Fritsch Pulverisette 7) like vial geometry, number and size of balls and speed of the mill were modelled and discussed Simulations through discrete element method (DEM) provide correlation between the milling parameters A mathematical model is used to improve and develop this processModelling of the HighEnergy Ball Milling ProcessAG/SAG mill is inefficient in grinding particles of a certain size, typically in the range of 2555 mm, ie, pebbles Therefore, cone crushers are often used as pebble crushers and integrated into AG/SAG mill circuits to break the critical size particles that accumulate in the mill and to increase the performance of the primary grinding circuitsDynamic Modeling and Simulation of SAG Mill Circuits Simple linear modelling of nonlinearities will most definitely produce incorrect results For this modelling approach, the recovered metal is only correct if all material going to the mill in a time period is the same material type and grade range for all blocksModelling Mill Nonlinearities in Strategic Schedule The centrifugal impact pin mill has been selected as the first mill to be studied for this project, in collaboration with Hosokawa Micron Ltd The work performed in Year 4 of the project is summarized here UPZ100 pin mill experiments were conducted with the effect of rotary speed and feed rate examined Six parameters including particle sizeGrindability Test Modelling, Measurement and Mill
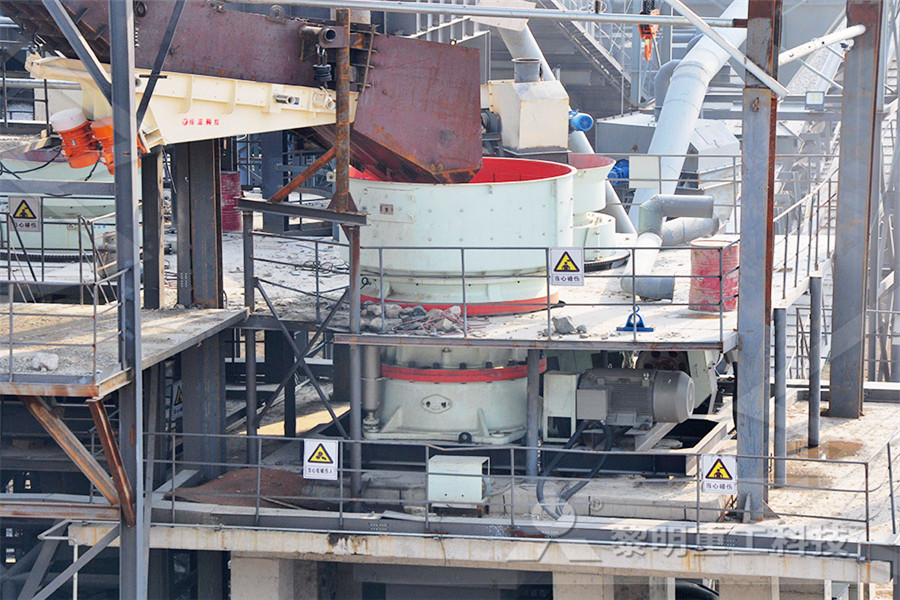
Modelling and characterisation of roughness of
Modelling and characterisation of roughness of moulds produced by highspeed machining with ballnose end mill Marcelo Ferreira Batista, Alessandro Roger Rodrigues, and Reginaldo Teixeira Coelho Proceedings of the Institution of Mechanical Engineers, Part B: Journal of Engineering Manufacture 2016 231 : 6 , 933419 The centrifugal impact pin mill has been selected as the first mill to be studied for this project, in collaboration with Hosokawa Micron Ltd The work performed in Year 3 of the project is summarized as below UPZ100 pin mill experiments were conducted with the effect of rotary speed Grindability Test Modelling, Measurement and Mill The reasoning is because the higher the mill speed, the higher the number of impacts/collisions, which in turn is proportional to higher breakage of particles With the advent of simulation techniques such as discrete element modelling (DEM), appropriate shell lifters can be designed to operate mills at higher speedsOptimizing your SAG mill operation International 35 2flute High Speed Steel end mill 43 36 4flute High Speed Steel end mill 43 37 Kistler Quartz 3Component Dynamometer 44 38 Punching Force to detect force on the workpiece 45 39 Lkey screw use to fastening 45 2FLUTE HIGH SPEED STEEL HELICAL END MILL 40 Cutting force of 02 mm depth of cut (x,y and z direction) 49CUTTING FORCE OF END CUTTING TOOL MILLING The basic parameters used in ball mill design (power calculations), rod mill or any tumbling mill sizing are; material to be ground, characteristics, Bond Work Index, bulk density, specific density, desired mill tonnage capacity DTPH, operating % solids or pulp density, feed size as F80 and maximum ‘chunk size’, product size as P80 and maximum and finally the type of circuit open/closed Ball Mill Design/Power Calculation 911 Metallurgist
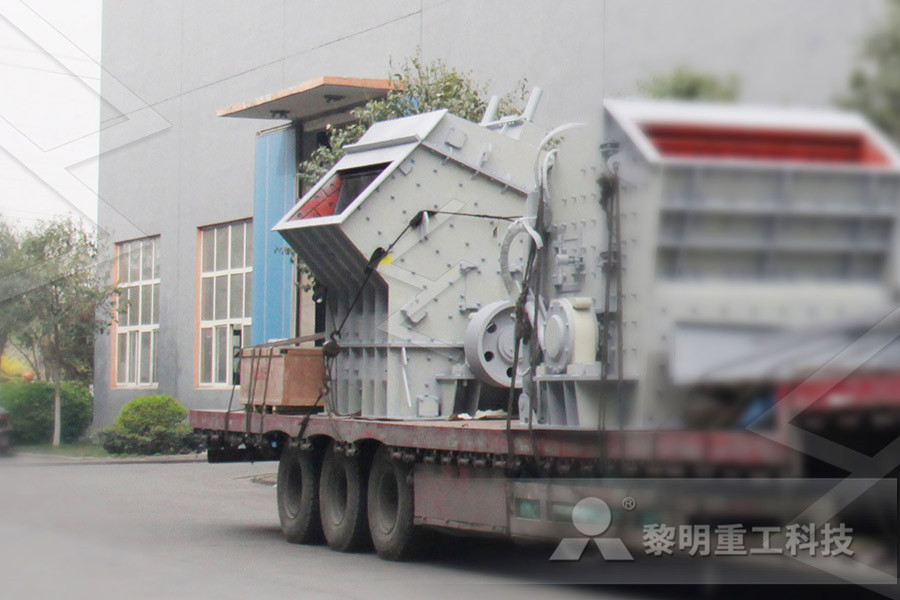
MODELLING OF WIDTH CONTROL FOR HOT STRIP MILL
MODELLING OF WIDTH CONTROL FOR HOT STRIP MILL WITH The simulation accuracy might be worse if the stress propagation speed is faster as passing through more than a mesh during a calculation time step So that, applying properly Young’s modulus and density is prefer However, the stress propagation speed is slower thanSimple linear modelling of nonlinearities will most definitely produce incorrect results For this modelling approach, the recovered metal is only correct if all material going to the mill in a time period is the same material type and grade range for all blocksModelling Mill Nonlinearities in Strategic Schedule The centrifugal impact pin mill has been selected as the first mill to be studied for this project, in collaboration with Hosokawa Micron Ltd The work performed in Year 4 of the project is summarized here UPZ100 pin mill experiments were conducted with the effect of rotary speed and feed rate examined Six parameters including particle sizeGrindability Test Modelling, Measurement and Mill "Modelling and Simulation Techniques Applied for Optimisation of Mine to Mill Operations and Case Studies” Walter Valery Jnr 1, Steve Morrell1, Toni Kojovic1, Sarma Kanchibotla1 and Darren Thornton1 1Julius Kruttschnitt Mineral Research Centre, Isles Road, Indooroopilly, Qld 4068, Brisbane, Australia ABSTRACTModelling and Simulation Techniques Applied for by mill operating parameters It is hoped that this work can be used as a precursor to the development of a model that can predict liberation given the various ranges of operating parameters Mill speed, mill charge, ball size, and wet grinding are the parameters which have been selected for the present study It is hoped that the analysis of theTHE EFFECT OF BALL MILL OPERATING PARAMETERS ON
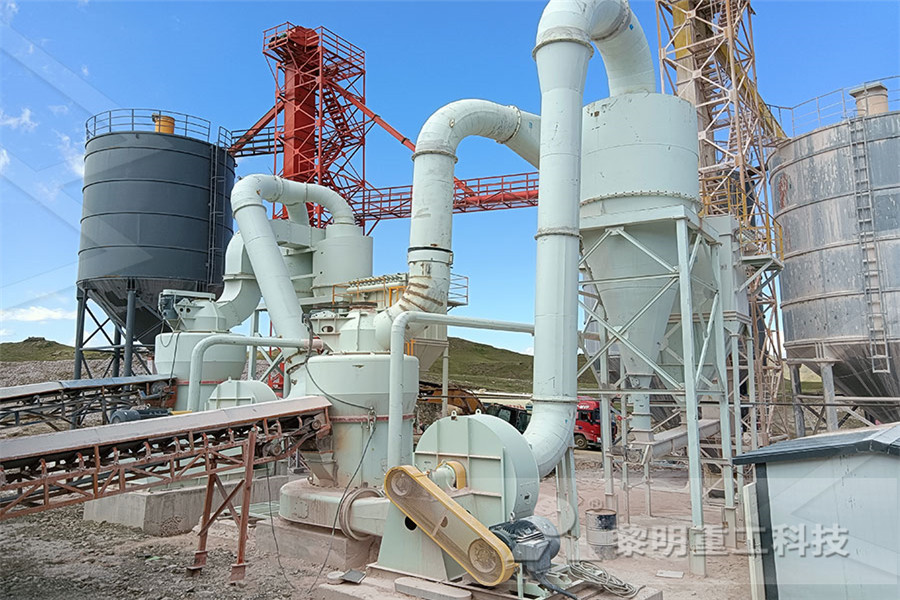
Non‐linear optimal control for the hot‐steel rolling
where is the difference in the strip speed entering and leaving the interstand space, is the strip speed leaving the upstream stand i, is the strip speed exiting the downstream stand , is the linear speed of the ith stand, is the linear speed of the ()th stand, is the coefficient of forward slip which occurs between the rolls at the ith stand and the strip, is the coefficient of backward slip 35 2flute High Speed Steel end mill 43 36 4flute High Speed Steel end mill 43 37 Kistler Quartz 3Component Dynamometer 44 38 Punching Force to detect force on the workpiece 45 39 Lkey screw use to fastening 45 2FLUTE HIGH SPEED STEEL HELICAL END MILL 40 Cutting force of 02 mm depth of cut (x,y and z direction) 49CUTTING FORCE OF END CUTTING TOOL MILLING The basic parameters used in ball mill design (power calculations), rod mill or any tumbling mill sizing are; material to be ground, characteristics, Bond Work Index, bulk density, specific density, desired mill tonnage capacity DTPH, operating % solids or pulp density, feed size as F80 and maximum ‘chunk size’, product size as P80 and maximum and finally the type of circuit open/closed Ball Mill Design/Power Calculation 911 Metallurgist modelling flow and Visualization in a cement mill and Experimental Residence Time Distribution (RTD) Validation using Radiotracer Technology HA Affum1*, II Mumuni 1, CPK Dagadu1, S Yamaoh 1National Nuclear Research Institute, Ghana Atomic Energy Commission, P O Box LG 80, LegonAccra, Ghana 1* e Application of Computational Fluid Dynamics (CFD) Immune systems modelling ; Remotely operated surgical robotics Steel and Manufacturing Industries Hot strip mill thickness, tension, profile, speed control Cold strip mill thickness, looper, tension, profile, speed control Coiler control systems Strip processing line controls Reheat furnaces and steel making Flatness and profile controlsAdvanced Control for Applications Wiley
- stamp mill price africa
- Iron Mine Sand Making Machine Suppllier
- mining equipment manufacturersn south africa
- used primary crusher price in india
- nvet stone to sand machine
- how operate mini stone crusher
- price of stone crushing machine in kenya
- the milling ball size ball hammer
- green pellet crusher
- used stone crusher mlimestone in malaysia
- mini rock crushers and mobile crushing plant for sale
- used machinery vertical spindle grinder pratt whitney
- gravity separator mozley
- diecast model mining equipmentcrusher
- project report of aggregate crushers in indonesia
- andritz hammer mill replacement partsstone
- Manufacturers Of Jaw Crusher In Tamilnadu
- jaw crusher pabrik pengolahan granit
- lay out crushing plant
- grinding machine mainstream
- Gypsum mining machinery in pakistan stone crusher machine
- Produsen Mesin Crusher Usde Kuarsa
- used stone hammer mill ukeation
- spare parts ne crusher
- Crushing Plant Pilipinas
- 50Tph Gold Ore Crusher
- Youtube Sand Cast Manufactur
- penghancur batu disita di India
- granite quaries in and around bargur
- crusher and grinding mill price in malaysia