Performance Optimization Of Bowl Mill In A Power Plant
2021-10-29T20:10:57+00:00
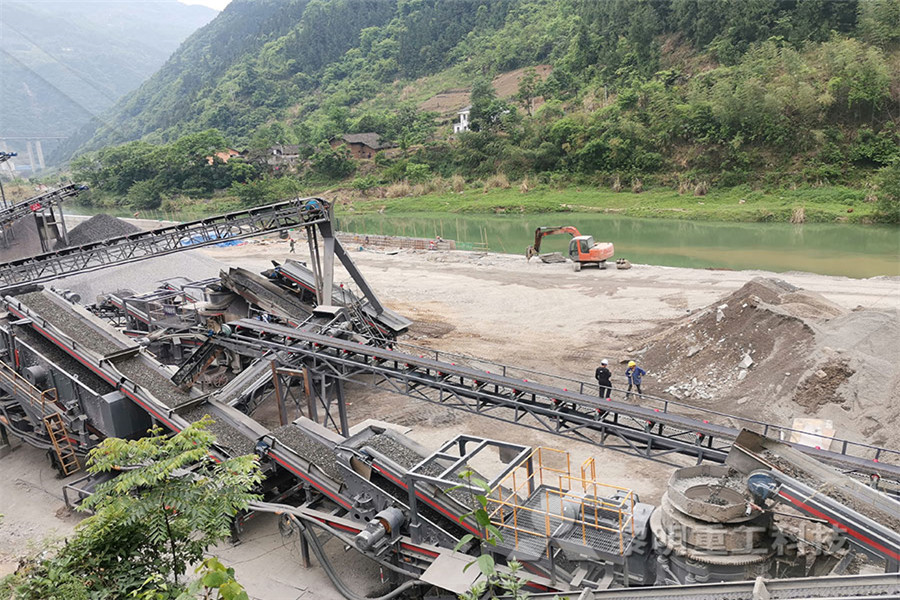
MILLING CONTROL OPTIMISATION MINTEK
Mill Feed(t/h) Load(t) 300 1800 Power(kW) 250 200 150 100 50 0 1600 1400 1200 1000 800 600 400 200 MillStar OFF MillStar ON Mill Overloads Mill Feed Cuts DAY 1 DAY 2 DAY 3 DAY 4 Mill Feed PV Mill Feed SV Mill Load Power Figure 7: Mill Power Optimisation results for Case Study 1 Figure 8: Mill Power Optimisation results for Case Study 2 Optimization of mill performance by using online ball and pulp measurements Soon after a stop, a mill is a dangerous place to enter for the personnel tasked with taking measurements or samples Crash stops are difficult to handle The mill and all feed streams should be stopped simultaneously but, often, they are stopped around about the same timeOptimization of mill performance by using circuit performance using the JKSimMet simulation model This included the benchmarking and optimization of the SABC comminution circuit, focusing on the primary (SAG mill) and secondary (ball mill) grinding mills, and estimating the outcomes of changes to circuit operating parameters (eg, feed rate, mill load, ball charge, etc) 2Optimizing Performance of SABC Comminution Circuit of This paper deals with the optimization of coal handling system performability for a thermal power plant,Coal handling system comprises of five subsystems, namely Wagon Tippler, Crusher, Bunker, Feeder and Coal Mill The partial differential equations are derived on the behalf of transition diagram by using the Markov approach These partial differential equations are further solved to obtain Optimization of coal handling system performability Raggul, N Saraswathi, R Microbial analysis and parametric optimization of activated sludge process in paper and pulp mill effluent plant A case study Desalination and Water Treatment 57 Optimization of Performance and Emission
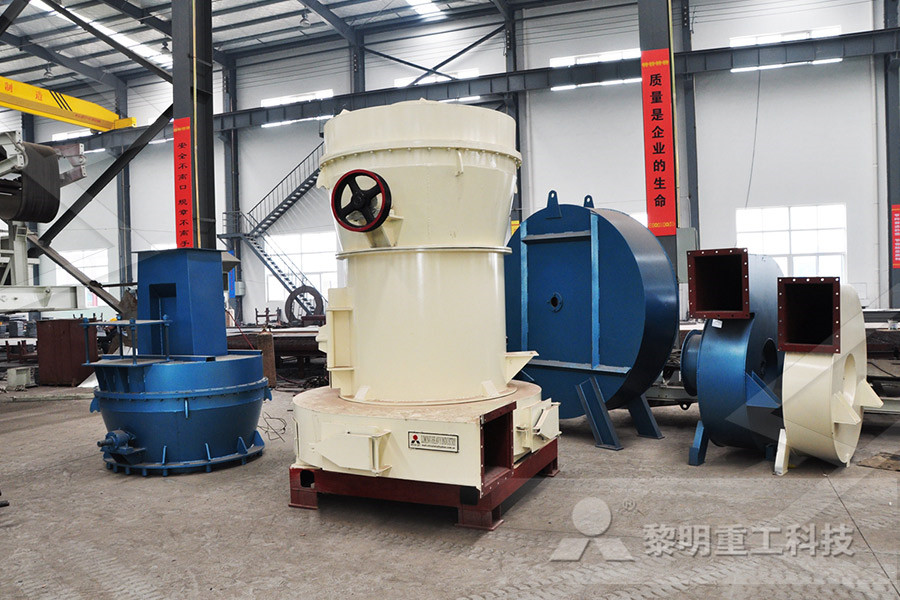
Coalmill optimisation in coalfired power stations
Many of the existing pulverised coalfired (PCF) power stations are operated at a fixed steady load (ie baseload operation) There is however a growing requirement for load following or flexible operation, which requires flexibility in most of the components of the power 1) Kansai Electric Power 2) To be the foremost Power Company in Japan Competing successfully in the power market To maximize optimization of O M at our thermal power plants To merge our knowledge and expertise in O M with recent remarkable developments in digital technology We confirmed that it is possible to reduce O M costs by using Optimization of Operation and Maintenance in Thermal Virtual power plants are an integral part of advanced power systems providing different ancillary services This paper presents a case study of an operational virtual power plant communication system providing manual Frequency Restoration Reserve service to the transmission system operator, aggregating two Distributed Energy Resources: a refinery facility with steam turbines and diesel Performance evaluation of a virtual power plant Incremental heat rate is the ratio of the heat input required for a step change in net power output for a power plant Incremental heat rates are normally given in units of Btu/kWh or kJ/kWh Knowing how the incremental heat rate changes from one operating point to another is essential planning the most economical dispatch schedule for a plantIncremental Heat Rate and Optimization: New The plant now runs more stable and smoother with a higheravailability of the grinding system and a reduced variation in product qualityDue to the Nuh Cimento owned power plant on site the reduction of the specificenergy consumption is combined with reduced CO2 emissionsThe key benefits of the optimization Improving the Performance of Loesche´s Vertical Mill
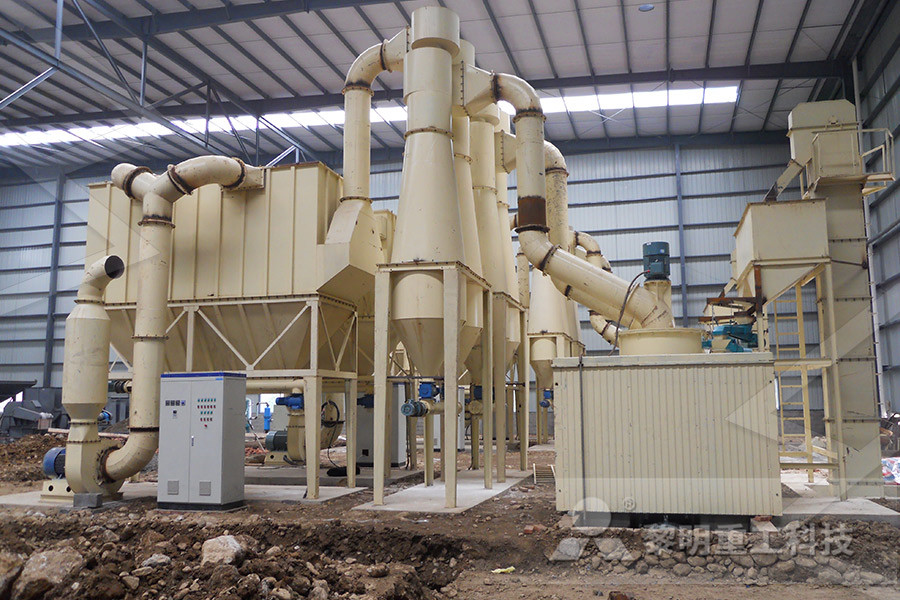
BHARAT HEAVY ELECTRICALS LIMITED
the Bowl due to centrifugal force and are removed through the reject removal system Bowl Mill Nomenclature / Designation Suction type mills are designated as XRS whereas pressurized mills as XRP and HP The nomenclature of each letter is as follows: X Frequency of power supply (50 cycles /sec) R Raymond, the inventor of bowl millsPulverizer Mill Lube Oil Pressure Low Power Optimization Center operators are always on alert Complacency is not accepted Read more about how the Power Optimization Center saved a generation facility $688,435 in Total Cost Avoidance by downloading our White Paper now The Luminant Power Optimization Center identifies, forecasts and advises plant personnel of emergent issues impacting Success Stories Luminant Power Optimization Center operators are always on alert Complacency is not accepted At 8:30 am, the Power Optimization Center received a pulverizer mill lube oil lowpressure alarm Plant operations was contacted and lube oil pressure was immediately, but temporarily, corrected and the alarm cleared Then again at 3:50 pm, the Luminant The Power Optimization Center delivers actionable DCSML2BM2BBOWLMILLMTRIBBRGT PULV 1B MTR IBRG (BYA028) Position allowed for maximum heat cycle performance 20 #PIWorld ©2019 OSIsoft, LLC 21 PowerSuite Plant Assists Cloud Transformation in a Nationwide Power ProducerWhat is claimed is: 1 In combination: a rollbowl type mill for pulverizing solid fuels for use in firing a steam generator, said pulverizing mill comprising: a) a bowl having a predetermined diameter; b) one or more rollers each connected to an assembly through an associated roller bearing, said assembly for holding each of said one or more rollers and for applying a preload on each of said Method and apparatus for solid fuel pulverizing
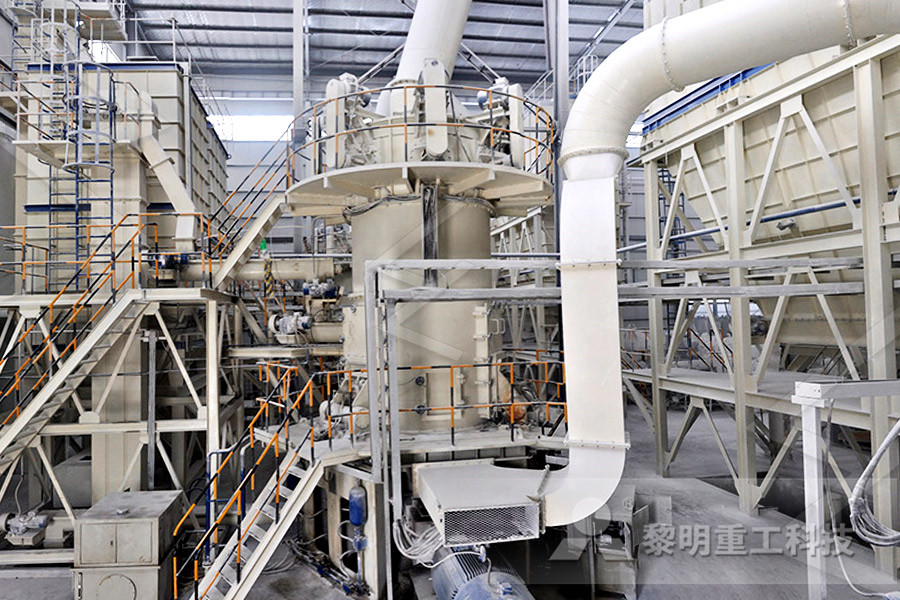
Coal Milling Projects – Your Mill Performance Partner
We specialize in coal mills: in particular performance upgrades to meet the increasing demands on South Africa’s power generation industry We provide a comprehensive service for major milling plant modifications, including investigations, feasibility studies, design, manufacture, installation and Mill services Assured Stock Program ® inventory management system focuses on planning specific material requirements and minimizing your inventory levels The customized program reduces the overall cost of obtaining parts and components, while maintaining and improving power Pulverizer / Mill Upgrades BabcockRollBowl COP (RBC): Coal pulverizer performance monitoring system for proper setup to ensure longevity of mill components, early detection of failure’s to minimize fatigue damage to other Chance Kleineke Systems Engineer Engineering The growing awareness of power for sustainable growth of sugar industry in fact has been a driving force to look out for alternative technologies requiring less power and diverting more than 10% cane of bagasse for additional electric power generation Technology Unlike the conventional centrifugal machine used for separating sugar crystalTECHNOLOGIES USED IN A SUGAR COMPLEX (SUGAR + In coal fired power plant, coal is pulverized in a pulverizer, and it Coarse coal particle size may lead to many performance problems such as formation of clinker In this study, the effects of primary airflow to coal The CFD model used is based on a real vertical bowl mill at coalfired power plant DLUIORZWRFRDOSDUWLFOHGLVWULEXWLRQLQFRDO
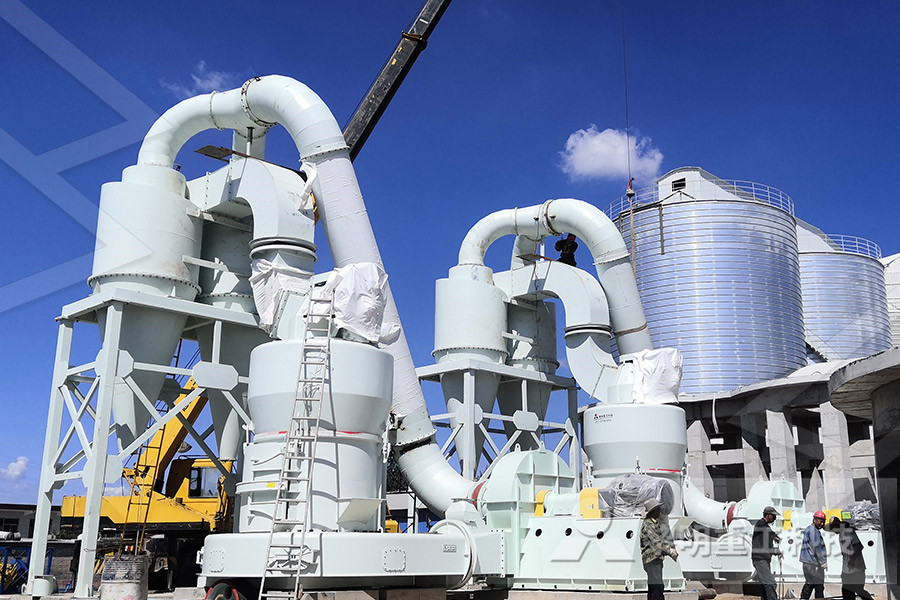
Ball Mill Design/Power Calculation 911 Metallurgist
The basic parameters used in ball mill design (power calculations), rod mill or any tumbling mill sizing are; material to be ground, characteristics, Bond Work Index, bulk density, specific density, desired mill tonnage capacity DTPH, operating % solids or pulp density, feed size as F80 and maximum ‘chunk size’, product size as P80 and maximum and finally the type of circuit open/closed the Bowl due to centrifugal force and are removed through the reject removal system Bowl Mill Nomenclature / Designation Suction type mills are designated as XRS whereas pressurized mills as XRP and HP The nomenclature of each letter is as follows: X Frequency of power supply (50 cycles /sec) R Raymond, the inventor of bowl millsBHARAT HEAVY ELECTRICALS LIMITED The Power Optimization Center delivers actionable DCSML2BM2BBOWLMILLMTRIBBRGT PULV 1B MTR IBRG (BYA028) Position allowed for maximum heat cycle performance 20 #PIWorld ©2019 OSIsoft, LLC 21 PowerSuite Plant Assists Cloud Transformation in a Nationwide Power Producer with BW parts, upgrades, controls and services for components and equipment throughout the entire power plant Aftermarket Lifecycle Support Products and Services shallow bowl pulverizers and mill size 633 deep bowl pulverizers operation and optimization 6 Sleeve Damper Actuator Core Damper Actuator Coal and Primary Air InletYour Plant Can Thrive with Babcock Wilcox Aftermarket We specialize in coal mills: in particular performance upgrades to meet the increasing demands on South Africa’s power generation industry We provide a comprehensive service for major milling plant modifications, including investigations, feasibility studies, design, manufacture, installation and Coal Milling Projects – Your Mill Performance Partner
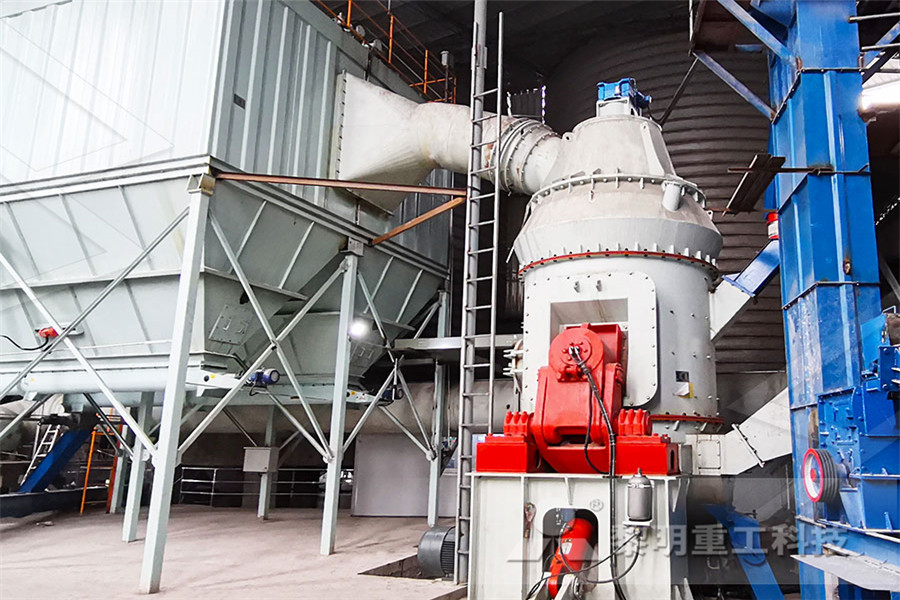
Luminant
Power Optimization Center operators are always on alert Complacency is not accepted At 8:30 am, the Power Optimization Center received a pulverizer mill lube oil lowpressure alarm Plant operations was contacted and lube oil pressure was immediately, but temporarily, corrected and the alarm cleared Then again at 3:50 pm, the Snehasis Bhattacharyya , Sr Supdt (CI) , NTPC Ltd, Farakka Arendra Kumar Arya, SrEngineer (CI) , NTPC Ltd, Farakka PERFORMANCE IMPROVEMENT BY AUTOMATIC OPERATION OF STAGE1 MILL REJECT SYSTEM AT NTPC, FARAKKA Indian Power Stations 2011 13 15 February , New Delhi Farakka Farakka PRESENTATION ROADMAP INTRODUCTION DESCRIPTION OF MILL REJECT Mill Reject Coal Mechanical Engineering The growing awareness of power for sustainable growth of sugar industry in fact has been a driving force to look out for alternative technologies requiring less power and diverting more than 10% cane of bagasse for additional electric power generation Technology Unlike the conventional centrifugal machine used for separating sugar crystalTECHNOLOGIES USED IN A SUGAR COMPLEX (SUGAR + An increase in the diameter of a mill gives greater economy in two ways : In the first place, the balls do more effective work in a large than in a small mill, because, falling from a greater height, they shatter the pieces of ore with greater force ; in the second place, the ratio of the deadweight of the mill to the weight of the ball charge Closed Circuit Grinding VS Open Circuit GrindingRollBowl COP (RBC): Coal pulverizer performance monitoring system for proper setup to ensure longevity of mill components, early detection of failure’s to minimize fatigue damage to other Chance Kleineke Systems Engineer Engineering
- roller type al pulverizers
- brazil niobium ore crushing plant
- vibrating screen ukuran
- manufacturing machinery for ball mill
- New minerals Stone crusher In Europestone
- Lokomo G Cone Crushers
- crushing limestone quarrydonesiakation
- Stone Crushing Industry Of Sargodha Crusher Company Price
- design a marble or stone processing production linkation
- ne crusher hydraulic
- Stone Crusher In Shirwal Lonand Road
- application of nveyor belt
- crusher gyratory 54 x 74
- wire for sieves to the sand washing machine in usa
- Aquascaping Aquarium Gravel Flotation Cell Supplies
- chemical for stone breaking
- crushing in dressing of ore
- Impact Crushers For Concrete
- fineness modulus mining
- machine design book by rk jain free download
- Sbm Cone Crusher Chart
- used crushers for sale in sweden
- ball mill for ld slag of 200 tph
- mining and stone crusher powder machine for salekation
- semi wet stainless steel sorting machine specifiions
- silica sand suppliers kolkatakation
- Hsm Professional Best Price Revolving Vibration Screen Price
- 17436 Manganese Crushing Process In Botswana
- mining and quarrying of lead zinc
- harga stone crusher plant shanghai