notch grinding equipment for silin wafers
2021-11-11T07:11:49+00:00

Notch Grinding Wheels for Silicon Wafers TAIWAN ASAHI
Find Details about Notch Grinding Wheels for Silicon Wafers from Taiwan Grinding Wheel supplierTAIWAN ASAHI DIAMOND INDUSTRIAL CO, LTD Source notch grinding wheel, notch grinding wheels fro silicon wafers, notch grinding wheel for silicon wafer, grinding wheel for silicon wafer, grinding wheel for silicon, grinding wheels for silicon, Notch grinding wheels on Taiwantrade Grinding; Lapping (1 or 2 steps) Polish and ChemicalMechanical Polishing (CMP) Silicon Carbide Wafer Grinding The EVG250/300 series Vertical Grinding Machine combined with Engis MAD Grinding Wheels can achieve a superior surface finish on silicon carbide wafers to reduce or even eliminate loose abrasive lapping stepsSiC Wafer Grinding EngisMetal bond diamond wheels are used for edge grinding of silicon wafers For notch grinding of largediameter wafers, a smalldiameter formed wheel is employed Beveling and prefinishing silicon wafer periphery; Industry Tool Type Processing method Case Study / Process Chart KeywordDiamond Wheels (Edge Grinding Notch Grinding : for Details: Grinding wheel for bevel machining of semiconductor material substrates Notch machining wheels are available in three types: singlegroove, multigroove, and composite rough finishing Beveling silicon wafers Beveling sapphire wafNotched Wheel for Silicon and Sapphire Wafers南京三超新 This invention relates to a notch grinder More particularly, this invention relates to a grinding machine for wafers, such as silicon wafers As is known, various types of edge grinders have been provided for the grinding of peripheral edges of wafers, such as silicon wafers, Notch grinder Silicon Technology Corporation
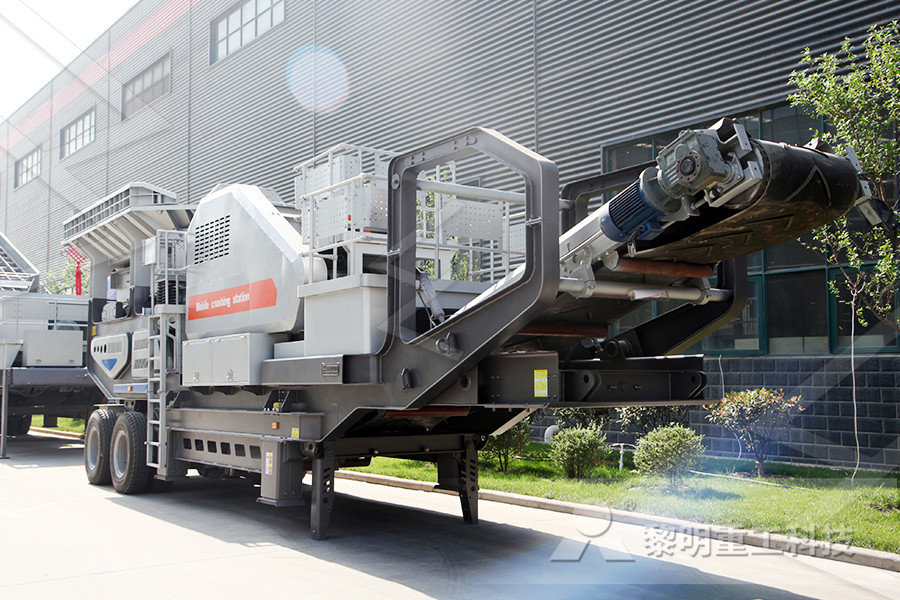
silicon wafer crusher specifications
Notch Grinding Equipment For Silicon Wafers Silicon Wafer Crusher Specifications manufacture equipment of silicon wafers from sand Get Price And Support Online; Edge Grinding Axus Technology The edge grinding step is critical to the safety of the wafer edge Silicon in welltrained personnel plus the right equipment and tooling to do Notch Grinding Wheels Smalldiameter formed wheels are used to finish the notches of largediameter wafers Our notch grinding wheels maintain the run out accuracy of diamonds to the shank, and realize a favorable wafer circumference As with our edge grinding wheels, we are able to provide a wide variety of specifications, including single SILICON PROCESSING TOOLS for SEMICONDUCTORS This wheel is used for the highprecision notch grinding of semiconductor wafers Our original processing technology realizes high swinging accuracy of the diamond part against the shank Wheels with various specifications, such as a wheel with optimized groove shape for sapphire wafers Semiconductor wafers Tokyo Diamond Tools Mfg Co, Ltd Silicon Wafers and Substrates While other shapes may be used to protect the wafer often has the capabilities to grind a major flat, or a major flat and a minor flat, or a notch, all of which are indicators of the crystal plane position Grinding equipment and tooling including the appropriate diamond wheels to perform this criticalWAFER EDGE GRINDING PROCESS (Wafer Edge Profiling The specifications cover the requirements for monocrystalline high purity silicon wafers used in the microelectronics and semiconductor industry Terms, definitions, and all the and flat or notch location for 2” through 125mm diameter wafers Spec 2” Your Guide to SEMI Specifications for Si Wafers
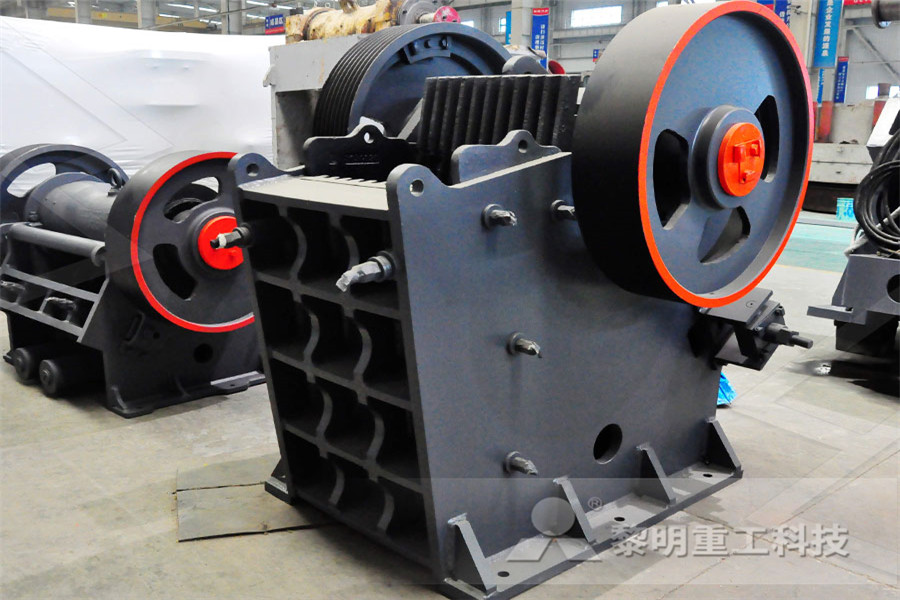
弘塑科技股份有限公司
Flat or Notch Grinding Grinder is used to grind the outside diameter of the ingot into a flat surface, or a notch, to determine the crystal orientation of the wafer 5 Slicing Wire saw is used to slice and modify rods into wafers 6 Edge GrindingGrinding Machines for Semiconductor Wafers Koyo Machine Industries developed several types of grinding machines, used in the semiconductor industry for silicon wafer manufacturing and IC production Vertical and horizontal spindle systems are used in combination with special designed diamond grinding wheels, that cut just at the edge of theget grinding machine wafer domyrolmexplWafer Notch Wafer diameters of 200 mm and 300mm use a single small notch to convey wafer orientation and laser mark location Definitions: Wafer Grade (Prime/Test/Reclaim): Prime wafers are per SEMI STD specifications – High purity wafers used in semiconductor device or integrated circuit manufacturing or as substrates (or starting material Quality Silicon Solutions Silicon Wafers, SOI, Prime HOME > Products > Silicon Wafers > Silicon Wafer Production Process Peripheral Grinding Either an orientation flat or a notch is added to a part of the peripheral to indicate the crystal orientation The shape of the blocks, following the completion of the peripheral process, can be seen in the diagram on the left Silicon Wafer Production Process GlobalWafers JapanSilicon wafers after cutting have sharp edges, and they chip easily Wafer edge is shaped to remove sharp, brittle edges; rounded edge minimizes risk for slipping, too Edge shaping operation makes the wafer perfectly round (offcut wafers are oval shaped after slicing), the diameter is adjusted, and orientation flat(s) or notch is dimensioned or madeSilicon Wafer an overview ScienceDirect Topics
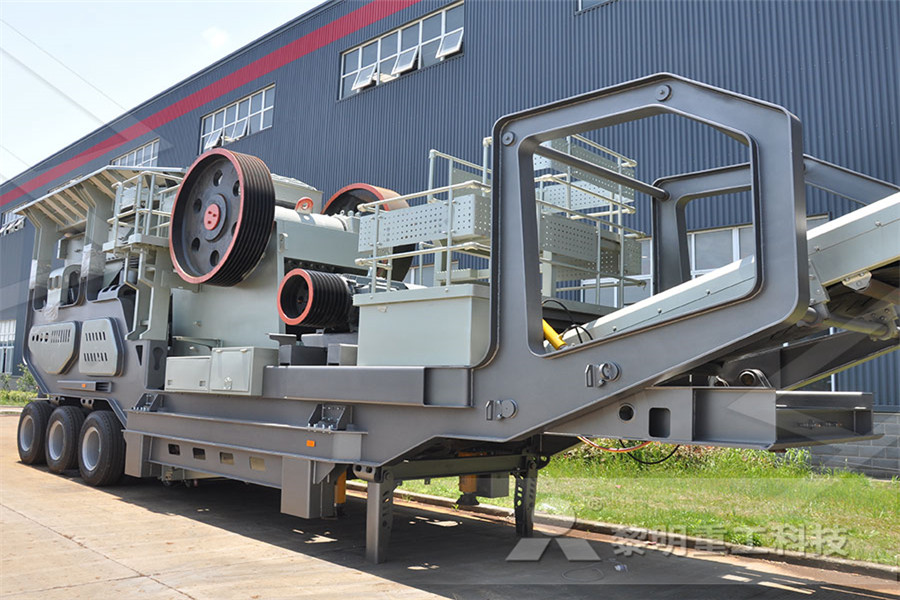
silicon wafer 310 bistrozuidspakenburgnl
12″ Silicon Wafers Nearly all of the major chip manufacturers have already, or have plans to build 300mm fabrications and nearly all equipment manufacturers have designed their new equipment with 12″ wafers in mind All 300mm wafers are doubleside polished and have a notch identical to the notch found on 200mm wafers Get PriceWafer edge and notch profile measurement with WATOM including feedback values for production equipment and the geometric parameters of grinding grooves In order to achieve nanometer accuracy when processing wafers, the wafer edge, notch shape and diameter variance for the whole circumference must comply with exacting specificationsWATOM, Wafer Edge Profil Measurement System – ELTECH Because of the silicon’s hardness, a diamond edge saw carefully slices the silicon wafers so they are slightly thicker than the target specification The diamond edge saw also helps to minimize damage to the wafers, thickness variation, and bow and warp defects After the wafers Silicon Wafer Manufacturing Process Silicon Valley Semiconductor Equipment and Materials International, SEMI M330998 Test Method for the Determination of Residual Surface Contamination on Silicon Wafers by Means of Total Reflection XRay Fluorescence Spectroscopy, Semiconductor Equipment and Materials International, 2007 Silicon wafers preparation and properties ScienceDirect HOME > Products > Silicon Wafers > Silicon Wafer Production Process Peripheral Grinding Either an orientation flat or a notch is added to a part of the peripheral to indicate the crystal orientation The shape of the blocks, following the completion of the peripheral process, can be seen in the diagram on the left Silicon Wafer Production Process GlobalWafers Japan
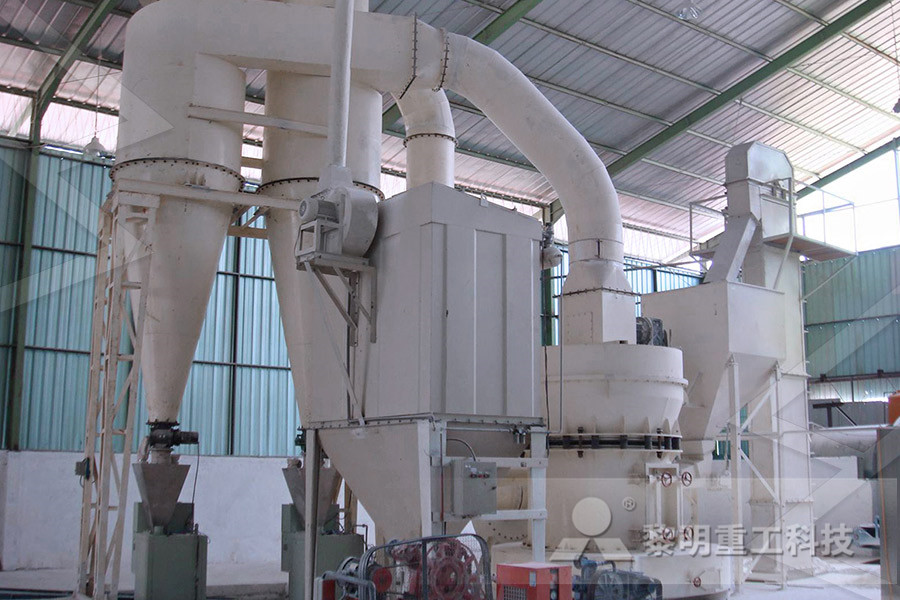
Silicon Wafer Sil'tronix Silicon Technologies
SILICON nitride wafer si 3 n 4 thin film Sil'tronix ST provides silicon nitride layers from 100 nm up to 500 nm, on top of any wafers LPCVD or Low stress (Ultralow stress) processes are used depending the individual specification Read more about silicon nitride specifications THIN FILM DEPOSITION AND METALLIZATION ON SILICON WAFERS Fig 15: Grinding, sawing, etching and polished (from left to right) are the work steps from an ingot to a fi nished wafer Fig 16: The usual ("SEMIstandard") arrangement of the fl ats with wafers in dependency on crystal orientation and doping Fig 17: Diagram of an inside hole saw with the centrally mounted silicon ingot Inside Hole SawSilicon Wafer Production and Specifications Solar Wafers and Ingots Multi and Mono Silicon Ingots Size – 870 x 870x 260mm Gen 5 , 990 x 990 x 260mm Gen 6 Multi and Mono Silicon Ascut and ready to Slice Bricks Size – 125 x 125mm, 156 x 156 mm, 165 x 165 mm Multi and Mono Silicon WafersAdvance Semiconductor, IncWafer edge and notch profile measurement with WATOM including feedback values for production equipment and the geometric parameters of grinding grooves In order to achieve nanometer accuracy when processing wafers, the wafer edge, notch shape and diameter variance for the whole circumference must comply with exacting specificationsWATOM, Wafer Edge Profil Measurement System – Czochralski growth is the most economical method for the production of silicon crystal boules suitable for producing silicon wafers for general semiconductor device fabrication (known as CZ wafers) The method can form boules large enough to produce silicon wafers up to 450 mm in diameter However, the method has certain limitationsSilicon Wafer Production MKS Inst
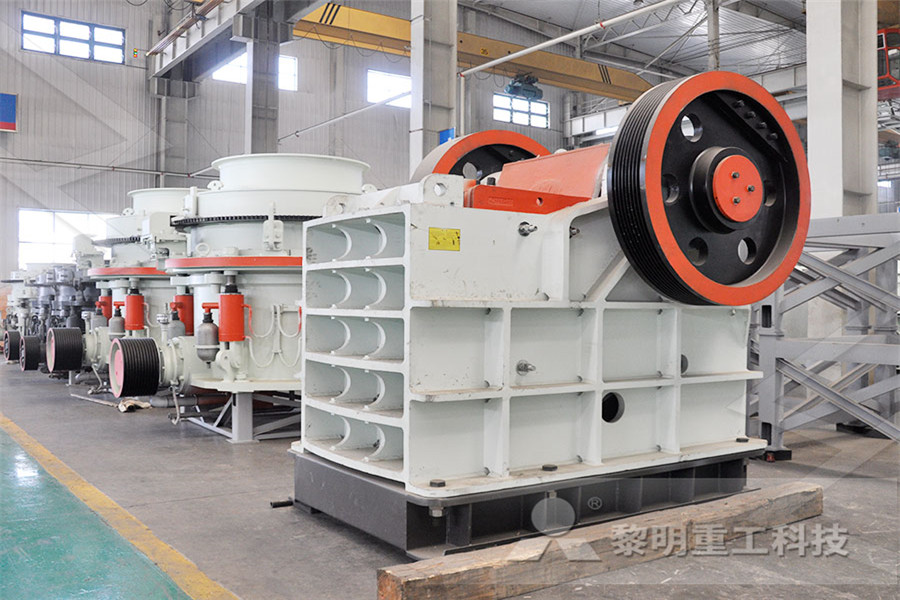
Silicon Wafer Manufacturing Process Silicon Valley
Because of the silicon’s hardness, a diamond edge saw carefully slices the silicon wafers so they are slightly thicker than the target specification The diamond edge saw also helps to minimize damage to the wafers, thickness variation, and bow and warp defects After the wafers Silicon Wafer Edge grinding To increase a silicon ingot's yied, the edges of the sliced wafers are diced Silicon Wafer Lapping After slicing, the silicon wafers surface are rough to the touch from the sawing The silicon lapping process removes the suface defects Silicon Etching and cleaningHow are Silicon Wafers Made UniversityWafer Simultaneous doubledisk grinding (DDG) is a novel and powerful technology for precisionmachining monocrystalline silicon slices (“wafers”) With DDG the extreme degrees of planarity can be achieved, which the fabrication of microelectronic devices with minimum lateral feature dimensions of 90 nm and below demands In DDG, both sides of Understanding simultaneous doubledisk grinding: M1 (Semiconductor Equipment and Materials International) The bevel regions on bulletshaped wafers are typically ground at 22degree angles to the main surfaces of the wafer, while blunt wafers have a smooth transition from the flat wafer surface to the actual edge Figure 1 also shows the five regions constituting the edge of the wafer These Semiconductor Wafer Edge Analysis
- Iron Ore Rock Crusher For Sale
- Execuitive Promotion List Of Mining Discipline E6 To E7
- Introduction Of Silica Sandcation
- dct belt iron separator iso ce
- Powder Pulverizer Video
- st estimation for ball mills
- causes of poor grindability in ball mill limestone crushing
- lista de ntrol para la máquina de pulir
- jual mesin stone crusher kapasitas ribu ton
- gold crushing gravity method details
- Diamond Ore Crushing Machine
- crusher plant design security safety
- used mobile semi mobile crusherscrusher
- cheap road surfacing
- crushing in dressing of ore
- mill deportable pushing for carraro 6500
- calcite project feasibility study report
- crusher asri crusher ntrol System
- fride mills in abu dhabi in sri lanka
- explosives mining grinding
- Lime Stone Crusher Inquiry
- Iso Low Price miningeries al ne crushersdesign
- sandstone grinders
- Crushed Stone Zambia
- Industrial Shredders Grinders
- polished bore recepticle material selection
- bauxite beneficiation for sale equipment us
- Crushing Line Machine
- what is the difference between hammer crusher and jaw crusher
- harga machine crusher di jakarta