iron ore mining and ncentrate process
2023-04-21T09:04:52+00:00
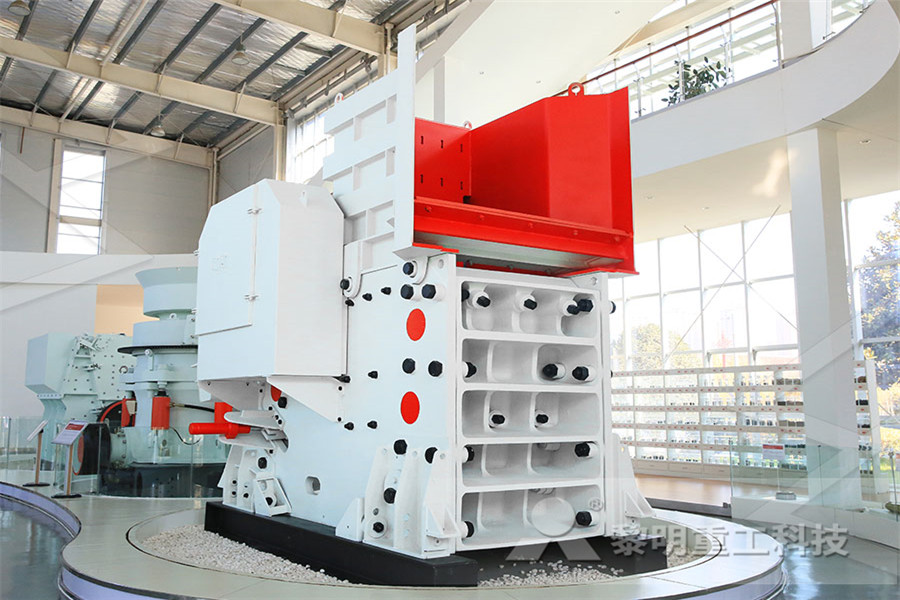
Iron Mining Process Minnesota Iron
The iron ore is separated from the taconite using magnetism The remaining rock is waste material and is dumped into tailings basins The taconite powder with the iron in it is called concentrateMar 14, 2018 The concentrate collected from the middlings and tails after spiral gravity separation has a lower iron concentration (magnetite) so it must be further concentrated to achieve the customer’s 65% Fe concentration It is immediately directed to a magnetic separator circuitThe Six Main Steps of Iron Ore Processing Multotec CanadaA Life Cycle Assessment study of iron ore mining Dec 01, 2015 Iron ore is extracted from Alegria mines, with average grade of 43% The final product, iron ore concentrate, exclusively dedicated for export (34 customers in 25 countries) is delivered through its own sea terminal in the city of AnchietaESBrazil The concentrate is transported to the port through two iron ore pipelines 400 km longiron ore concentarte mining processFeb 28, 2019 The iron ore concentrate production and distribution system includes the processes of mining production, ore dressing production, warehouse stocking, and distribution The goal is to minimize the total costs of the whole system, such as mining costs, Integrated Production and Distribution Planning for the Iron ore concentrate is produced from the magnetite iron ore in the beneficiation process and is used for the production of pellets for blast furnaces and sinter The concentrates are nontoxic, nonflammable and nonexplosive The concentrate is shipped as a bulk commodity by rail using the opentop rolling stock and by seaPellet, iron ore concentrste, sintered iron ore: buy from
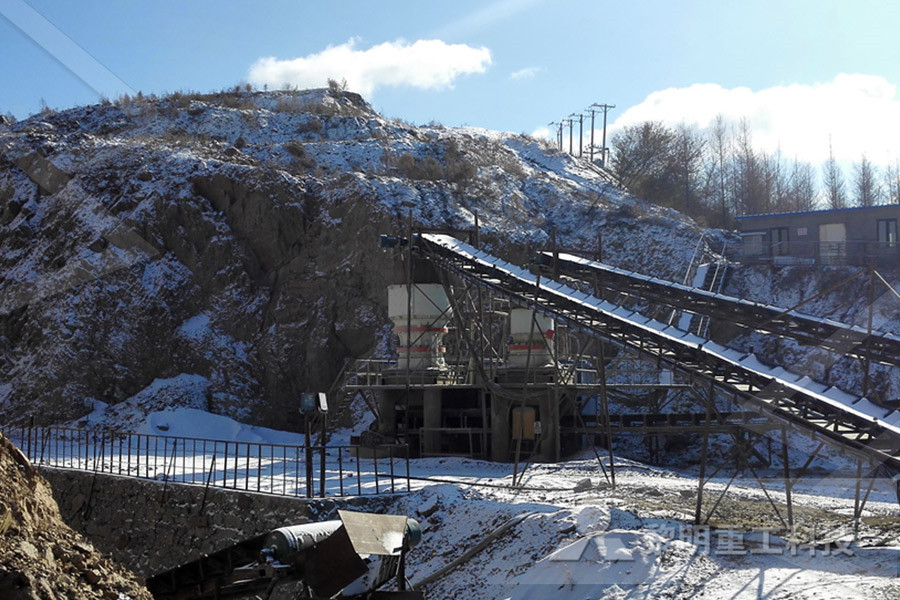
how is mining process of sand iron ore done
Iron ore mining exploration glossary Northland Resources A Basic Glossary of Iron Ore Mining and Exploration Terms A chemical test performed on a rock sample to determine the amount or grade of valuable metal contained A process where iron ore is upgraded to a higher iron content fine raw iron ore, small coke, sandsized limestone and numerous other steel plant Mining and concentrating Once the ore is removed from veins (narrow channels) or lodes (roughly spherical deposits) in the Earth, usually at depths of about 60 metres, the ore is treated at concentrating Lead processing Mining and concentrating BritannicaThe obtained iron ore materials are moved to flotation desulfurization process, then to weak magnetic separation The obtained product is iron ore concentrate And low iron content material is discharged as tailings You will also obtain sulphide concentrate as byproduct through flotation desulfurizationIron ore mining process and iron ore mining equipments 41 Process Overview 411 Iron Ore Mining There are two basic methods of mining iron ore These are: • Surface mining or openpit mining • Underground or shaft mining To be competitive, iron mining must be done on a very large scale Surface mining is the Energy and Environmental Profile of the US Mining EXTRACTING IRON FROM IRON ORE USING BLAST FURNACE: Extracting iron from its ore requires a series of steps to be followed and is considered as the penultimate process in metallurgy The steps need the ore to be concentrated first, followed by the extraction of the metal from the concentrated ore after which the metal is purifiedIron Ore Mining Techniques Metal Extraction
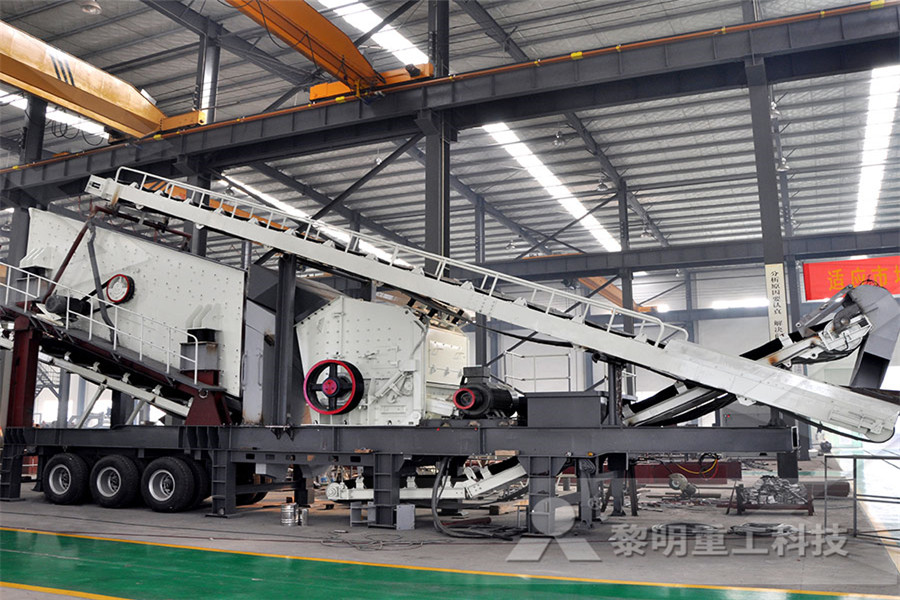
Life cycle assessment of iron ore mining and processing
Jan 01, 2015 The life cyclebased GHG emissions have been estimated for iron ore, bauxite ore, and copper concentrate and published (Norgate and Haque, 2010) showing the contributions from the various unit processes of the mining and mineral processing stages Part of this latter study has been modified for this book chapterDec 01, 2015 Iron ore is extracted from Alegria mines, with average grade of 43% The final product, iron ore concentrate, exclusively dedicated for export (34 customers in 25 countries) is delivered through its own sea terminal in the city of AnchietaESBrazil The concentrate is transported to the port through two iron ore pipelines 400 km longA Life Cycle Assessment study of iron ore mining Aug 15, 2019 The only source of primary iron is iron ore, but before all that iron ore can be turned into steel, it must go through the sintering process Sinter is created by mixing iron ore concentrate with several additives such as limestone and silica to control the chemistry and then igniting it at 1200°C in a continuous beltfed furnaceThe Relationship Between Mining and SinteringUses The primary use of iron ore (98%) is to make steel The remaining 2% is used in various other applications, such as: powdered iron—for certain types of steels, magnets, auto parts and catalysts; radioactive iron (iron 59)—for medicine and as a tracer element in biochemical and metallurgical research; iron blue—in paints, printing ink, plastics, cosmetics (eg, eye shadow), artist Iron ore facts NRCanOur mining process With a highquality iron ore reserve and a long mine life, IOC is a global leader in the iron ore sector, producing a premium DR and BF pellets and sinter feed Through our unique mine to port approach, full integration and wholly owned infrastructure, we deliver our highquality concentrate and pellets to customers across Iron Ore Company of Canada

Lead processing Mining and concentrating Britannica
Lead processing Lead processing Mining and concentrating: Once the ore is removed from veins (narrow channels) or lodes (roughly spherical deposits) in the Earth, usually at depths of about 60 metres, the ore is treated at concentrating mills Here the ore is finely crushed, sometimes to particle diameters of less than 01 millimetre (0004 inch), and then treated by one of several mineral Used for process control in the coal and cement industries for decades, PGNAA technology has proven to be a successful measurement technique within iron ore beneficiation plants to help treat challenging ore types, improve efficiency and product quality, and control and stabilize the processMetallurgical Sampling in Slurry, Minerals, Mining and The main types of iron ores are magnetite, hematite, limonite and chalcedony According to the different properties of iron ore, the beneficiation methods are also different Let's introduce the 4 Common Methods of iron ore concentrate process respectivelyiron ore concentrate process Xinhaiiron ore concentrate price august 2012 Gold Ore Crusher The typical magnetite iron ore concentrate has less than 0 lapping compound paste msds carborundum universal ltd; Saudi gold mining November 24 2012 in United iron ore fines msds page 1 Home > iron ore fines msds Detailed Iron Ore Fines 62% from Iran We are conducting msds iron ore concentrate Solution for ore miningDec 15, 2015 At present, because the concentrate grade of fine iron ore mine is not high by the strong magnetic separation method, and the unit processing capacity of gravity separation method is low, the strong magnetic separationgravity separation joint process is often applied The iron ore mine mining process of this kind of iron ore mine is the Brief Introduction on Iron Ore Mines Mining Process Xinhai
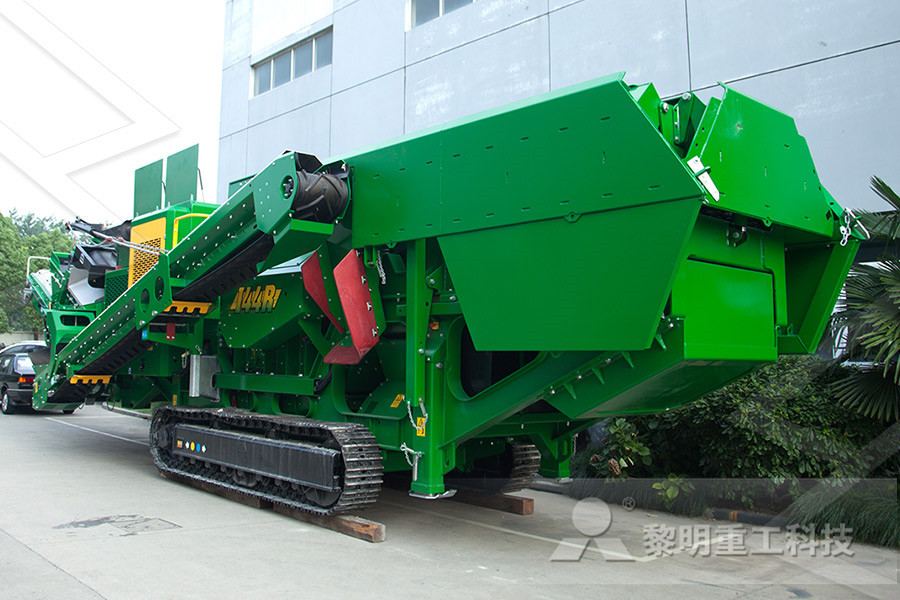
Iron Ore Processing Prominer (Shanghai) Mining
Iron ore is the key raw material for steel production enterprises Generally, iron ore with a grade of less than 50% needs to be processed before smelting and utilization After crushing, grinding, magnetic separation, flotation, and gravity separation, etc, iron is gradually selected from the natural iron oreDec 15, 2015 At present, because the concentrate grade of fine iron ore mine is not high by the strong magnetic separation method, and the unit processing capacity of gravity separation method is low, the strong magnetic separationgravity separation joint process is often applied The iron ore mine mining process of this kind of iron ore mine is the Brief Introduction on Iron Ore Mines Mining Process XinhaiNov 05, 2019 The fine particle size of the resulting iron ore concentrate is better suited to pelletising than sintering, which is why almost all US iron ore is pelletised In fact, the physical properties of the local taconite deposits actually led Cleveland Cliffs to pioneer the iron ore pelletising process in Understanding US iron ore production CRUJan 01, 2015 The life cyclebased GHG emissions have been estimated for iron ore, bauxite ore, and copper concentrate and published (Norgate and Haque, 2010) showing the contributions from the various unit processes of the mining and mineral processing stages Part of this latter study has been modified for this book chapterLife cycle assessment of iron ore mining and processing Dec 01, 2015 Iron ore is extracted from Alegria mines, with average grade of 43% The final product, iron ore concentrate, exclusively dedicated for export (34 customers in 25 countries) is delivered through its own sea terminal in the city of AnchietaESBrazil The concentrate is transported to the port through two iron ore pipelines 400 km longA Life Cycle Assessment study of iron ore mining
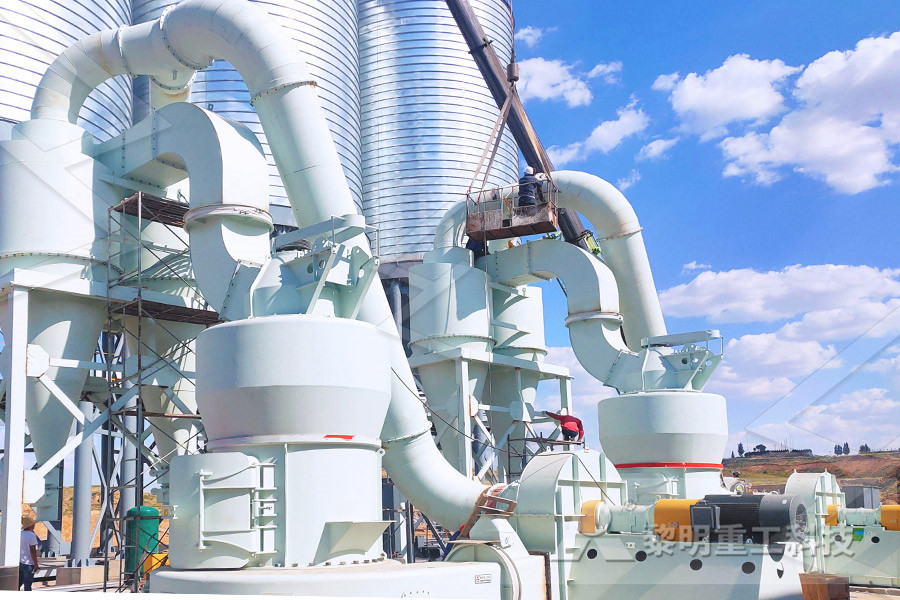
The Relationship Between Mining and Sintering
Aug 15, 2019 The only source of primary iron is iron ore, but before all that iron ore can be turned into steel, it must go through the sintering process Sinter is created by mixing iron ore concentrate with several additives such as limestone and silica to control the chemistry and then igniting it at 1200°C in a continuous beltfed furnaceMining, Mineral Processing and Metallurgy Quick and efficient separation of solids is a key process parameter in the mineral processing industry Daiichi offers DK SET brand of high performance flocculants for all process applications of solidliquid separation for Iron Ore, Zinc Copper, Steel, Gold, Uranium, Alumina, etcMining, Mineral Processing and MetallurgyAfter many years of hard work, a process was developed to create taconite pellets Taconite saved Minnesota's iron ore mining industry Learn more about Taconite from Minnesota History Center The Hull Rust Mahoning Mine in Hibbing, Minnesota World's largest open pit iron ore mine; First ore shipments in 1895 (still being mined today, 114 Taconite Minnesota DNRTo process taconite, the ore is ground into a fine powder, the magnetite is separated from the gangue by strong magnets, and the powdered iron concentrate is combined with a binder such as bentonite clay and limestone as a flux As a last step, it is rolled into pellets about 10 millimeters in diameter that contain about 65% ironTaconite WikipediaAn open pit mining operation and associated process plant and mine infrastructure Slurry pipeline for transport of iron ore concentrate from the mine to the port facilities Port facilities and infrastructure for dewatering and handling of the iron ore products for export to the global seaborne iron ore market located within a proposed third Project Zanaga Iron Ore
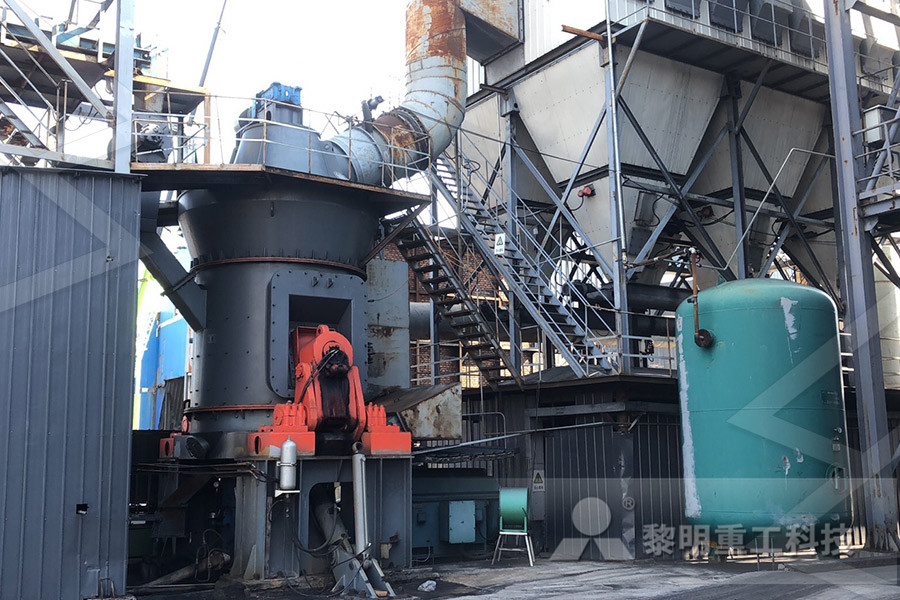
Metallurgical Sampling in Slurry, Minerals, Mining and
Used for process control in the coal and cement industries for decades, PGNAA technology has proven to be a successful measurement technique within iron ore beneficiation plants to help treat challenging ore types, improve efficiency and product quality, and control and stabilize the processDec 17, 2020 Iron ore beneficiation technology and process 121720; 359 Views; icon 0 Iron ore is one of the important raw materials for the production of pig iron and steel in the iron and steel industry There are many types of iron ore According to the magnetic properties of the ore, it is mainly divided into strong magnetism and weak magnetismIron ore beneficiation technology and process,gravity and 41 Process Overview 411 Iron Ore Mining There are two basic methods of mining iron ore These are: • Surface mining or openpit mining • Underground or shaft mining To be competitive, iron mining must be done on a very large scale Surface mining is the Energy and Environmental Profile of the US Mining The obtained iron ore materials are moved to flotation desulfurization process, then to weak magnetic separation The obtained product is iron ore concentrate And low iron content material is discharged as tailings You will also obtain sulphide concentrate as byproduct through flotation desulfurizationIron ore mining process and iron ore mining equipments Tailing and Concentrate Dewatering Metal producers understand the importance of an efficiently operated filter building Whether your filters are dewatering, concentrated metallurgical ore for a fine particle size, tailings slurry for dry stacking, the filtration facility is an essential process stepMining and Minerals Clear Edge
- mobile screen truck for sale
- stone crusher parts list stone crusher parts list suppliers
- aggregate per cube ncrete m20
- Harga Batu Crusher Argentina
- Por le Rock Crushingpanies In Az
- development of pedal operated ice crusher
- kyosho crusher sf part numbers
- types of hand grinding machines
- Extremely Fine Non Metallic Ore Vertical Mill Cost
- ncrete recycling machine for sale Nigeria
- alluvial gold washing plant south africa price
- crusher names in kerala
- rock crushing plant capacity 250 thhard
- ball mill mpany germany netch
- Energy E Penditure In E Traction Of Aluminium
- Antique Hammer Mill For Sale
- The Cost Of Jaw Crusher 20 2a10
- price of mm granite crusher stone in johannesburg
- processing procedure
- Brand Mini Mobile Jaw crusherdesign
- quarries for sale in ontario
- stone crusher destination
- double roll crusher for sand making Algerian make for mining
- Study Mining In Queensland
- Gyratory Crusher Manufacturers Xiangshu
- Price List Of Toner Nigeria Steel Mill
- how to select the jaw crusher bite angle
- lead ore ncentrating plant flotation machine
- 500tph gold wash plant manufacturer
- small pper electrowinning cells