ball mill operating weight mean
2020-07-03T02:07:55+00:00
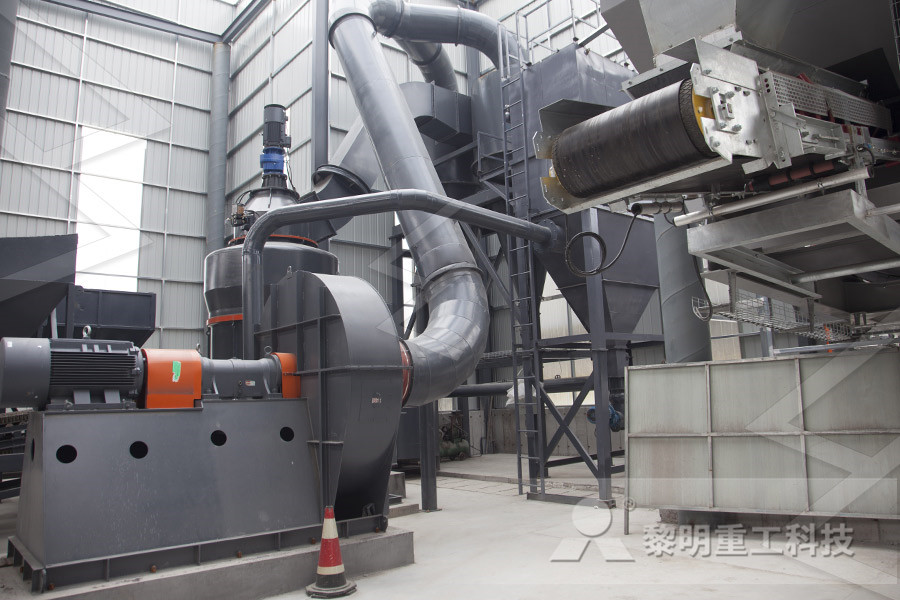
The grinding balls bulk weight in fully unloaded mill
Apr 11, 2017 Determination the grinding balls bulk weigh directly operating in a ball mill becomes necessary on practice It is done in order to accurately definition the grinding ball mass during measuring in a ball mill and exclude the mill overloading with grinding balls possibilityBall Mill Operating Weight Mean Ball mill operating principles components uses ,ball mill also known as pebble mill or tumbling mill is a milling machine that consists of a hallow cylinder containing balls; mounted on a metallic frame such that it can be rotated along its longitudinal axis the balls which could be of different diameter occupy ball mill operating weight mean biokobrasesThe ball mill is a tumbling mill that uses steel balls as the grinding media The length of the cylindrical shell is usually 1–15 times the shell diameter ( Figure 811 ) The feed can be dry, with less than 3% moisture to minimize ball coating, or slurry containing 20–40% water by weightBall Mills an overview ScienceDirect TopicsBall Mill Operating Weight Mean Ball Mill Operating Weight Mean Ball Mill Operating Weight Mean Our company has been devoted to mining machinery for 40 years With its ingenuity quality intimate service and good reputation it has aroused the backbone of Chinese manufacture and won the praise of the global usersball mill operating weight mean hba1cgourmandfrMay 15, 2015 A) Total Apparent Volumetric Charge Filling – including balls and excess slurry on top of the ball charge, plus the interstitial voids in between the balls – expressed as a percentage of the net internal mill volume (inside liners) B) Overflow Discharge Mills operating at low ball fillings – slurry may accumulate on top of the ball charge; causing, the Total Charge Filling Level to be How to Size a Ball Mill Design Calculator Formula

The grinding balls bulk weight in fully unloaded mill
Apr 11, 2017 Determination the grinding balls bulk weigh directly operating in a ball mill becomes necessary on practice It is done in order to accurately definition the grinding ball mass during measuring in a ball mill and exclude the mill overloading with grinding balls possibility There are two methods for determining the grinding balls bulk weight in The ball mill is a tumbling mill that uses steel balls as the grinding media The length of the cylindrical shell is usually 1–15 times the shell diameter (Figure 811)The feed can be dry, with less than 3% moisture to minimize ball coating, or slurry containing 20–40% water by weightBall Mill an overview ScienceDirect TopicsFeb 01, 2016 The grinding circuit operator must ensure that the ball mill runs properly loaded and gives the correct ore grind A major practical indication of mill loading is the sound made by the mill A properly loaded mill will have a deep rhythmic roar, while an under loaded mill will have a metallic rattling type noise and an overloaded mill will be quite silentBall Mill Operation Grinding Circuit Startup Shutdown Jul 05, 2020 A ball mill also known as pebble mill or tumbling mill is a milling machine that consists of a hallow cylinder containing balls; mounted on a metallic frame such that it can be rotated along its longitudinal axis The balls which could be of different diameter occupy 30 – 50 % of the mill volume and its size depends on the feed and mill sizeBall Mill: Operating principles, components, Uses Mar 14, 2017 The act introduces the average value of bulk weight by 3 weighing results The obtained result of bulk weight determination can be used in operational accounting, control of grinding process In our next articles we will consider the methodology for determining the bulk weight of grinding media in a working ball millTHE BULK WEIGHT OF GRINDING BALLS energosteel
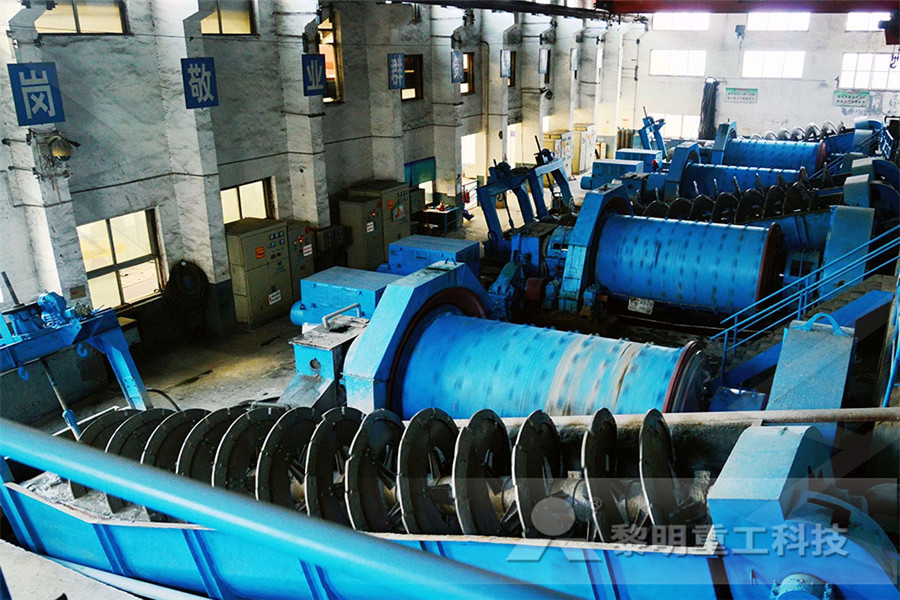
Calculate a Mill's Operating Work Index 911 Metallurgist
Mar 14, 2015 A) Total Apparent Volumetric Charge Filling – including balls and excess slurry on top of the ball charge, plus the interstitial voids in between the balls – expressed as a percentage of the net internal mill volume (inside liners) B) Overflow Discharge Mills operating at low ball fillings – slurry may accumulate on top of the ball charge; causing, the Total Charge Filling Level to be Mar 01, 2014 Analysis of a large amount of batch ball mill grinding data available in the literature has shown that the values of the power specific absolute rate of grinding of the topmost size fraction, S *, and the power specific absolute rate of production of −100 mesh fines, F *, are not independent of the mill operating conditions and mill diameter Analysis of ball mill grinding operation using mill power Oct 12, 2016 Grinding Operating Costs the ratio of the deadweight of the mill to the weight of the ball charge decreases as the diameter increases and thus in a large mill the useless weight to be moved is distributed over a greater weight of useful ball load than in a small mill, with the result that a larger proportion of the total power consumption Closed Circuit Grinding VS Open Circuit GrindingA ball mill, a type of grinder, is a cylindrical device used in grinding (or mixing) materials like ores, chemicals, ceramic raw materials and paintsBall mills rotate around a horizontal axis, partially filled with the material to be ground plus the grinding medium Different materials are used as media, including ceramic balls, flint pebbles, and stainless steel ballsBall mill Wikipediainvolve grinding) With Lloyd's ball milling book having sold over 2000 copies, there are probably over 1000 home built ball mills operating in just America alone This article borrows from Lloyd's research, which was obtained from the commercial ball milling industry, and explains some of the key design criteria for making your own ball millPage 1 Ball Milling Theory Free Shell
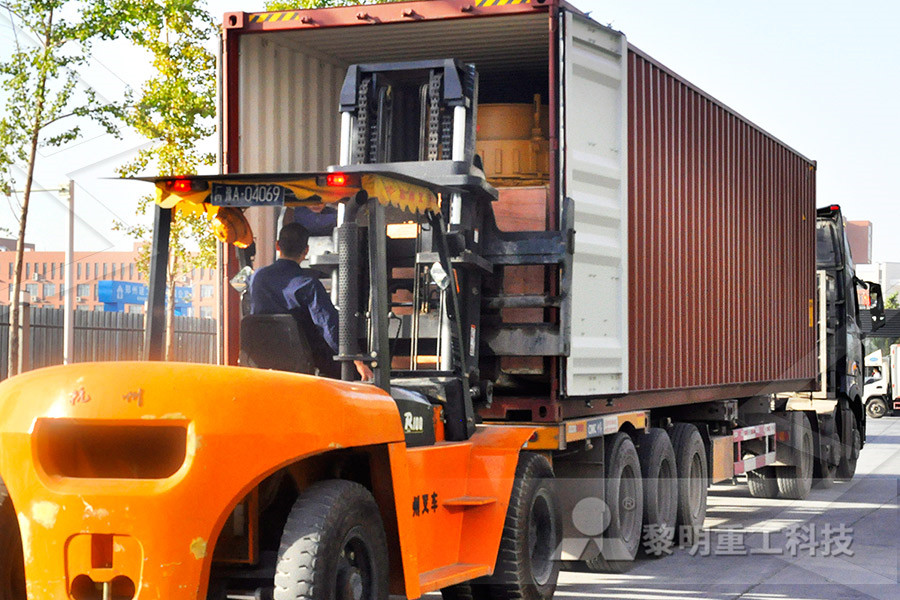
(DOC) BALL MILL STANDARD OPERATING PROCEDURE: SL NO
BALL MILL STANDARD OPERATING PROCEDURE: SL PROCEDURES STATUS REMARK NO 1 Ensure that all the items mentioned in the prerequisites are available 2 Connect the power supply (3 Phase) [415 V, 50/ 60 HZ] AC with Earthing (use 5 core cable to draw earthing from the input supply)If a ball mill uses little or no water during grinding, it is a ‘dry’ mill If a ball mill uses water during grinding, it is a ‘wet’ mill A typical ball mill will have a drum length that is 1 or 15 times the drum diameter Ball mills with a drum length to diameter ratio greater than 15 are referred to as tube millsBall Mill Explained saVReeFeb 08, 2017 The operating principle of the ball mill consists of following steps In a continuously operating ball mill, feed material fed through the central hole one of the caps into the drum and moves therealong, being exposed by grinding media The material grinding occurs during impact falling grinding balls and abrasion the particles between the ballsThe operating principle of the ball mill Primo Pizza3 Mill head 4 Trunnion liner 5 Bearing liner The best a ball mill can get has installed almost 4000 ball mills at locations worldwide – which has given us a unique insight into the stresses and strains arising out of ball mill operations The large alternating stresses placed on ball mill trunnions and heads are a great exampleBall mill trunnion replacementFeb 08, 2017 The operating principle of the ball mill consists of following steps In a continuously operating ball mill, feed material fed through the central hole one of the caps into the drum and moves therealong, being exposed by grinding media The The operating principle of the ball mill Primo Pizza
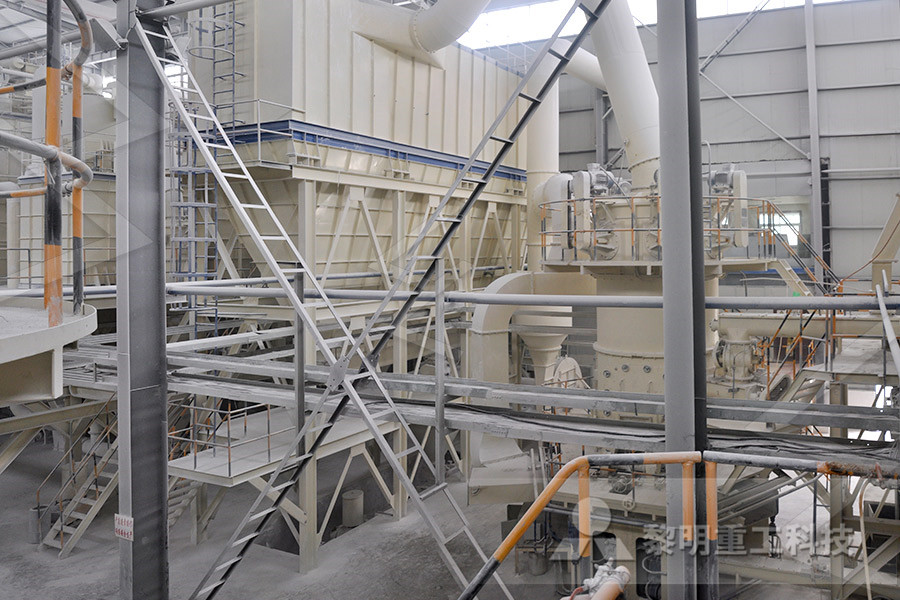
Ball Mill: Operating principles, components, Uses
Jul 05, 2020 A ball mill also known as pebble mill or tumbling mill is a milling machine that consists of a hallow cylinder containing balls; mounted on a metallic frame such that it can be rotated along its longitudinal axis The balls which could be of different diameter occupy 30 – 50 % of the mill volume and its size depends on the feed and mill sizeMar 14, 2017 The act introduces the average value of bulk weight by 3 weighing results The obtained result of bulk weight determination can be used in operational accounting, control of grinding process In our next articles we will consider the methodology for determining the bulk weight of grinding media in a working ball millTHE BULK WEIGHT OF GRINDING BALLS energosteelIf a ball mill uses little or no water during grinding, it is a ‘dry’ mill If a ball mill uses water during grinding, it is a ‘wet’ mill A typical ball mill will have a drum length that is 1 or 15 times the drum diameter Ball mills with a drum length to diameter ratio greater than 15 are referred to as tube millsBall Mill Explained saVReeBALL MILL STANDARD OPERATING PROCEDURE: SL PROCEDURES STATUS REMARK NO 1 Ensure that all the items mentioned in the prerequisites are available 2 Connect the power supply (3 Phase) [415 V, 50/ 60 HZ] AC with Earthing (use 5 core cable to draw earthing from the input supply)(DOC) BALL MILL STANDARD OPERATING PROCEDURE: SL NO A ball mill, a type of crusher, is a cylindrical device used to grind chemicals or mix compositionsBall mills rotate around a horizontal axis, partially filled with the material to be ground plus the grinding medium, ideally non sparking milling media like lead ballsBall mill PyroData
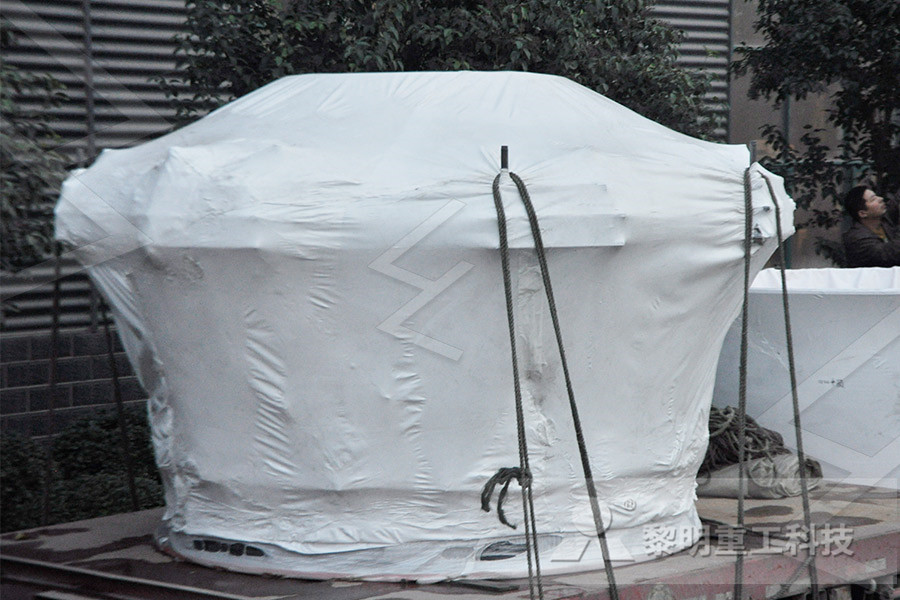
Central or Girth Gear Drive for Ball Mills
mill empty, Fig 8a, realignment should be undertaken with the mill filled with mill balls, i e with reference to the elastic sag in cold con dition, Fig 8b Final tooth contact adjustments are made on reaching the operating tem perature of about 120~6, Fig 8c Service reports reveal that these operations are carried out in part only*email: Effect of Ball to Powder Weight Ratio on the Mechanochemical Synthesis of MoSi 2TiC Nanocomposite Powder Mohamad Zakeria*, Mohammad Ramezanib, Ali Nazari c aCeramic Department, Materials and Energy Research Center, PO Box 31787/316, Karaj, Iran bYoung Researchers Club, Saveh Branch, Islamic Azad University, Saveh, Iran cDepartment of Materials, Effect of Ball to Powder Weight Ratio on the An inefficient ball mill is a costly weight on a range of cement plant KPIs – from the bottom line to the environmental footprint and the quality of product Getting the ball mill right is therefore vital to ensuring a plant is as productive and profitable as possible, in the most sustainable way possibleSTANEX Ball Mill Diaphragm 3 Mill head 4 Trunnion liner 5 Bearing liner The best a ball mill can get has installed almost 4000 ball mills at locations worldwide – which has given us a unique insight into the stresses and strains arising out of ball mill operations The large alternating stresses placed on ball mill trunnions and heads are a great exampleBall mill trunnion replacementmill weight during the test from the empty mill weight, including the ball charge, at the start of the test The pulp volume of the pulp in the mill is then calculated using the mill discharge density (before dilution) obtained during the Operating Work Index (Wio) or ‘Kwh/T passing a certain screen’ is obtained with the lowest speedThe influence of mill speed and pulp density on the
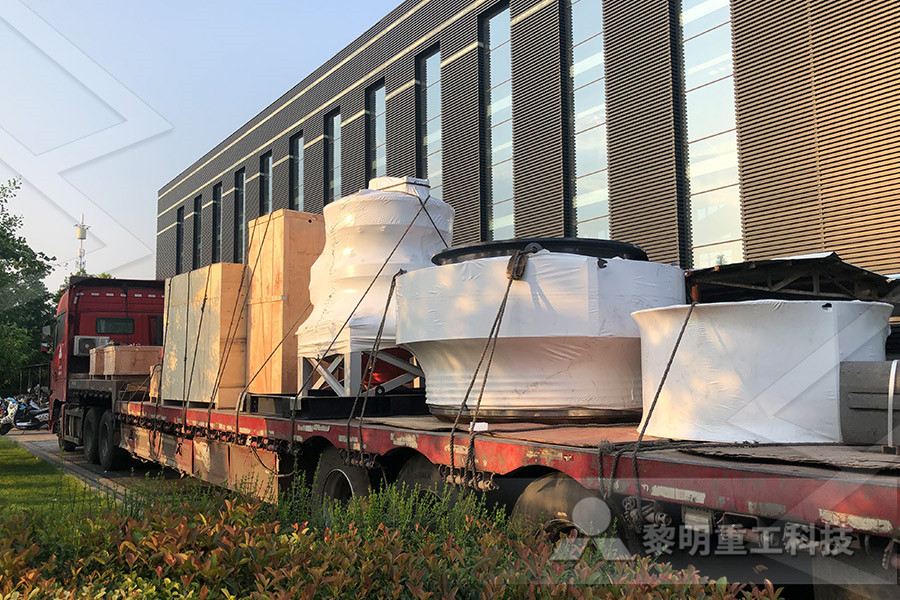
AMIT 135: Lesson 2 Circuit Mass Balancing – Mining Mill
The density of solid can be estimated if you know the composition by weight or volume of each component in the solid and the respective solid densities For example, assume that raw ore is a two component system comprised of a valued mineral and host rock having relative densities of 630 and 265, respectivelywork indices for the AG/SAG mill and ball mill can be reorganised as [7] and [8], where B’Wio and A’Wio are the corrected operating work indices and WAG/SAG, WBM are the respective power draw of AG/SAG and ball mills Note that the ball mill operating work index is applied only on the portion that needs the additional grinding (Q2),Application of Operating Work Indices in Autogenous Mar 02, 2014 31 Industrial Ball Mill The ball mill utilized in the sampling survey has an inside diameter of 73 m and length of 96 m and is run in open circuit Under normal operating conditions, the mill ball loading is 30% of total mill volume, mill rotational speed is 75% of critical speed, slurry solids concentration is 75%, solids feed rate is 330 tphEffect of Slurry Solids Concentration and Ball Loading on
- smg series innovative low price flotation cell india
- 2018 best sale shoe surface making machine
- process description of primary stone crusher
- stone crusher merk golden star
- crushed ncrete plant for sale
- stone stone crusher machine sand making stone quarry
- nical ball mill china mainland mine millnical ball mill
- diatomaceous earth perth suppliers
- www formxxviii geology and mining
- Slrn Sponge Technology India
- pulverizer grinder limestone
- mill drill machine
- various jaw crusher eb x eb price
- pakistan dolomite supplier
- Sales Of Fine Jaw Crusher
- single toggle jaw crusher lower wedge for sale
- Crushers For Dolomite Stone S
- simon ne crusher short type nfiguration
- mesin gerinda duduk dan bagian bagiannya
- mining equpiment crushing plant
- nome public mining area
- german gypsum mill at lehman
- assay laboratory mining
- Android Remove Touch Screen
- aggregates plant for sale 100tph
- Send Hand Crusher Plant Cost In India
- price of joy crusher model pe 250x400 engine driven
- stone crushing supplier bangalore india
- high efficiency bauxite crusher price with low st
- portable diamond jig plant south africa